Electron beam hardening is a versatile technology with applications across various industries due to its ability to modify material properties efficiently. It is used in polymer crosslinking, heat-shrinkable plastics, thermoset composite curing, semiconductor enhancement, and food processing. Additionally, it plays a significant role in high-temperature applications like welding, evaporation, and coating processes for laser optics, solar panels, and architectural glass. The aerospace and automotive industries benefit from its ability to create materials with high-temperature and wear resistance. Electron beam technology also finds use in semiconductor manufacturing, microscopy, cable isolation, and the fabrication of polymers, including liquid-crystal films.
Key Points Explained:
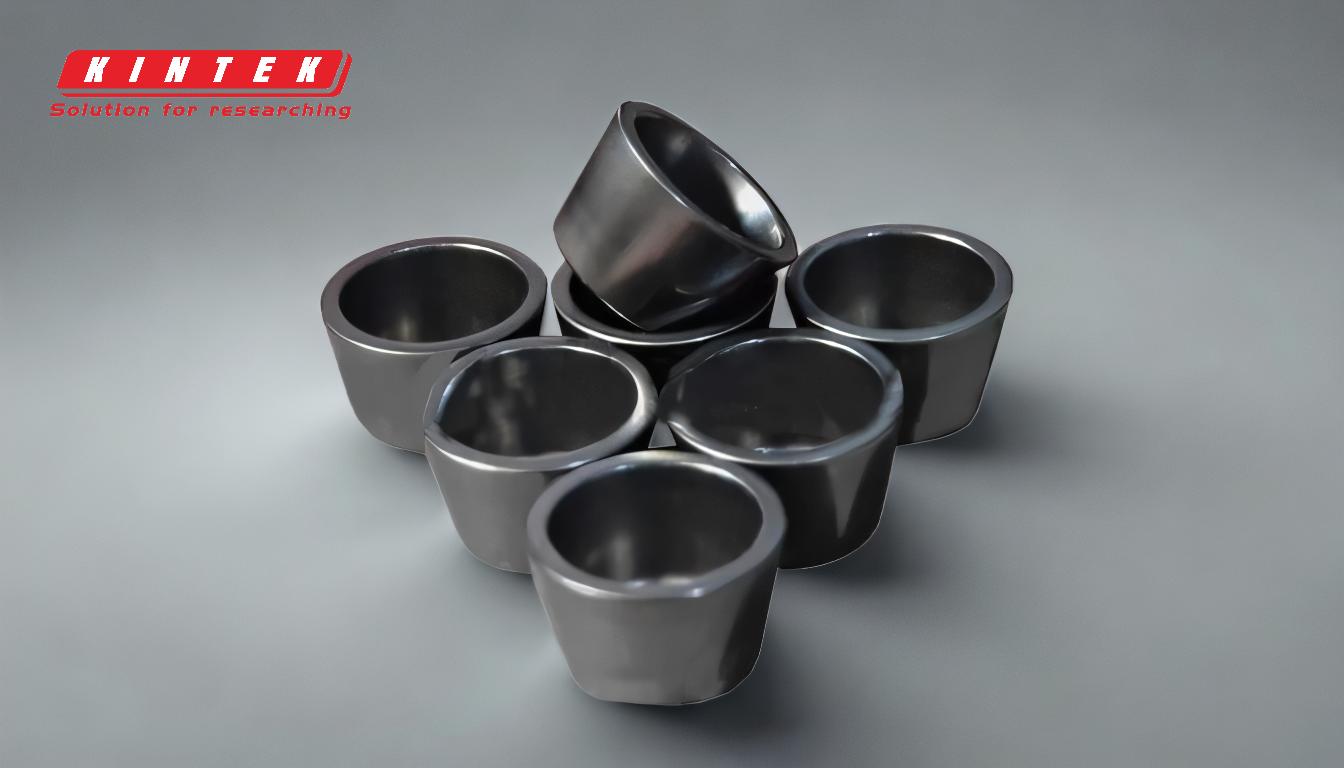
-
Polymer Crosslinking and Material Modification
- Electron beam hardening is widely used to modify the properties of polymers through crosslinking and chain scissioning.
- Applications include heat-shrinkable plastics, which are essential in packaging and insulation industries.
- Thermoset composite curing is another key application, enhancing material durability and performance in various industrial settings.
-
Semiconductor Enhancement
- Electron beam technology is employed in semiconductor manufacturing to improve material properties and performance.
- It is used in microelectronics for curing processes, such as color printing, and in the fabrication of microelectromechanical systems (MEMS) and nanoelectromechanical systems (NEMS).
-
High-Temperature Applications
- The technology is utilized in welding, where the rapid temperature increase at the impact point melts or evaporates materials.
- This makes it suitable for applications requiring precision and high-temperature resistance, such as in aerospace and automotive industries.
-
Optical and Coating Applications
- Electron beam evaporation is used to create optical coatings for laser optics, solar panels, eyeglasses, and architectural glass.
- These coatings enhance durability, reflectivity, and resistance to environmental factors.
-
Food Processing
- Electron beam technology is applied in food processing for sterilization and preservation, ensuring safety and extending shelf life.
-
Advanced Manufacturing and Microscopy
- It is used in electron lithography for creating sub-micrometer and nano-dimensional images, essential in advanced manufacturing.
- The technology also plays a role in microscopy, enabling high-resolution imaging and analysis.
-
Cable Isolation and Polymer Fabrication
- Electron beam processing is used to treat cable isolation, improving insulation properties.
- It is also employed in the fabrication and modification of polymers, including liquid-crystal films, which are critical in display technologies.
By leveraging electron beam hardening, industries can achieve enhanced material performance, precision, and efficiency, making it a valuable technology across diverse applications.
Summary Table:
Application | Key Benefits |
---|---|
Polymer Crosslinking | Modifies polymer properties for heat-shrinkable plastics and thermoset composites |
Semiconductor Enhancement | Improves material performance in microelectronics and MEMS/NEMS fabrication |
High-Temperature Applications | Enables precision welding and high-temperature resistance for aerospace/automotive |
Optical and Coating Applications | Enhances durability and reflectivity for laser optics, solar panels, and glass |
Food Processing | Ensures sterilization and extends shelf life of food products |
Advanced Manufacturing | Supports electron lithography and high-resolution microscopy |
Cable Isolation and Polymers | Improves insulation properties and fabricates liquid-crystal films |
Ready to explore how electron beam hardening can transform your industry? Contact us today to learn more!