Melting temperature, a critical property of materials, plays a pivotal role in various industrial and scientific applications. It is primarily used to liquefy metals, enabling processes like welding, casting, and reshaping. Beyond physical transformations, melting also facilitates the alteration of intrinsic material properties, such as demagnetizing steel by disrupting its atomic structure. This process is indispensable in manufacturing, where it is frequently employed to fuse materials or reform metals, rather than altering their fundamental properties. Understanding the applications of melting temperature helps in selecting appropriate materials and processes for specific industrial needs.
Key Points Explained:
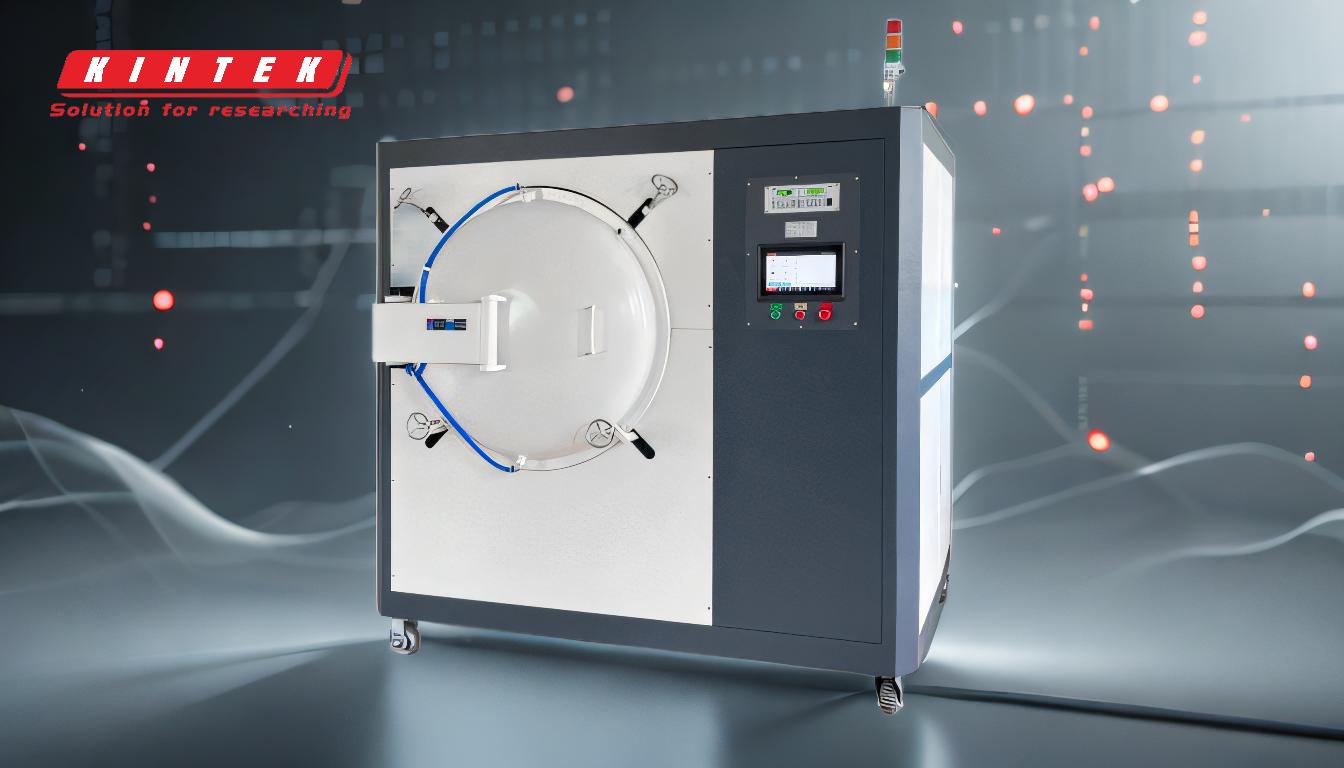
-
Liquefaction of Metals:
- Welding and Joining: Melting temperature is crucial in welding processes where metals are heated to their melting points to fuse them together. This is essential in constructing durable structures and machinery.
- Casting: In casting, metals are melted and poured into molds to create complex shapes and components, which are integral in industries like automotive and aerospace.
-
Reshaping Metals:
- Forming and Fabrication: Metals are often melted to be reshaped into new forms. This is common in the production of metal sheets, wires, and other components that require specific dimensions and properties.
-
Altering Material Properties:
- Demagnetization: By heating magnetized steel to its melting temperature, the atomic structure is disrupted, effectively removing its magnetic properties. This is particularly useful in applications where non-magnetic materials are required.
- Heat Treatment: Melting can be part of heat treatment processes that enhance the mechanical properties of metals, such as hardness, strength, and ductility.
-
Manufacturing Applications:
- Fusion of Materials: In manufacturing, melting is frequently used to fuse two different materials, creating composites with combined properties that are beneficial for specific applications.
- Reforming Metals: Instead of altering the fundamental properties, melting is often used to reform metals into desired shapes and sizes, which is more common in everyday manufacturing processes.
Understanding these applications helps in making informed decisions about material selection and processing techniques, ensuring optimal performance and efficiency in various industrial applications.
Summary Table:
Application | Description |
---|---|
Liquefaction of Metals | - Welding and Joining: Fusing metals for durable structures and machinery. |
- Casting: Creating complex shapes for automotive and aerospace industries. | |
Reshaping Metals | - Forming and Fabrication: Producing metal sheets, wires, and components. |
Altering Material Properties | - Demagnetization: Removing magnetic properties by disrupting atomic structure. |
- Heat Treatment: Enhancing hardness, strength, and ductility of metals. | |
Manufacturing Applications | - Fusion of Materials: Combining properties for specific applications. |
- Reforming Metals: Shaping metals without altering fundamental properties. |
Discover how melting temperature can optimize your industrial processes—contact our experts today!