The Physical Vapor Deposition (PVD) process is a versatile and environmentally friendly coating technique widely used across various industries. It enhances the durability, functionality, and aesthetic appeal of products by depositing thin films of materials onto substrates. PVD coatings are known for their high corrosion resistance, wear resistance, and ability to improve surface hardness. Applications span from consumer goods and automotive components to medical devices and aerospace equipment. The process is also crucial in industries requiring precision, such as microelectronics and semiconductor production, where control over film thickness and composition is essential.
Key Points Explained:
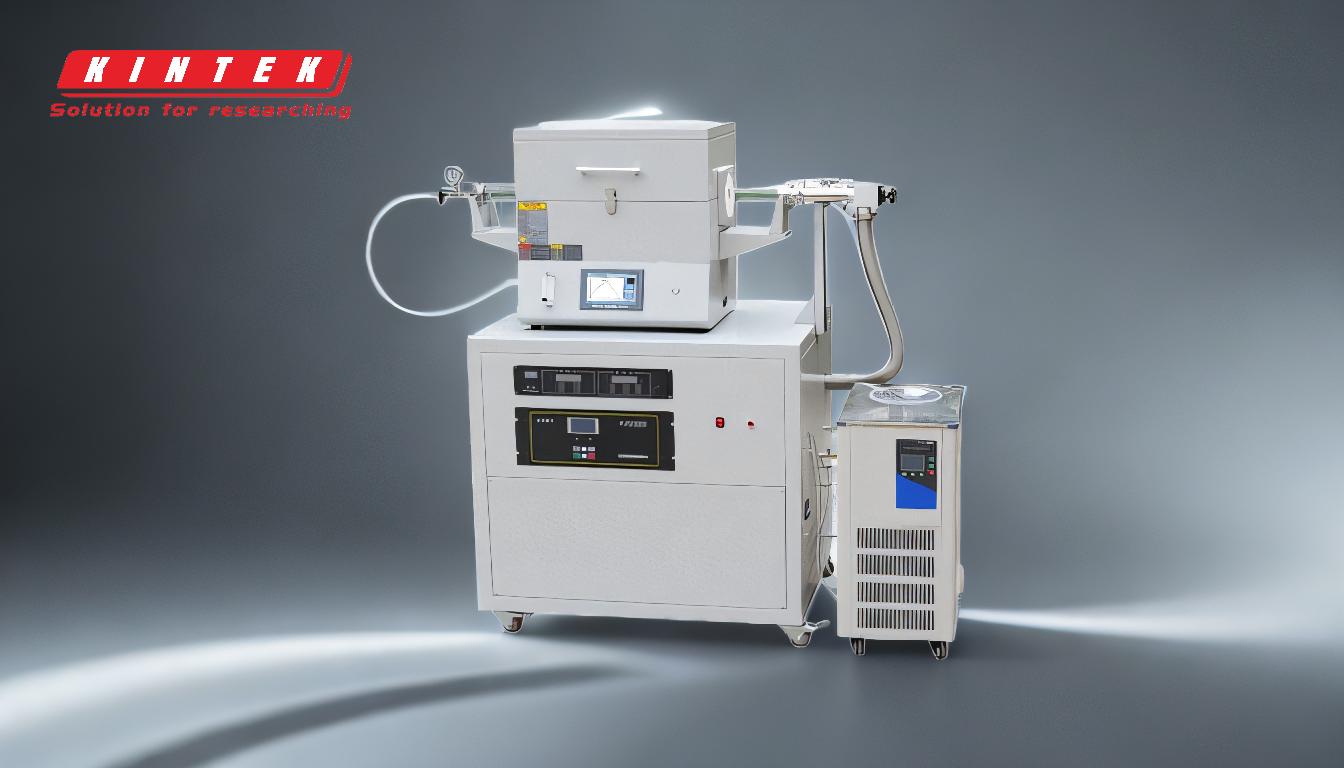
-
Wide Range of Industries Using PVD:
- Consumer Goods: PVD coatings are used to enhance the durability and aesthetic appeal of everyday items such as watches, jewelry, and home hardware like faucets and showerheads.
- Automotive: In the automotive industry, PVD coatings are applied to engine components, cutting tools, and decorative trim to improve wear resistance and longevity.
- Aerospace: The aerospace sector utilizes PVD coatings for their high durability and resistance to extreme conditions, making them ideal for engine parts and other critical components.
- Medical Devices: PVD coatings are used on surgical instruments and implants to enhance their biocompatibility, corrosion resistance, and wear resistance.
- Electronics: In microelectronics, PVD is used to deposit thin films on semiconductors, optical discs, and circuit boards to improve conductivity and durability.
- Sporting Goods and Firearms: PVD coatings are applied to knives, cutting tools, and firearms to enhance their durability, corrosion resistance, and aesthetic finish.
-
Functional and Decorative Applications:
- Functional Coatings: PVD is used to improve the hardness, wear resistance, and chemical resistance of products. This is particularly important in industries like automotive and aerospace, where components are subjected to harsh conditions.
- Decorative Finishes: PVD coatings are also used to create attractive finishes on products such as jewelry, bathroom accessories, and home hardware. The process allows for a variety of colors and finishes, enhancing the visual appeal of the products.
-
Precision and Control in Film Deposition:
- Thin Film Deposition: PVD processes can deposit films with thicknesses ranging from a few nanometers to micrometers, making them suitable for applications requiring precise control over film thickness and composition.
- Multilayer and Graded Composition: PVD is used to create multilayer coatings and graded composition deposits, which are essential in applications requiring specific material properties at different layers.
- Free-Standing Structures: PVD can be used to create free-standing structures, which are useful in advanced manufacturing and nanotechnology applications.
-
Hybrid Techniques and Advanced Applications:
- Hybrid Deposition Techniques: PVD can be combined with other deposition methods to create hybrid coatings that offer enhanced properties, such as improved adhesion or specific mechanical characteristics.
- Semiconductor and Optics Production: PVD is crucial in the production of semiconductors and precision optics, where high-quality films with controlled stoichiometry are necessary for optimal performance.
-
Environmental and Material Benefits:
- Environmentally Friendly: PVD is considered an environmentally sound process because it does not involve harmful chemicals or produce significant waste, making it a sustainable choice for coating applications.
- Material Versatility: PVD can be applied to a wide range of materials, including stainless steel, titanium, and ceramics, allowing for its use in diverse applications across different industries.
In summary, the PVD process is a highly adaptable and valuable technique used across numerous industries for both functional and decorative purposes. Its ability to provide durable, high-quality coatings with precise control over film properties makes it indispensable in modern manufacturing and technology.
Summary Table:
Key Aspect | Details |
---|---|
Industries Using PVD | Consumer goods, automotive, aerospace, medical devices, electronics, etc. |
Functional Applications | Improves hardness, wear resistance, and chemical resistance. |
Decorative Applications | Enhances visual appeal with various colors and finishes. |
Precision & Control | Deposits thin films (nanometers to micrometers) with precise composition. |
Environmental Benefits | Eco-friendly process with minimal waste and no harmful chemicals. |
Learn how PVD coatings can elevate your products—contact our experts today!