Resistance furnaces, including muffle furnaces, box resistance furnaces, and vacuum furnaces, are versatile tools used across a wide range of industries for various high-temperature applications. These furnaces are essential for processes requiring precise temperature control, material isolation, and high thermal efficiency. Industries such as aerospace, metallurgy, ceramics, pharmaceuticals, and electronics rely on resistance furnaces for tasks like heat treatment, sintering, annealing, and quality control. Their ability to handle complex geometries, refractory materials, and specialized processes makes them indispensable in advanced manufacturing, research, and development.
Key Points Explained:
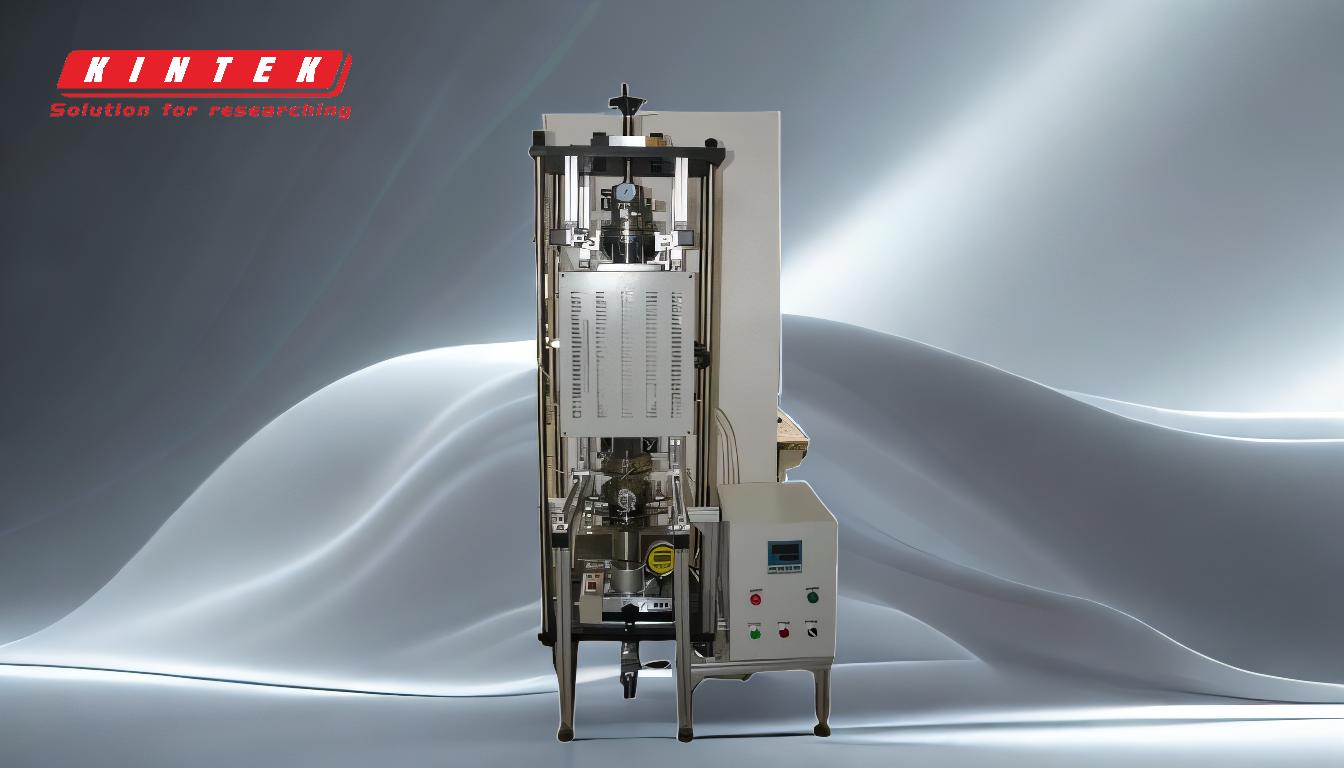
-
Aerospace Industry:
- Resistance furnaces are used for producing critical components like airplane parts, guided missiles, space vehicles, and engines.
- Applications include sintering, heat treatment, and annealing of high-performance materials such as titanium alloys and composites.
- Vacuum furnaces are particularly valuable for ensuring material integrity and precision in aerospace manufacturing.
-
Metallurgy and Powder Metallurgy:
- Resistance furnaces are crucial for sintering powdered metals, creating complex geometries, and producing high-strength components.
- They are used in the production of refractory metals, technical ceramics, and advanced alloys.
- Graphitization furnaces play a key role in producing graphite electrodes, crucibles, and structural components for metallurgical applications.
-
Ceramics and Glass Manufacturing:
- Resistance furnaces are employed for firing, co-firing, and sintering ceramic and glass materials.
- They provide precise temperature control for processes like glass formation, metallizing, and annealing.
- Applications include the production of advanced ceramics for electronics, aerospace, and industrial use.
-
Pharmaceutical and Chemical Industries:
- Muffle furnaces are used for drug inspection, pretreatment of medical samples, and sample processing in analytical chemistry.
- Applications include water quality analysis, environmental analysis, and coal quality analysis (e.g., moisture, ash, and volatile determination).
- These furnaces ensure contamination-free environments for sensitive processes.
-
Battery Manufacturing and Electronics:
- Resistance furnaces are essential for producing battery components, such as cathodes and anodes, through sintering and heat treatment.
- They are used in the electronics industry for firing ceramic substrates and producing high-purity materials.
- Vacuum furnaces are employed for creating precision components in semiconductor manufacturing.
-
Heat Treatment and Quality Control:
- Resistance furnaces are widely used for heat treatment processes like annealing, hardening, and tempering of metals.
- They are integral to quality control laboratories for material testing and analysis.
- Applications include testing the thermal properties of materials and ensuring product consistency.
-
Additive Manufacturing and 3D Printing:
- Resistance furnaces, especially vacuum furnaces, are used in metal additive manufacturing and 3D printing.
- They enable the sintering and post-processing of 3D-printed metal parts, ensuring mechanical strength and dimensional accuracy.
- Applications include producing complex geometries for aerospace, medical devices, and automotive industries.
-
Nuclear and Energy Applications:
- Resistance furnaces are used in nuclear fuel disposal and the production of components for energy systems.
- They play a role in testing and developing materials for high-temperature and high-stress environments.
- Applications include sintering and heat treatment of materials for nuclear reactors and renewable energy systems.
-
Refractory and Building Materials:
- Resistance furnaces are employed in the production of refractory materials, such as bricks and linings for high-temperature applications.
- They are used in the development of new materials for construction and industrial use.
- Applications include firing and testing materials for durability and thermal resistance.
-
Specialized Applications:
- Resistance furnaces are used in niche industries like dental technology for sintering dental implants and prosthetics.
- They are employed in the production of cutting tools, body armor, and other specialized components.
- Applications include brazing, metallizing, and creating ultra-high-temperature materials for defense and industrial use.
In summary, resistance furnaces are indispensable across a wide range of industries due to their ability to provide precise temperature control, material isolation, and high thermal efficiency. Their applications span from advanced manufacturing and research to quality control and specialized material production, making them a cornerstone of modern industrial processes.
Summary Table:
Industry | Key Applications |
---|---|
Aerospace | Sintering, heat treatment, and annealing of titanium alloys and composites. |
Metallurgy | Sintering powdered metals, producing refractory metals, and advanced alloys. |
Ceramics & Glass | Firing, co-firing, and sintering ceramic and glass materials. |
Pharmaceuticals | Drug inspection, medical sample pretreatment, and contamination-free processes. |
Electronics & Batteries | Producing battery components, firing ceramic substrates, and semiconductor manufacturing. |
Heat Treatment | Annealing, hardening, and tempering of metals for quality control. |
Additive Manufacturing | Sintering and post-processing of 3D-printed metal parts. |
Nuclear & Energy | Nuclear fuel disposal and material testing for high-stress environments. |
Refractory Materials | Producing bricks and linings for high-temperature applications. |
Specialized Applications | Dental implants, cutting tools, and ultra-high-temperature material production. |
Discover how resistance furnaces can optimize your industrial processes—contact our experts today!