Thin films play a pivotal role in nanotechnology, offering a wide range of applications due to their unique properties at the nanoscale. These applications span across industries, including aerospace, electronics, energy, and biomedical fields. Thin films are used to enhance mechanical, optical, electrical, and thermal properties, making them indispensable in modern technology. Their ability to reduce materials to atomic sizes and alter surface-to-volume ratios results in improved performance in devices such as solar cells, semiconductors, protective coatings, and sensors. Additionally, thin films are critical in developing advanced memory storage, flexible displays, and energy-efficient solutions like thermal barriers and photovoltaic cells. Their versatility and adaptability continue to drive innovation in nanotechnology.
Key Points Explained:
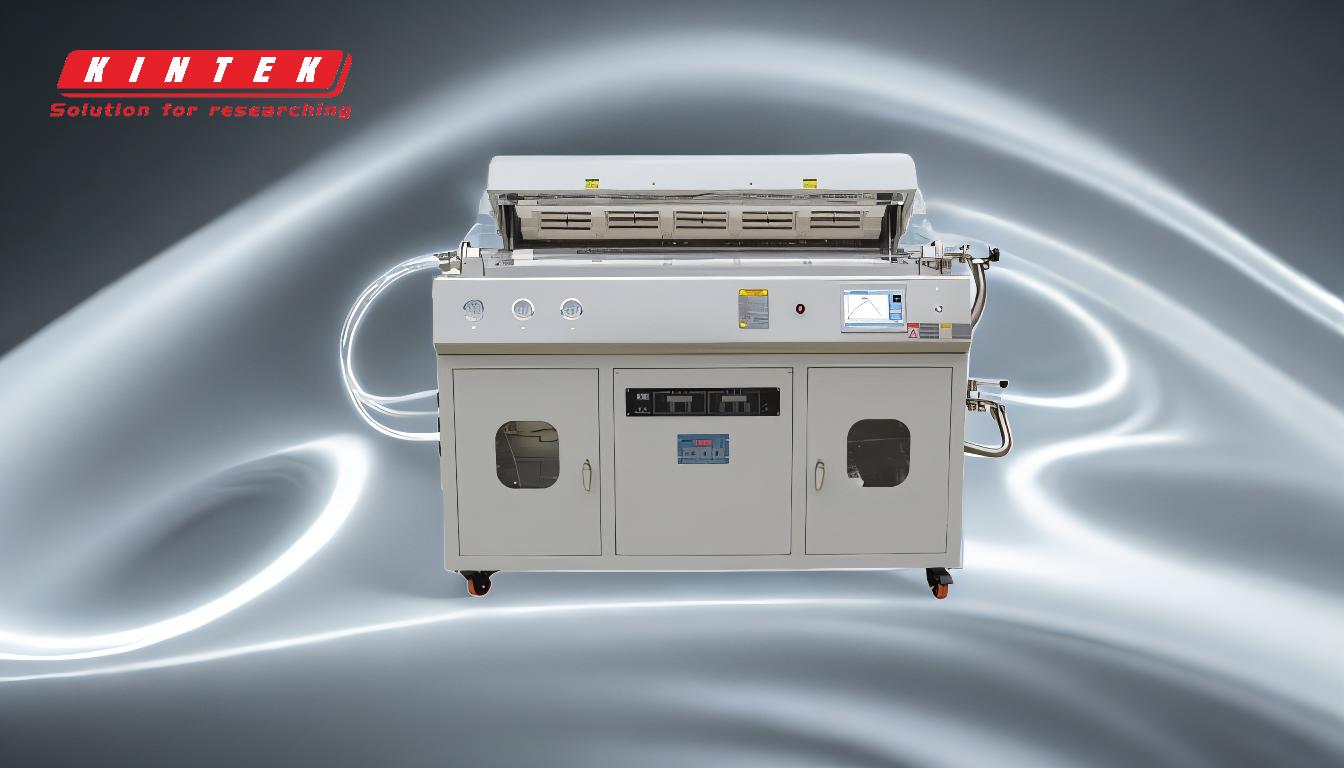
-
Mechanical and Protective Applications:
- Thin films are used to create hard metallic coatings (e.g., chromium films for automobile parts) and wear-resistant layers (e.g., TiN coatings on cutting tools), enhancing durability and performance.
- They provide oxidation resistance, high adherence, and wear protection, making them ideal for industrial tools and machinery.
- Applications include protective coatings to prevent corrosion, decorative layers on jewelry, and wear protection on tools.
-
Optical and Multilayer Coatings:
- Thin films are used in optical multilayer coatings such as distributed Bragg reflectors, notch filters, antireflective coatings, and narrow-bandpass filters.
- They improve the optical properties of ophthalmic lenses, mirrors, and flexible displays.
- Applications include architectural glass for thermal insulation and reflector lamps for enhanced light efficiency.
-
Energy and Semiconductor Applications:
- Thin films are integral to solar cells and thin-film photovoltaic cells, converting light energy into electrical power efficiently.
- They are used in semiconductor devices, where their reduced structure and unique properties improve performance.
- Applications include thermal barriers in aerospace industries and advanced memory storage devices.
-
Biomedical and Sensor Applications:
- Thin films are used in biosensors and plasmonic devices, enabling precise detection and analysis in medical and environmental monitoring.
- They are employed in touch-panel production and head-up displays in the automotive industry, enhancing user interaction and safety.
- Applications include packaging foils for freshness preservation and dactyloscopy for forensic analysis.
-
Emerging and Niche Applications:
- Thin films are used to make objects less visible by bending radiation in various electromagnetic spectrum regions.
- They are applied in flexible displays and decorative coatings, expanding their use in consumer electronics and design.
- New applications are continually emerging, driven by advancements in nanotechnology and material science.
-
Industrial and Technological Versatility:
- Thin films are widely used in coatings, energy conversion, and advanced storage solutions.
- Their ability to improve size effects through techniques like magnetron sputtering makes them essential in nanotechnology.
- Applications include thermal barriers, solar cells, and semiconductor devices, showcasing their adaptability across industries.
In summary, thin films are a cornerstone of nanotechnology, enabling innovations across mechanical, optical, energy, biomedical, and industrial domains. Their unique properties and versatility continue to drive technological advancements and open new possibilities for future applications.
Summary Table:
Application Area | Key Uses |
---|---|
Mechanical & Protective | Hard coatings, wear resistance, corrosion protection, decorative layers |
Optical & Multilayer | Antireflective coatings, flexible displays, architectural glass |
Energy & Semiconductor | Solar cells, thin-film photovoltaics, thermal barriers, memory storage |
Biomedical & Sensors | Biosensors, plasmonic devices, touch panels, packaging foils |
Emerging & Niche | Flexible displays, decorative coatings, radiation bending |
Industrial Versatility | Coatings, energy conversion, advanced storage solutions, semiconductor devices |
Discover how thin films can revolutionize your industry—contact our experts today to learn more!