Vacuum brazing is a specialized joining process that offers numerous advantages over traditional brazing methods, making it highly suitable for industries requiring precision, durability, and environmental sustainability. This process is particularly beneficial in aerospace, automotive, and medical device manufacturing, where high-performance materials and clean, strong joints are essential. The vacuum brazing furnace plays a critical role in this process by creating an oxygen-free environment, preventing oxidation, and ensuring the integrity of the brazed joints. Applications range from micro-channel heat exchangers to aircraft components, highlighting its versatility and importance in modern industrial processes.
Key Points Explained:
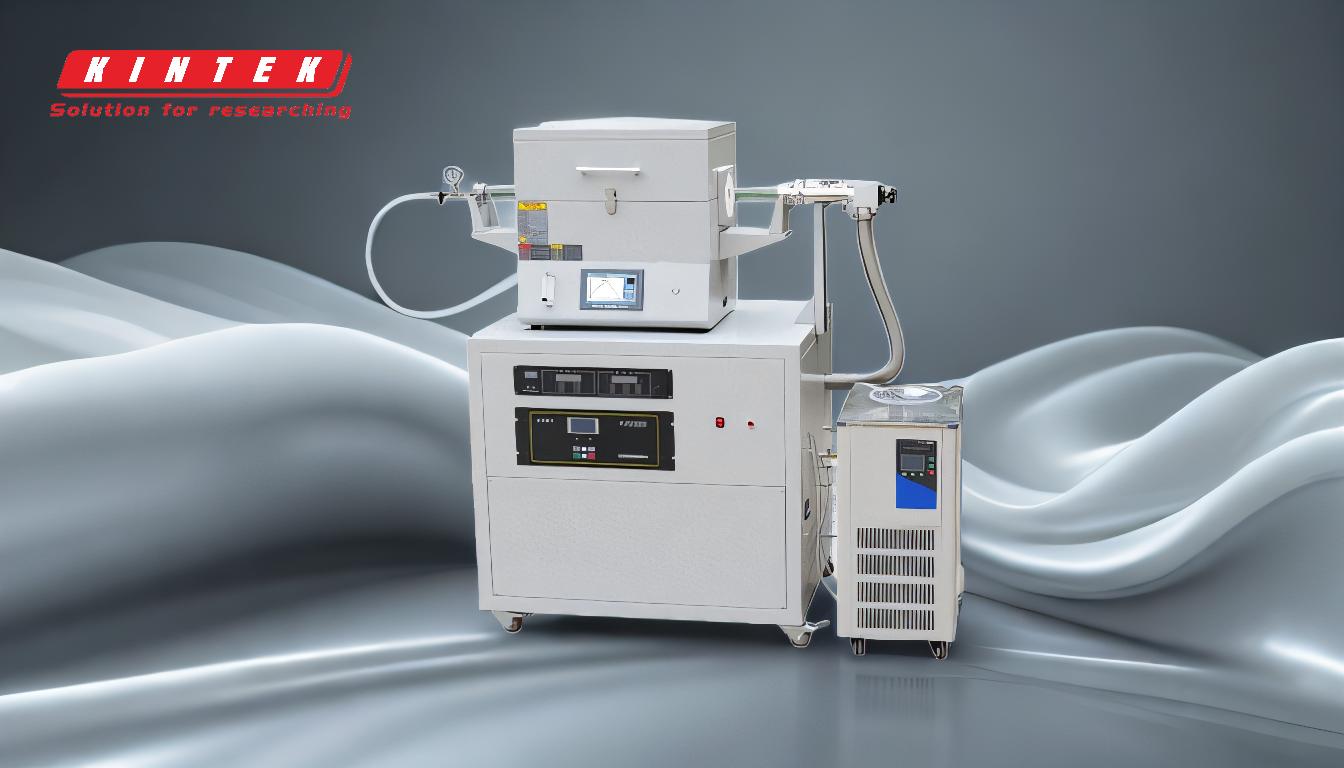
-
How Vacuum Brazing Works:
- Vacuum brazing involves heating workpieces in a vacuum environment, where a liquid filler metal with a lower melting point than the base metal flows into the gaps between the workpieces. This creates a strong, durable bond without the need for flux.
- The vacuum brazing furnace is essential for this process, as it ensures the required vacuum level and precise temperature control, preventing oxidation and contamination of the metals.
-
Applications in Aerospace:
- Vacuum brazing is widely used in the aerospace industry for joining critical components such as turbine blades, heat exchangers, and structural parts. The process ensures high-strength, lightweight joints that can withstand extreme temperatures and stresses.
- The absence of flux and oxide layers in vacuum brazing results in cleaner, more reliable joints, which are crucial for aerospace safety and performance.
-
Applications in Automotive:
- In the automotive sector, vacuum brazing is used for manufacturing components like heat exchangers, sensors, and fuel system parts. The process enhances corrosion resistance and durability, which are essential for vehicle longevity and performance.
- The environmental benefits of vacuum brazing, such as reduced waste and pollution, align with the automotive industry's push toward sustainability.
-
Applications in Medical Devices:
- Medical devices, such as surgical instruments and implants, require precise, contamination-free joints. Vacuum brazing ensures clean, strong bonds without the risk of introducing impurities, making it ideal for this industry.
- The process also allows for the joining of dissimilar materials, which is often necessary in medical device manufacturing.
-
Environmental and Economic Benefits:
- Vacuum brazing is an environmentally friendly process, as it does not emit waste gases or water. This reduces the need for waste treatment and lowers air pollution, aligning with modern environmental standards.
- The process also reduces production costs by eliminating the need for flux and minimizing material waste, making it economically advantageous for manufacturers.
-
Advantages Over Traditional Brazing:
- Vacuum brazing offers superior joint quality, improved corrosion resistance, and better wettability and fluidity of filler metals compared to traditional brazing methods.
- The process is compatible with a wide range of materials, including those that are difficult to braze using conventional methods, such as titanium and nickel-based alloys.
-
Specific Applications:
- Common applications of vacuum brazing include the production of heating and cooling assemblies, micro-channel heat exchangers, aircraft components, sensors, and structural components. These applications benefit from the process's ability to produce clean, strong, and durable joints.
By leveraging the capabilities of a vacuum brazing furnace, industries can achieve high-quality, reliable, and environmentally sustainable results, making vacuum brazing a cornerstone of modern manufacturing processes.
Summary Table:
Industry | Applications | Benefits |
---|---|---|
Aerospace | Turbine blades, heat exchangers, structural parts | High-strength, lightweight, and reliable joints for extreme conditions |
Automotive | Heat exchangers, sensors, fuel system parts | Enhanced corrosion resistance, durability, and environmental sustainability |
Medical Devices | Surgical instruments, implants | Clean, contamination-free joints for precision and reliability |
General | Heating/cooling assemblies, micro-channel heat exchangers, sensors, structural components | Strong, durable, and cost-effective joints for diverse applications |
Learn how vacuum brazing can enhance your manufacturing process—contact our experts today!