Vacuum furnaces are versatile and advanced heat treatment systems widely used across various industries due to their ability to provide a controlled, contamination-free environment. They are essential for processes such as vacuum quenching, brazing, sintering, and magnetic treatment, which enhance material properties like hardness, strength, and wear resistance. Industries such as aerospace, automotive, medical, and energy rely on vacuum furnaces for producing high-performance components with precise temperature control, uniform heating, and energy efficiency. These furnaces are also integral in research and development for studying material behavior under controlled conditions. Their ability to eliminate impurities and oxidation ensures high-quality, durable, and clean products, making them indispensable in modern manufacturing and material processing.
Key Points Explained:
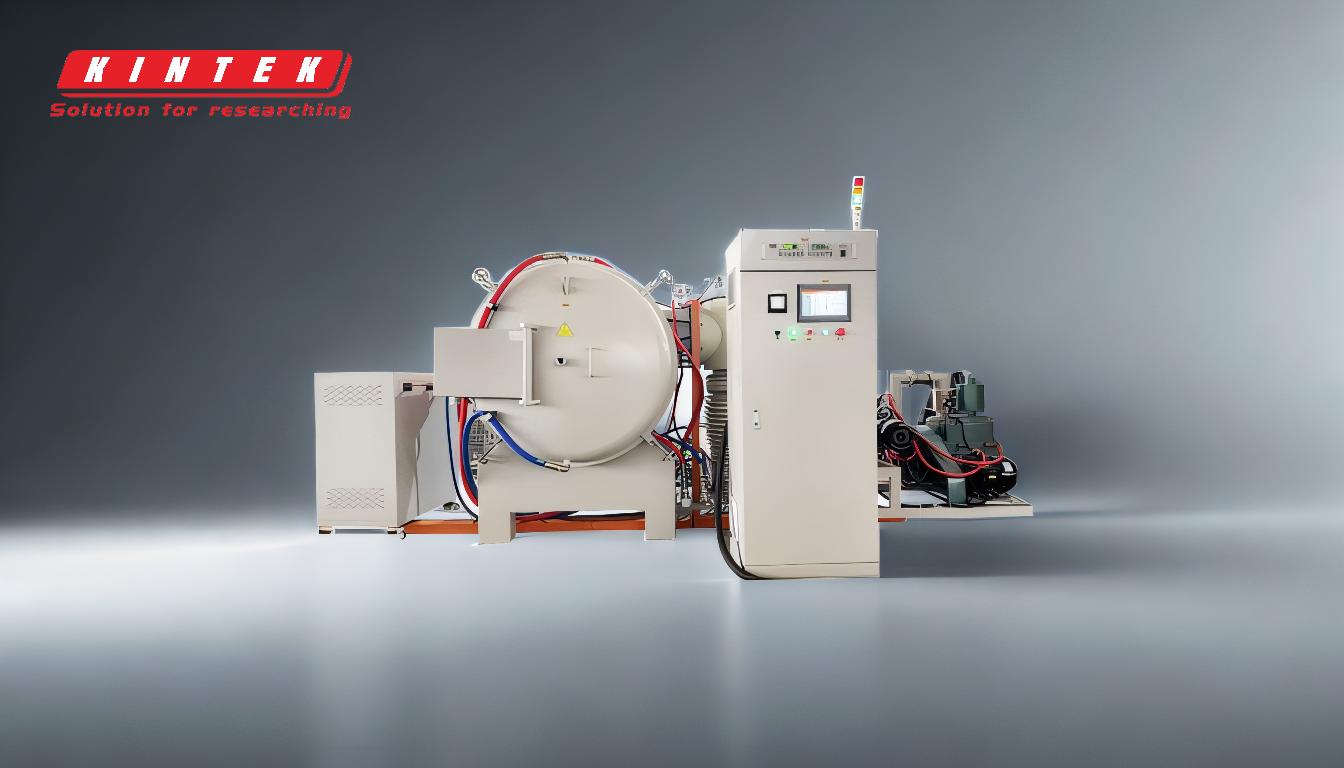
-
Primary Applications of Vacuum Furnaces:
- Vacuum Quenching, Tempering, and Annealing: These processes involve heating materials in a vacuum and then cooling them to achieve desired mechanical properties. The absence of reactive gases ensures no oxidation or contamination, resulting in high-quality, durable components.
- Vacuum Brazing: A welding process where materials are heated to the melting point of a filler metal in a vacuum. This method is ideal for joining complex or delicate components without oxidation or contamination.
- Vacuum Sintering: Used in powder metallurgy, this process involves heating metal powder grains in a vacuum to bond them into solid parts through adhesion and diffusion. It is crucial for producing high-strength, precision components.
- Vacuum Plus Magnetism: This specialized process is used for treating magnetic materials, enhancing their properties for specific applications.
-
Industries Benefiting from Vacuum Furnaces:
- Aerospace: Critical for processing titanium alloys and nickel-based superalloys used in aircraft components, ensuring high strength, durability, and resistance to extreme conditions.
- Automotive: Enhances the performance of gears, bearings, and engine parts by improving hardness and wear resistance.
- Medical and Pharmaceutical: Produces biocompatible and sterile medical devices such as orthopedic implants and surgical instruments.
- Tool and Die: Improves the hardness and wear resistance of molds, dies, and cutting tools.
- Electronics and Semiconductor: Used in processes like diffusion bonding and sintering for high-performance electronic components.
- Energy and Power Generation: Produces turbine blades and heat exchangers with high temperature and corrosion resistance.
- Research and Development: Enables the study of material behavior under controlled thermal conditions, advancing material science and engineering.
-
Advantages of Vacuum Furnaces:
- Controlled Environment: A vacuum furnace provides a clean, impurity-free environment, ensuring high-quality and ultra-clean components.
- Enhanced Material Properties: Processes like quenching and tempering improve hardness, strength, and wear resistance while maintaining dimensional stability.
- Precise Temperature Control: Offers excellent temperature uniformity and stability, ensuring consistent and repeatable results.
- Versatility: Supports various heat treatment processes, including annealing, brazing, sintering, tempering, and hardening.
- Energy Efficiency: Advanced insulation materials and control systems minimize heat loss and optimize energy consumption, making vacuum furnaces environmentally friendly and cost-effective.
-
Technological Features:
- Electromechanical Integration: High integration of mechanical and electrical systems ensures precise control and efficient operation.
- Programmable Workpiece Movement: Pre-programmed adjustments for workpiece movement and air pressure enable customization according to specific process requirements.
- Computer-Controlled Processes: Automation ensures metallurgical repeatability and reduces human error, enhancing productivity and quality.
-
Material and Surface Quality:
- Clean and Bright Surfaces: The vacuum environment eliminates impurities, resulting in clean, bright, and transmutation-free surfaces.
- No Oxidation: High-temperature heating in a vacuum prevents oxidation, preserving the integrity and appearance of materials.
-
Future Trends:
- Sustainability: The focus on low consumption and pollution-free processes makes vacuum furnaces a key component in the development of sustainable manufacturing technologies.
- Advanced Applications: Continued innovation in vacuum furnace technology is expected to expand their use in emerging industries and advanced material processing.
In summary, vacuum furnaces are indispensable in modern manufacturing and material processing due to their ability to provide precise, contamination-free heat treatment. Their applications span across critical industries, enhancing material properties and ensuring high-quality, durable products. With advancements in technology, vacuum furnaces continue to play a pivotal role in driving innovation and sustainability in industrial processes.
Summary Table:
Applications | Industries | Benefits |
---|---|---|
Vacuum Quenching, Tempering | Aerospace, Automotive, Medical | Enhances hardness, strength, and wear resistance; no oxidation or contamination. |
Vacuum Brazing | Aerospace, Electronics | Joins complex components without oxidation; ideal for delicate parts. |
Vacuum Sintering | Tool and Die, Energy | Produces high-strength, precision components through powder metallurgy. |
Vacuum Plus Magnetism | Electronics, Research | Improves magnetic material properties for specialized applications. |
Learn how vacuum furnaces can transform your manufacturing process—contact us today for expert advice!