Heat treatment atmospheres are critical for ensuring the quality and performance of metal parts by preventing contamination, oxidation, and other undesirable reactions during the process. The most common types of atmospheres include inert gases like argon, helium, and nitrogen, as well as controlled atmospheres such as endothermic, exothermic, and ammonia decomposition atmospheres. These atmospheres are tailored to specific heat treatment goals, such as reducing oxidation, controlling carburizing, or ensuring non-carbon heating. Proper atmosphere control is essential in industries like automotive, chemical, and nuclear power, where high temperatures and aggressive environments are common. The choice of atmosphere depends on factors like gas purity, temperature, and the material being processed.
Key Points Explained:
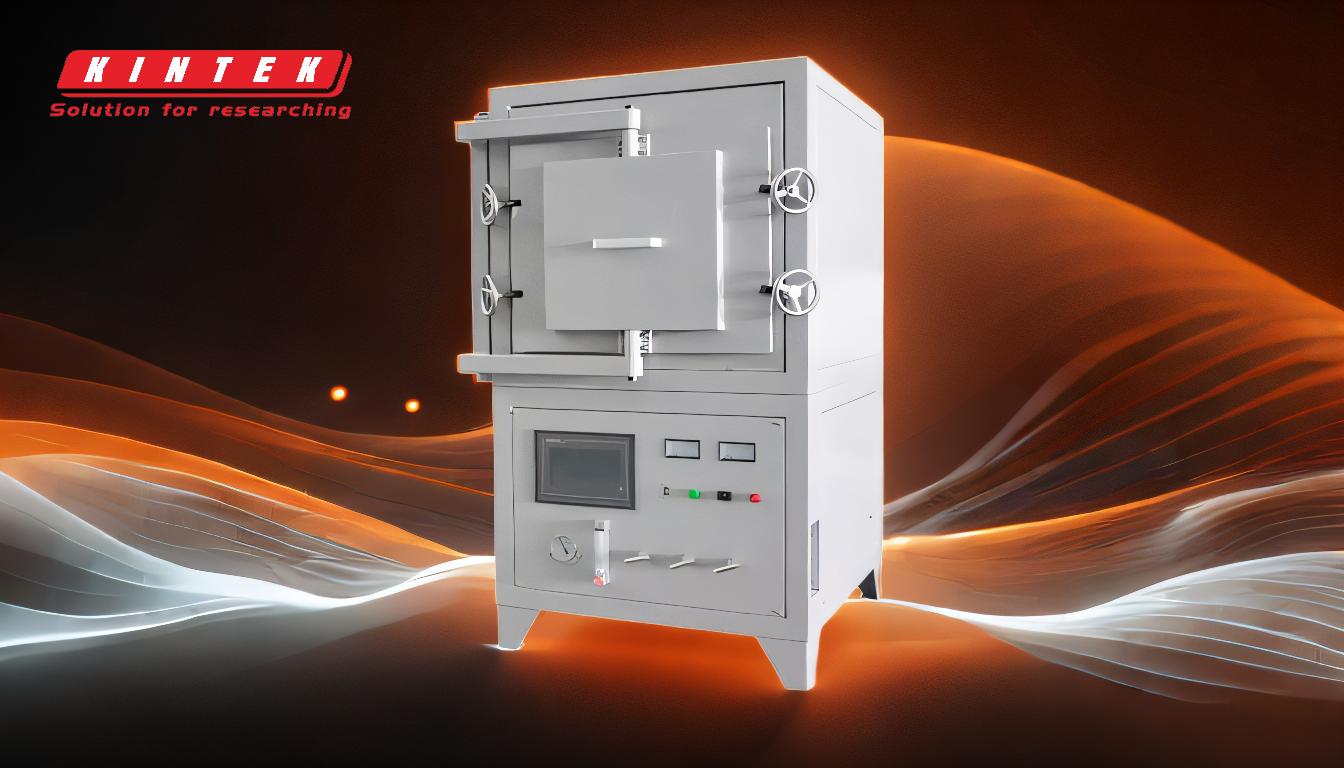
-
Purpose of Heat Treatment Atmospheres:
- Heat treatment atmospheres are designed to protect metal parts from contamination, oxidation, and other chemical reactions during heating.
- They ensure the alloy retains its desired properties, such as strength, ductility, and dimensional stability.
- Without proper atmosphere control, parts may become brittle, corroded, or otherwise damaged, leading to quality issues and potential safety risks.
-
Types of Atmospheres:
- Inert Atmospheres: These include gases like argon (Ar), helium (He), and nitrogen (N₂), which are chemically non-reactive. They are used to prevent oxidation and contamination.
-
Controlled Atmospheres: These are tailored to specific heat treatment processes and include:
- Endothermic Atmosphere: Produced by partially combusting natural gas with air, it is used for processes like carburizing and neutral hardening.
- Exothermic Atmosphere: Created by fully combusting natural gas with air, it is used for annealing and other processes requiring a reducing environment.
- Purified Exothermic Atmosphere: A refined version of exothermic atmosphere, used for high-purity applications.
- Drip-Type Atmosphere: Generated by introducing organic liquids into the furnace, used for carburizing and carbon restoration.
- Ammonia Decomposition Atmosphere: Produced by breaking down ammonia into nitrogen and hydrogen, used for nitriding and other specialized processes.
-
Importance of Atmosphere Control:
- Controlled atmospheres ensure consistency in heating, leading to parts that meet quality standards.
- They prevent unwanted chemical reactions, such as oxidation or decarburization, which can compromise the mechanical properties of the metal.
- In industries like automotive, chemical, and nuclear power, where parts are exposed to extreme conditions, proper atmosphere control is critical to avoid part failure and ensure safety.
-
Factors Influencing Atmosphere Choice:
- Material Being Processed: Different metals and alloys require specific atmospheres to achieve desired properties.
- Temperature: The reactivity of gases changes with temperature, so the atmosphere must be chosen accordingly.
- Gas Purity: Higher purity gases are needed for sensitive applications to avoid contamination.
- Process Goals: The atmosphere must align with the heat treatment objectives, such as reducing oxidation, controlling carburizing, or ensuring non-carbon heating.
-
Equipment for Controlled Atmospheres:
- Controlled Atmosphere Ovens/Furnaces: These are tightly sealed to prevent external interference and maintain consistent gas compositions and temperatures.
- Atmosphere Generators: Devices like endothermic and exothermic generators produce the required gases for specific heat treatment processes.
-
Applications of Heat Treatment Atmospheres:
- Automotive Industry: Used for hardening gears, bearings, and other critical components.
- Aerospace Industry: Ensures high-performance parts can withstand extreme conditions.
- Nuclear Power: Protects components from aggressive chemicals and high pressures.
- Tool Manufacturing: Enhances the durability and performance of cutting tools and dies.
By carefully selecting and controlling the heat treatment atmosphere, manufacturers can produce high-quality parts with consistent mechanical properties, ensuring reliability and safety in demanding applications.
Summary Table:
Aspect | Details |
---|---|
Purpose | Prevent contamination, oxidation, and chemical reactions during heating. |
Types of Atmospheres | Inert (Ar, He, N₂), Endothermic, Exothermic, Ammonia Decomposition, etc. |
Importance | Ensures consistent quality, prevents part failure, and enhances safety. |
Factors Influencing Choice | Material, temperature, gas purity, and process goals. |
Applications | Automotive, aerospace, nuclear power, and tool manufacturing. |
Optimize your heat treatment processes with the right atmosphere—contact our experts today!