Microwave plasma processes, such as plasma nitriding, offer significant advantages in material surface engineering. These processes enhance material properties by forming a hard, wear-resistant layer with compressive stresses, which improves surface hardness, fatigue strength, and resistance to wear, abrasion, and galling. This makes microwave plasma processes highly beneficial for industries requiring durable and high-performance materials.
Key Points Explained:
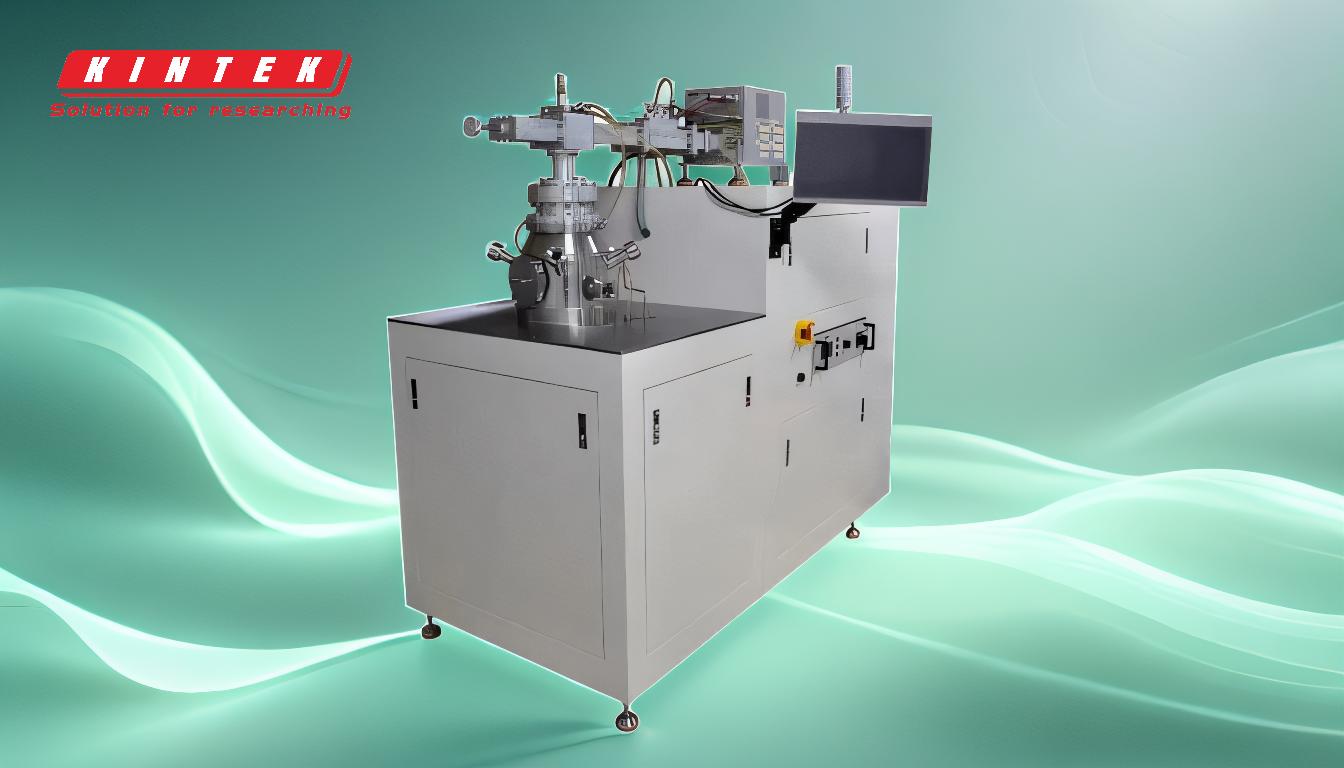
-
Enhanced Surface Hardness:
- Microwave plasma processes, like plasma nitriding, create a hard surface layer on materials. This layer significantly increases the surface hardness, making the material more resistant to wear and tear. The process involves the diffusion of nitrogen into the surface, forming nitrides that contribute to the hardness.
-
Improved Wear Resistance:
- The hard layer formed during the plasma nitriding process is highly resistant to wear. This is particularly beneficial for components subjected to high friction and mechanical stress, such as gears, bearings, and cutting tools. The enhanced wear resistance extends the lifespan of these components, reducing the need for frequent replacements.
-
Increased Fatigue Strength:
- The compressive stresses introduced during the microwave plasma process improve the fatigue strength of materials. Fatigue strength is crucial for components that undergo cyclic loading, as it helps prevent crack initiation and propagation. This leads to a longer service life and improved reliability of the components.
-
Resistance to Abrasion and Galling:
- The process generates surface compressive stresses that are essential for increasing resistance to abrasion and galling. Abrasion resistance is vital for materials exposed to rough surfaces or particulate matter, while galling resistance is important for components in sliding or rotating contact. The microwave plasma process ensures that these properties are significantly enhanced.
-
Controlled and Uniform Treatment:
- Microwave plasma processes offer precise control over the treatment parameters, ensuring uniform treatment across the material surface. This uniformity is crucial for achieving consistent material properties and performance. The ability to control the process parameters also allows for customization based on specific application requirements.
-
Environmentally Friendly:
- Compared to traditional surface treatment methods, microwave plasma processes are more environmentally friendly. They typically involve lower energy consumption and fewer hazardous chemicals, making them a sustainable choice for surface engineering.
-
Versatility in Applications:
- The benefits of microwave plasma processes make them suitable for a wide range of applications across various industries, including automotive, aerospace, tooling, and medical devices. The ability to enhance material properties without compromising the core material integrity is a significant advantage.
In summary, microwave plasma processes, such as plasma nitriding, provide a comprehensive solution for improving material properties. The formation of a hard, wear-resistant layer with compressive stresses enhances surface hardness, wear resistance, fatigue strength, and resistance to abrasion and galling. These benefits, combined with the controlled and uniform treatment, environmental friendliness, and versatility, make microwave plasma processes a valuable technique in material surface engineering.
Summary Table:
Benefit | Description |
---|---|
Enhanced Surface Hardness | Creates a hard surface layer, increasing resistance to wear and tear. |
Improved Wear Resistance | Extends component lifespan by reducing wear in high-friction applications. |
Increased Fatigue Strength | Improves reliability by preventing crack initiation and propagation. |
Resistance to Abrasion | Enhances durability in abrasive environments. |
Resistance to Galling | Prevents surface damage in sliding or rotating components. |
Controlled Treatment | Ensures uniform and customizable surface treatment. |
Environmentally Friendly | Reduces energy consumption and hazardous chemicals compared to traditional methods. |
Versatility | Suitable for automotive, aerospace, tooling, and medical applications. |
Unlock the full potential of microwave plasma processes for your materials—contact our experts today!