Pyrolysis oil, a complex mixture of oxygenated organic compounds, polymers, and water, is one of the primary products of the pyrolysis process. However, pyrolysis also generates several by-products, including biochar, syn-gas (or syngas), and ash. These by-products vary depending on the feedstock and reaction conditions. Biochar, a solid residue rich in carbon, is often used as a soil amendment or for carbon sequestration. Syn-gas, a mixture of combustible gases like CO, CO2, CH4, and H2, serves as a valuable energy source. Ash, a mineral-based material, is typically contained after processing. Additionally, pyrolysis produces non-condensable gases and water, which are by-products of the process. Understanding these by-products is crucial for optimizing the pyrolysis process and maximizing the utility of its outputs.
Key Points Explained:
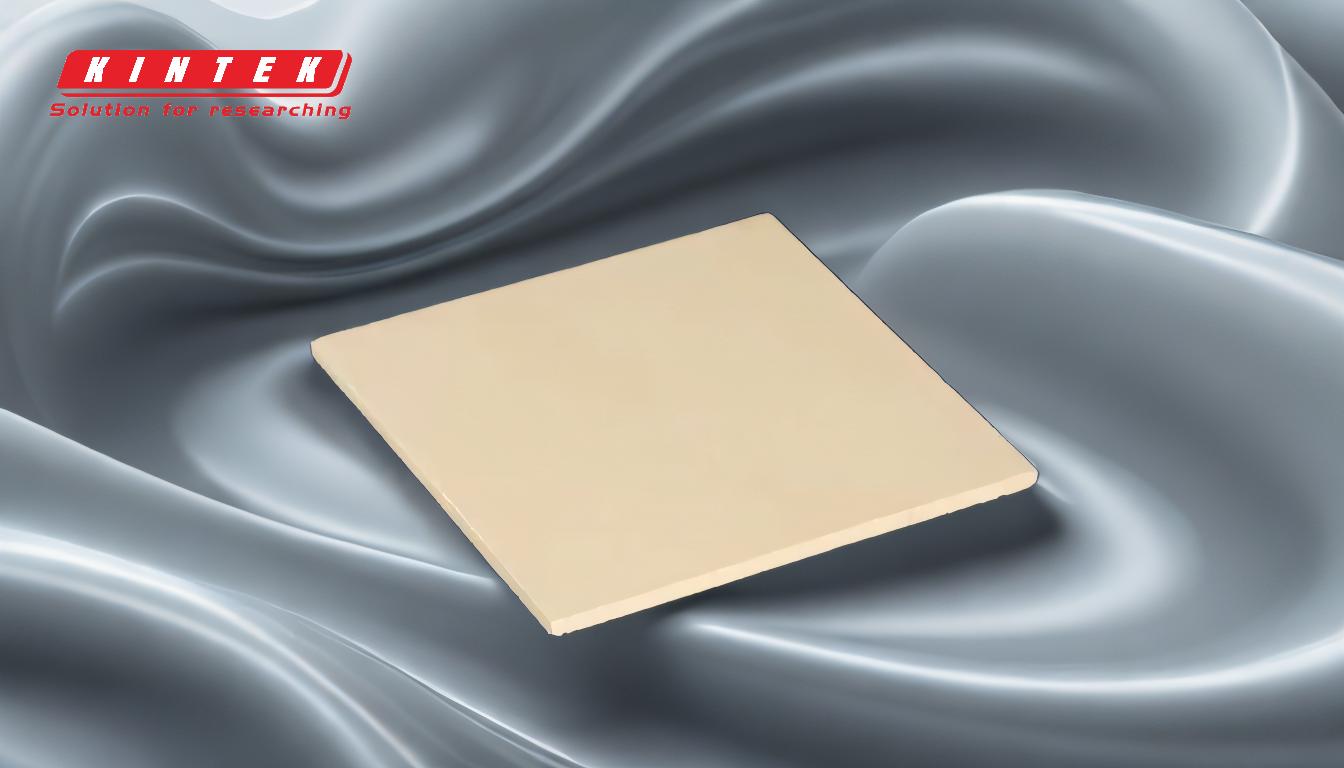
-
Pyrolysis Oil:
- Pyrolysis oil is the primary liquid product of pyrolysis, characterized by its high oxygen content (up to 40% by weight) and complex mixture of oxygenated hydrocarbons.
- It contains low molecular weight compounds like formaldehyde and acetic acid, as well as high molecular weight compounds such as phenols and oligosaccharides.
- The oil is unstable, corrosive, and thermally unstable, making it distinct from petroleum-based fuels.
-
Biochar:
- Biochar is a solid by-product of pyrolysis, consisting of organic matter with high carbon content and ash.
- It is commonly used as a soil amendment to improve soil quality, enhance water retention, and sequester carbon.
- Biochar can also serve as a catalyst support or be processed into activated carbon for various industrial applications.
-
Syn-Gas (Syngas):
- Syn-gas is a mixture of combustible gases produced during pyrolysis, including CO, CO2, CH4, H2, and various hydrocarbons (CnHm).
- It is a valuable energy source and can be used directly in burners or oxidation chambers for heat generation or further processed into fuels.
- The composition of syn-gas varies depending on the pyrolysis temperature and feedstock.
-
Ash:
- Ash is a mineral-based by-product of pyrolysis, typically derived from the inorganic components of the feedstock.
- It must be contained and managed after processing, as it does not have significant commercial value but may contain trace elements or contaminants.
-
Non-Condensable Gases:
- These gases include hydrogen (H2), methane (CH4), carbon monoxide (CO), carbon dioxide (CO2), and nitrogen (N).
- They are produced at different stages of pyrolysis, with higher temperatures favoring the production of H2 and hydrocarbons.
- These gases can be utilized for energy recovery or further chemical processing.
-
Water:
- Water is a by-product of pyrolysis, produced both during the reaction and the initial drying stage of the feedstock.
- It is often separated from the bio-oil and can be treated or reused in the process.
-
Other Solid Residues:
- Depending on the feedstock, pyrolysis may produce other solid residues, such as steel wire (in the case of tire pyrolysis) or char from specific organic materials.
- These residues can be recycled or repurposed for industrial applications.
By understanding these by-products, stakeholders can better design pyrolysis systems to maximize resource recovery and minimize waste, making the process more sustainable and economically viable.
Summary Table:
By-Product | Description | Applications |
---|---|---|
Pyrolysis Oil | Primary liquid product with high oxygen content, unstable and corrosive | Fuel alternative, chemical feedstock |
Biochar | Solid residue rich in carbon | Soil amendment, carbon sequestration, catalyst support |
Syn-Gas (Syngas) | Mixture of combustible gases (CO, CO2, CH4, H2) | Energy source, fuel production |
Ash | Mineral-based residue from inorganic components | Limited commercial value, requires containment |
Non-Condensable Gases | Gases like H2, CH4, CO, CO2, N2 | Energy recovery, chemical processing |
Water | By-product from reaction and drying stages | Treated or reused in the process |
Other Solid Residues | Residues like steel wire or char from specific feedstocks | Recycled or repurposed for industrial use |
Ready to optimize your pyrolysis process? Contact us today to learn more about maximizing resource recovery!