Physical Vapor Deposition (PVD) is a versatile and widely used technique for depositing thin films and coatings on various substrates. It involves the transformation of a solid target material into a vapor phase, which is then transported in a vacuum environment and condensed onto a substrate to form a thin film. The process is characterized by its ability to produce high-purity, durable coatings with precise control over thickness and composition. PVD is environmentally friendly, does not require heat treatment, and is suitable for applications requiring tight tolerances. The coatings replicate the substrate's finish and are applied without excessive build-up, making PVD ideal for industries such as aerospace, automotive, and electronics.
Key Points Explained:
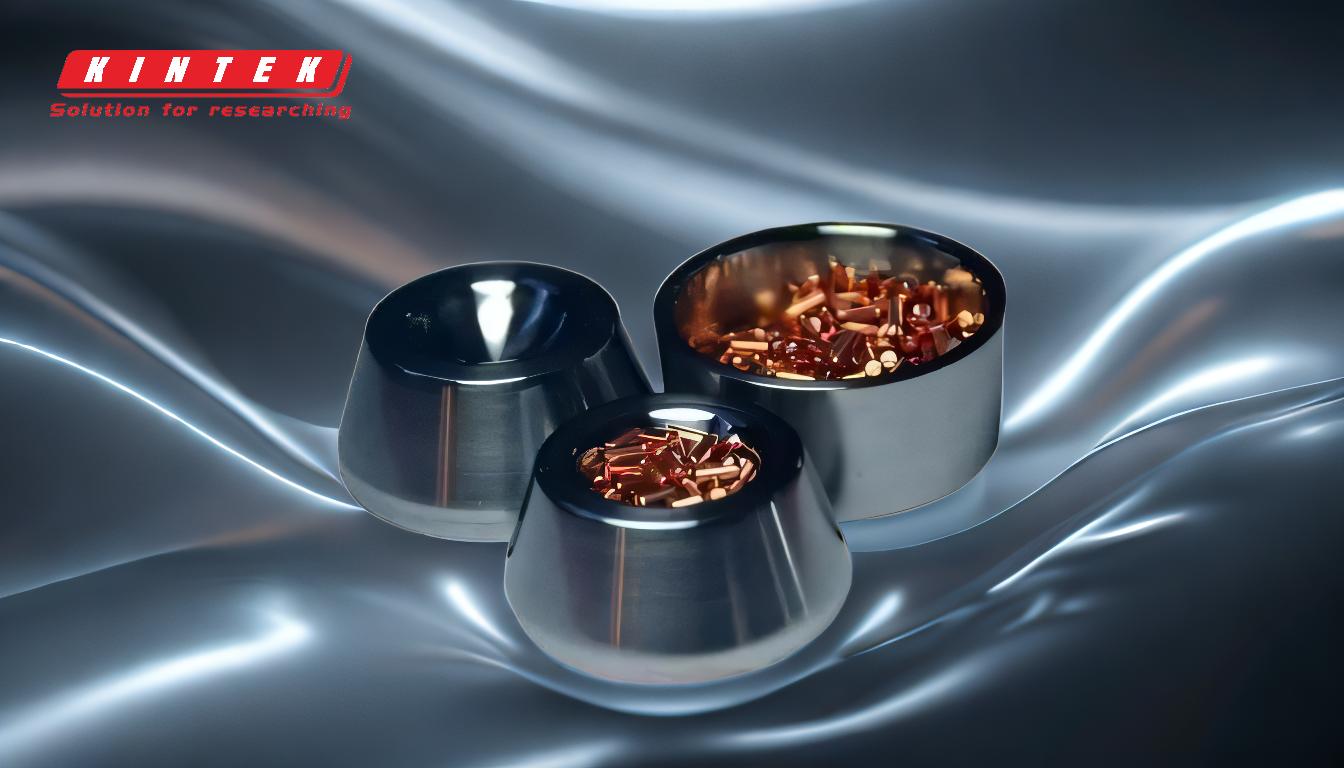
-
Processed in a Vacuum Chamber:
- PVD is conducted in a vacuum environment to ensure the purity of the coating and to prevent contamination from atmospheric gases.
- The vacuum chamber allows for precise control over the deposition process, ensuring consistent and high-quality coatings.
-
Standard Temperature Range:
- The process typically operates at temperatures ranging from 320 to 900 degrees Fahrenheit.
- This temperature range is suitable for a wide variety of materials, including metals, ceramics, and polymers, without causing thermal damage to the substrate.
-
'Line of Sight' Coating Process:
- PVD is a line-of-sight process, meaning that the coating material travels in a straight line from the source to the substrate.
- This characteristic requires careful positioning of the substrate to ensure uniform coating coverage, especially for complex geometries.
-
Physical Bonding:
- The coating material forms a physical bond with the substrate, resulting in strong adhesion and durability.
- This bonding mechanism is different from chemical bonding, which involves chemical reactions between the coating and the substrate.
-
Average Thickness:
- PVD coatings are typically very thin, with an average thickness ranging from 0.00004 to 0.0002 inches.
- Despite their thinness, PVD coatings provide excellent wear resistance, corrosion protection, and other functional properties.
-
Wide Range of Material Usage:
- PVD can be used to deposit a wide variety of materials, including metals, alloys, ceramics, and even some polymers.
- This versatility makes PVD suitable for a broad range of applications, from decorative coatings to functional films in high-tech industries.
-
Recommended for Tight Tolerances:
- PVD is ideal for applications requiring precise control over coating thickness and composition.
- The process is capable of producing coatings with very tight tolerances, making it suitable for high-precision components.
-
No Heat Treatment Required:
- Unlike some other coating processes, PVD does not require post-deposition heat treatment.
- This reduces the overall processing time and minimizes the risk of thermal distortion or damage to the substrate.
-
No Excessive Build-Up:
- PVD coatings are applied in very thin layers, preventing excessive build-up that could alter the dimensions or performance of the substrate.
- This characteristic is particularly important for components with intricate geometries or tight tolerances.
-
Coating Replicates the Finish:
- The PVD process replicates the surface finish of the substrate, maintaining its original texture and appearance.
- This is especially important for decorative applications where the visual quality of the coating is critical.
-
Environmentally Friendly:
- PVD is considered an environmentally friendly process because it does not involve harmful chemicals or produce hazardous waste.
- The process is also energy-efficient, as it operates at relatively low temperatures compared to other coating methods.
-
Improves Surface Quality:
- PVD coatings enhance the surface properties of the substrate, including hardness, wear resistance, and corrosion resistance.
- These improvements extend the lifespan of the coated components and enhance their performance in demanding environments.
-
Common PVD Processes:
- The most common PVD processes include sputtering, electron beam evaporation, and thermal evaporation.
- Each process has its own advantages and is chosen based on the specific requirements of the application, such as the type of material to be deposited and the desired coating properties.
-
Three-Step Process:
- PVD involves three main steps: vaporization of the coating material, migration of atoms or molecules through the vacuum, and deposition onto the substrate.
- This sequence ensures that the coating material is evenly distributed and adheres well to the substrate.
-
Applications:
- PVD is used in a wide range of industries, including aerospace, automotive, medical devices, electronics, and decorative coatings.
- The process is particularly valued for its ability to produce high-performance coatings that meet stringent industry standards.
In summary, Physical Vapor Deposition (PVD) is a highly versatile and precise coating process that offers numerous advantages, including the ability to produce thin, durable, and high-purity coatings. Its environmentally friendly nature, combined with its ability to improve surface properties and replicate the substrate's finish, makes PVD an essential technology in modern manufacturing and materials science.
Summary Table:
Key Aspect | Details |
---|---|
Process Environment | Conducted in a vacuum chamber to ensure purity and prevent contamination. |
Temperature Range | 320–900°F, suitable for metals, ceramics, and polymers without thermal damage. |
Coating Thickness | 0.00004–0.0002 inches, providing wear and corrosion resistance. |
Material Versatility | Deposits metals, alloys, ceramics, and some polymers. |
Environmental Impact | Eco-friendly, no harmful chemicals or hazardous waste. |
Applications | Aerospace, automotive, medical devices, electronics, and decorative coatings. |
Benefits | Improves surface quality, replicates substrate finish, and requires no heat treatment. |
Learn how PVD can enhance your product's performance—contact our experts today!