Brazing is a widely used joining process that involves melting a filler metal to bond two or more base materials. While it is generally reliable, several common defects can occur during the brazing process, affecting the quality and integrity of the joint. These defects can arise due to improper surface preparation, incorrect brazing parameters, or material incompatibility. Understanding these defects is crucial for ensuring strong, durable, and defect-free brazed joints.
Key Points Explained:
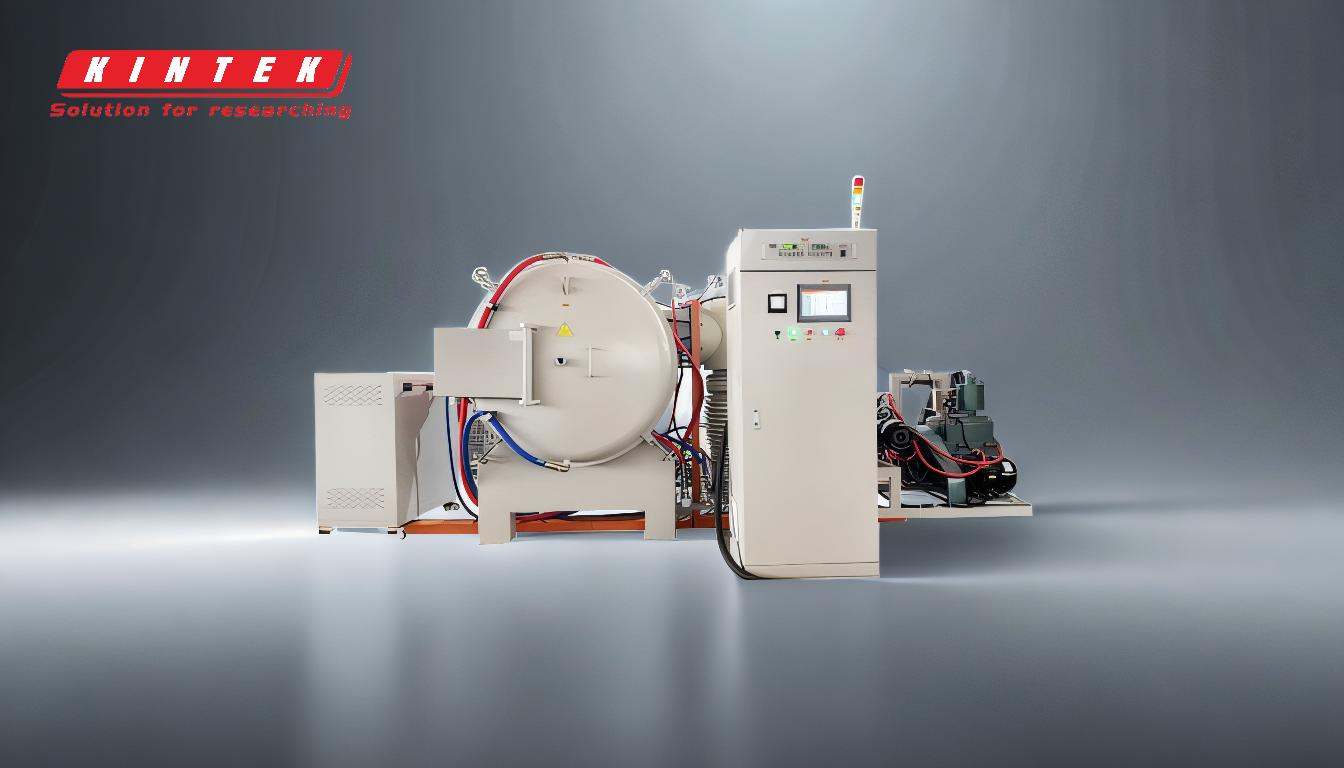
-
Incomplete Joint Filling
- Cause: Incomplete joint filling occurs when the filler metal does not fully flow into the joint gap. This can be due to insufficient heat, improper joint design, or poor surface preparation.
- Impact: This defect weakens the joint, making it prone to failure under stress.
- Solution: Ensure proper joint design with adequate clearance, clean the surfaces thoroughly, and apply sufficient heat to achieve complete filler metal flow.
-
Porosity
- Cause: Porosity refers to the presence of small voids or gas pockets within the brazed joint. It is often caused by trapped gases, contamination, or improper flux application.
- Impact: Porosity reduces the mechanical strength and can lead to leakage in pressurized applications.
- Solution: Use high-quality flux, ensure proper cleaning of the base materials, and control the brazing atmosphere to minimize gas entrapment.
-
Oxidation
- Cause: Oxidation occurs when the base metals or filler metal react with oxygen during the brazing process, forming oxides that inhibit proper bonding.
- Impact: Oxides can prevent the filler metal from wetting the base materials, leading to weak joints.
- Solution: Use a protective atmosphere (e.g., inert gas or vacuum) or apply flux to prevent oxidation during brazing.
-
Cracking
- Cause: Cracking can occur due to thermal stresses, improper cooling rates, or material incompatibility between the base metals and filler metal.
- Impact: Cracks compromise the structural integrity of the joint and can lead to catastrophic failure.
- Solution: Select compatible materials, control the heating and cooling rates, and avoid excessive joint clearance.
-
Erosion
- Cause: Erosion happens when the filler metal dissolves excessive amounts of the base metal, leading to thinning or localized damage.
- Impact: Erosion weakens the base material and can alter the joint's dimensions.
- Solution: Use a filler metal with a lower melting point and limit the brazing temperature and time.
-
Flux Residue
- Cause: Flux residue remains in the joint if the flux is not fully removed after brazing. This can occur due to insufficient cleaning or improper flux application.
- Impact: Flux residue can corrode the joint over time and affect its performance.
- Solution: Thoroughly clean the joint after brazing and use the appropriate amount of flux.
-
Distortion
- Cause: Distortion occurs when the base materials warp or deform due to uneven heating or cooling during the brazing process.
- Impact: Distortion can misalign the joint and affect the assembly's functionality.
- Solution: Use fixtures to hold the components in place, apply uniform heating, and control the cooling rate.
-
Lack of Wetting
- Cause: Lack of wetting happens when the filler metal does not spread evenly over the base material surfaces, often due to contamination or insufficient heat.
- Impact: Poor wetting results in weak and unreliable joints.
- Solution: Clean the surfaces thoroughly, ensure proper flux application, and maintain adequate brazing temperature.
By addressing these common defects through proper process control, material selection, and surface preparation, high-quality brazed joints can be consistently achieved. Regular inspection and testing of brazed components can also help identify and mitigate these issues early in the production process.
Summary Table:
Defect | Cause | Impact | Solution |
---|---|---|---|
Incomplete Joint Filling | Insufficient heat, improper joint design, poor surface preparation | Weakens joint, prone to failure under stress | Ensure proper joint design, clean surfaces, apply sufficient heat |
Porosity | Trapped gases, contamination, improper flux application | Reduces mechanical strength, may cause leakage | Use high-quality flux, clean base materials, control brazing atmosphere |
Oxidation | Reaction with oxygen during brazing | Inhibits proper bonding, leads to weak joints | Use protective atmosphere or flux |
Cracking | Thermal stresses, improper cooling rates, material incompatibility | Compromises structural integrity, risk of catastrophic failure | Select compatible materials, control heating/cooling rates |
Erosion | Filler metal dissolves excessive base metal | Weakens base material, alters joint dimensions | Use lower melting point filler metal, limit brazing temperature/time |
Flux Residue | Insufficient cleaning or improper flux application | Corrodes joint over time, affects performance | Thoroughly clean joint, use appropriate flux amount |
Distortion | Uneven heating or cooling | Misaligns joint, affects assembly functionality | Use fixtures, apply uniform heating, control cooling rate |
Lack of Wetting | Contamination or insufficient heat | Results in weak and unreliable joints | Clean surfaces, ensure proper flux application, maintain adequate heat |
Need help preventing brazing defects? Contact our experts today for tailored solutions!