An induction coil, a critical component in induction heating systems, is designed to generate electromagnetic fields that induce eddy currents in conductive materials, leading to heating or melting. The primary components of an induction coil include the inductor (copper coil), power supply, capacitor, and control system. These elements work together to ensure efficient and precise heating. The inductor, typically made of copper, is the core component that creates the electromagnetic field, while the power supply and capacitor regulate the energy flow. The control system ensures optimal operation and temperature uniformity. Additionally, supporting components like chillers and vacuum units may be integrated for enhanced performance and safety.
Key Points Explained:
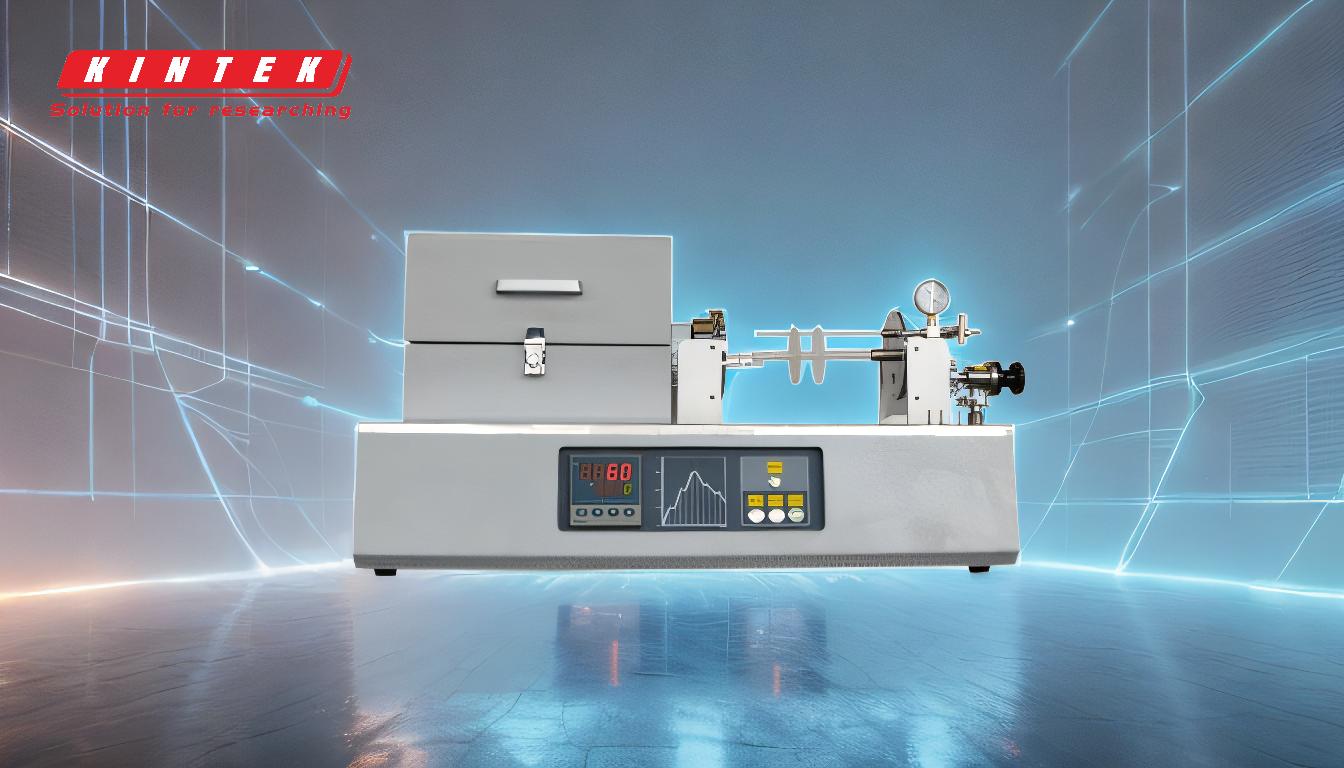
-
Inductor (Copper Coil):
- The inductor is the heart of the induction coil, typically made of high-conductivity copper to minimize energy loss.
- It is designed in various shapes (e.g., helical, pancake, or custom geometries) to suit specific heating applications.
- The inductor generates an alternating electromagnetic field when energized, inducing eddy currents in the workpiece.
-
Power Supply:
- The power supply provides the necessary electrical energy to the inductor.
- Solid-state RF (radio frequency) power supplies are commonly used for their efficiency and precise control over power output.
- The power supply converts standard AC power into high-frequency AC, which is essential for effective induction heating.
-
Capacitor:
- Capacitors are used in conjunction with the inductor to form a resonant circuit, ensuring efficient energy transfer.
- They help match the impedance of the power supply to the inductor, maximizing power delivery and minimizing losses.
- Capacitors also stabilize the system by filtering out unwanted frequencies.
-
Control System:
- The control system regulates the operation of the induction coil, ensuring precise temperature control and uniform heating.
- It monitors parameters such as power input, frequency, and temperature, adjusting them as needed for optimal performance.
- Advanced systems may include automation features for consistent results in industrial applications.
-
Supporting Components:
- Chiller: Used to cool the inductor and other components, preventing overheating and ensuring long-term reliability.
- Vacuum Unit: In some applications, a vacuum environment is required to prevent oxidation or contamination during heating.
- Workpiece: The material being heated or melted, which must be conductive to interact with the electromagnetic field.
By understanding these components, a purchaser can make informed decisions about the design, functionality, and maintenance of induction coils, ensuring they meet specific application requirements.
Summary Table:
Component | Function |
---|---|
Inductor (Copper Coil) | Generates electromagnetic fields, inducing eddy currents for heating. |
Power Supply | Provides electrical energy, converts AC to high-frequency AC for heating. |
Capacitor | Forms a resonant circuit, ensures efficient energy transfer and stability. |
Control System | Regulates operation, ensures precise temperature control and uniformity. |
Supporting Components | Includes chillers, vacuum units, and workpieces for enhanced performance. |
Need help selecting the right induction coil for your application? Contact us today for expert guidance!