A pyrolysis machine is a complex system designed to thermally decompose materials in the absence of oxygen, producing valuable by-products such as oil, gas, and carbon black. The primary components of a pyrolysis machine include the feeding system, pyrolysis reactor, discharging system, syn-gas recycling system, and de-dusting system. These components work together to ensure efficient waste treatment, energy recovery, and compliance with emission standards. The feeding system delivers raw materials to the reactor, where high-temperature pyrolysis occurs, while the discharging system handles the solid residues. The syn-gas recycling system recovers combustible gases for reuse, and the de-dusting system ensures that emissions meet environmental standards. Additional components like the cracking furnace, heating system, and condenser further enhance the system's functionality.
Key Points Explained:
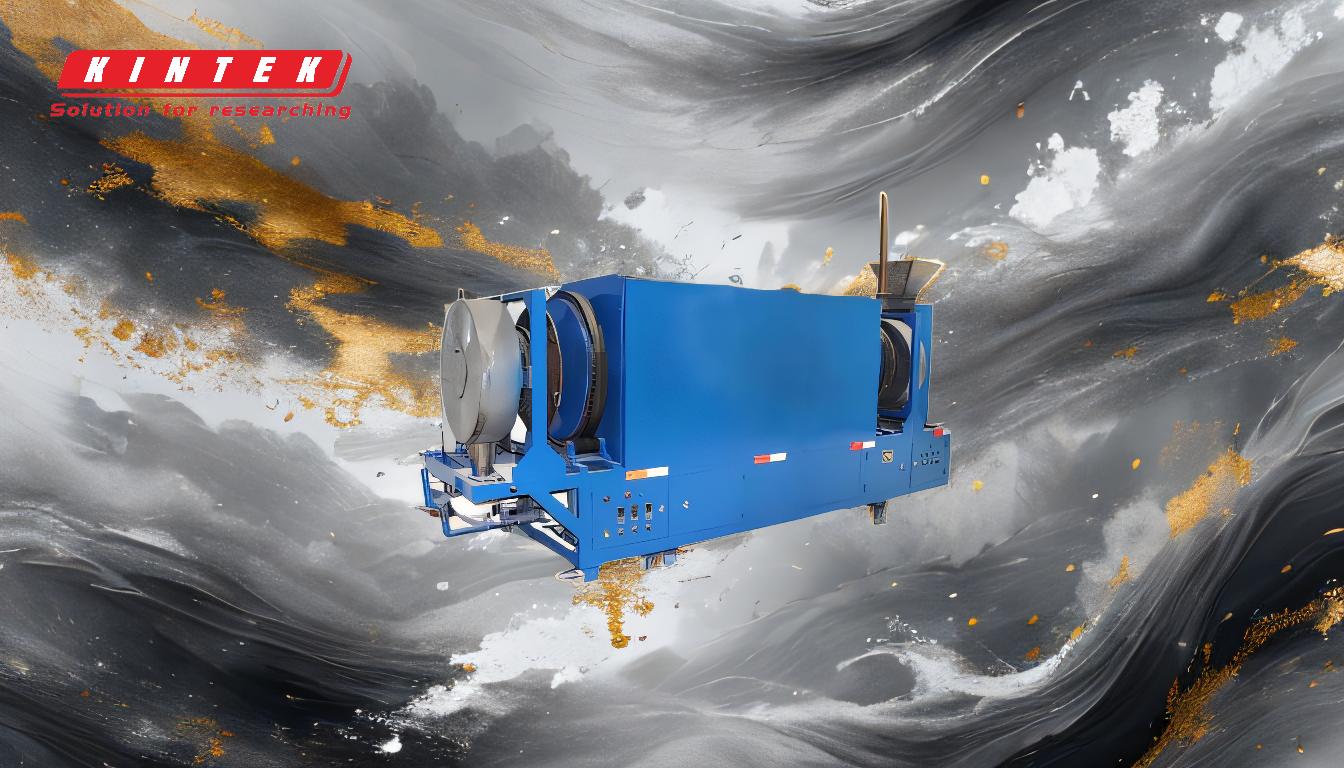
-
Feeding System:
- The feeding system is responsible for delivering raw materials (e.g., waste plastics, tires, or biomass) into the pyrolysis reactor.
- It operates in a fully sealed manner to prevent the escape of gases and ensure safety.
- Automation in the feeding system enhances efficiency and reduces manual labor.
-
Pyrolysis Reactor:
- The reactor is the core component where high-temperature pyrolysis occurs, typically in the range of 300-900°C.
- Inside the reactor, raw materials undergo thermal decomposition, resulting in the breakdown of complex molecules into simpler compounds.
- The reactor is designed to withstand high temperatures and pressures, ensuring durability and safety.
-
Discharging System:
- The discharging system handles the removal of solid residues, such as carbon black, from the reactor.
- It often includes a water-cooling pipe to cool the residues before storage or further processing.
- This system ensures the continuous operation of the pyrolysis machine by efficiently removing by-products.
-
Syn-Gas Recycling System:
- The syn-gas recycling system captures and recycles combustible gases produced during pyrolysis.
- These gases, primarily composed of methane, hydrogen, and carbon monoxide, can be used to heat the reactor, reducing the need for external fuel.
- This system enhances the overall energy efficiency of the pyrolysis process.
-
De-Dusting System:
- The de-dusting system is crucial for purifying the emission gases before they are released into the atmosphere.
- It removes particulate matter and harmful pollutants, ensuring compliance with environmental regulations such as EU emission standards.
- This system is essential for minimizing the environmental impact of the pyrolysis process.
-
Cracking Furnace:
- The cracking furnace is an additional component that facilitates the thermal cracking of larger hydrocarbon molecules into smaller, more valuable ones.
- It works in conjunction with the pyrolysis reactor to enhance the yield and quality of the pyrolysis products.
-
Heating System:
- The heating system provides the necessary thermal energy for the pyrolysis process.
- It can be powered by external fuel sources or by the combustible gases recovered from the syn-gas recycling system.
- Efficient heating is critical for maintaining the optimal temperature within the reactor.
-
Condenser:
- The condenser is used to cool and liquefy the vapor-gas mixture produced during pyrolysis, resulting in the collection of pyrolysis oil.
- In some designs, the condenser may be excluded if the primary goal is to obtain solid residues, and the vapor-gas mixture is burned in the furnace.
- The condenser plays a key role in maximizing the recovery of valuable liquid products.
-
Energy Module (Furnace):
- The energy module, often integrated with the reactor, provides the heat required for the pyrolysis process.
- Some designs combine the reactor and energy module to reduce energy losses, although this may complicate temperature control and require higher-quality materials.
- The energy module is essential for maintaining the continuous operation of the pyrolysis machine.
-
Driving Device, Base, Main Furnace, and Casing:
- The driving device ensures the mechanical operation of the pyrolysis system, such as rotating the reactor in some designs.
- The base provides structural support for the entire system, ensuring stability during operation.
- The main furnace houses the pyrolysis reactor and is designed to withstand high temperatures and pressures.
- The casing encloses the system, providing insulation and protection from external elements.
By understanding these components, a purchaser can make informed decisions about the type of pyrolysis machine that best suits their needs, ensuring efficient waste treatment, energy recovery, and compliance with environmental standards.
Summary Table:
Component | Function |
---|---|
Feeding System | Delivers raw materials into the reactor in a sealed, automated manner. |
Pyrolysis Reactor | Core component for thermal decomposition at 300-900°C. |
Discharging System | Removes solid residues like carbon black, ensuring continuous operation. |
Syn-Gas Recycling System | Captures and recycles combustible gases for energy efficiency. |
De-Dusting System | Purifies emissions to meet environmental standards. |
Cracking Furnace | Enhances product yield by breaking down larger hydrocarbon molecules. |
Heating System | Provides thermal energy for pyrolysis, powered by external or recycled fuel. |
Condenser | Cools vapor-gas mixtures to recover pyrolysis oil. |
Energy Module | Supplies heat for pyrolysis, often integrated with the reactor. |
Driving Device & Base | Ensures mechanical operation and structural stability. |
Ready to optimize your waste treatment process? Contact our experts today to find the perfect pyrolysis machine for your needs!