Induction brazing, while efficient and precise, has several disadvantages that can affect its suitability for certain applications. These include challenges related to material properties, such as the need for precise temperature control due to the close melting ranges of base and filler metals, and the potential for reduced material hardness post-brazing. Additionally, the process can be technically demanding, requiring skilled operators and specialized equipment, which can lead to higher energy consumption and longer processing times. Environmental and cleaning costs before welding also add to the overall expense. These factors must be carefully considered when choosing induction brazing for a project.
Key Points Explained:
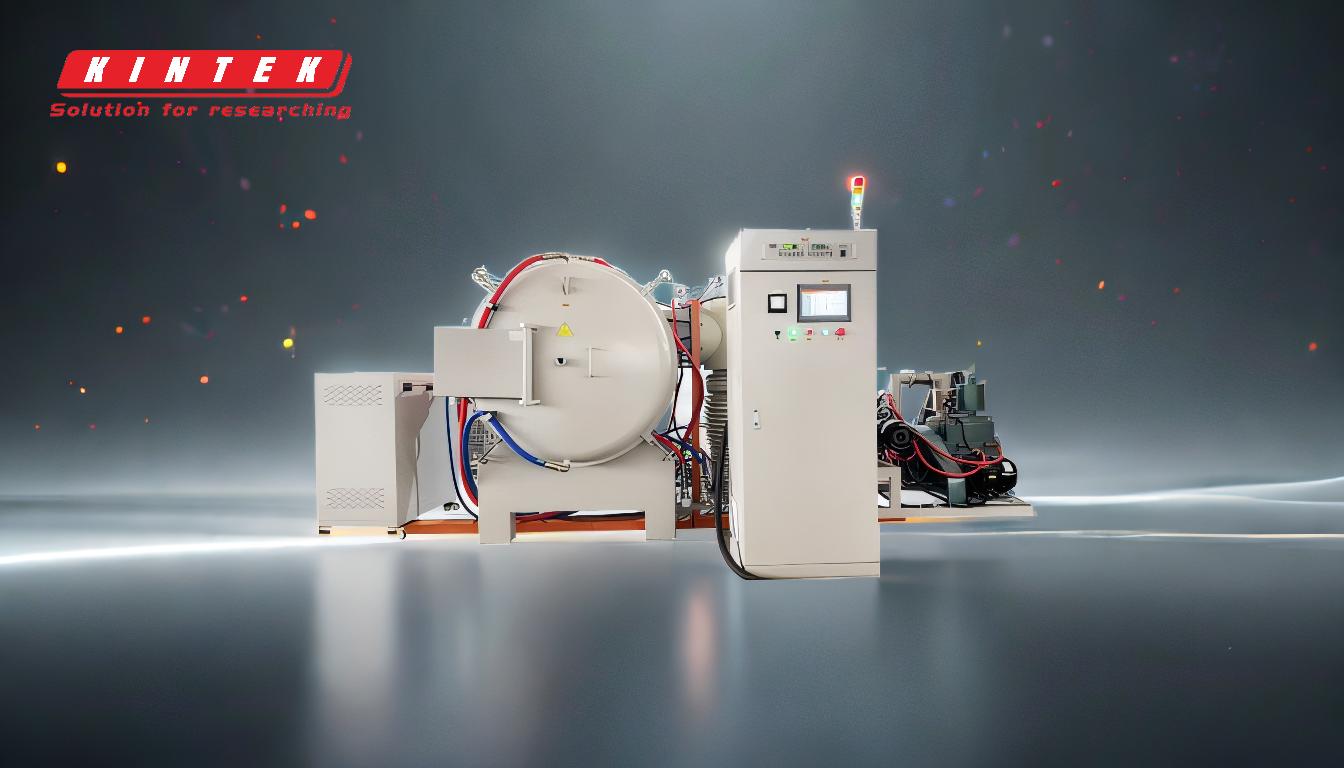
-
Precise Temperature Control and Homogeneous Thermal Distribution:
- Induction brazing requires precise temperature control because the melting ranges of the base and filler metals are often very close. This precision is crucial to prevent overheating or underheating, which can compromise the joint quality. Achieving homogeneous thermal distribution is also challenging, especially for complex geometries, as uneven heating can lead to weak joints or material damage.
-
Material Hardness Reduction:
- High-temperature processes like induction brazing can reduce the hardness of certain materials, particularly metals that undergo annealing or softening at elevated temperatures. This reduction in hardness can affect the mechanical properties of the final product, making it less suitable for applications requiring high strength or wear resistance.
-
Technical Difficulty and Skilled Labor:
- Induction brazing is a technically demanding process that requires skilled operators to manage the equipment and ensure proper joint formation. The complexity of setting up and maintaining the induction coils, along with the need for precise control over heating parameters, makes it less accessible for inexperienced users.
-
High Energy Consumption:
- The process can be energy-intensive, especially for large-scale or continuous operations. The induction coils require significant electrical power to generate the necessary electromagnetic fields for heating, leading to higher operational costs compared to some alternative brazing methods.
-
Long Processing Times:
- While induction brazing is generally faster than furnace brazing, it can still involve longer processing times compared to other methods like torch brazing. This is particularly true for complex assemblies or when multiple joints need to be brazed sequentially, which can slow down production rates.
-
High Cleaning and Environmental Costs:
- Before induction brazing, components often require thorough cleaning to remove oxides, oils, and other contaminants that can interfere with the brazing process. This cleaning process can be costly and time-consuming. Additionally, the environmental impact of using fluxes or cleaning agents must be considered, as they may require special disposal methods or contribute to pollution.
-
Design Constraints:
- Induction brazing necessitates close fits between components to facilitate capillary action, which is essential for proper filler metal flow. This requirement can impose design constraints, as parts must be manufactured to very tight tolerances. Furthermore, the location of the brazing material must be carefully planned during the design phase, adding complexity to the process.
By understanding these disadvantages, purchasers and engineers can make informed decisions about whether induction brazing is the right choice for their specific application, weighing the pros and cons against other brazing methods.
Summary Table:
Disadvantage | Description |
---|---|
Precise Temperature Control | Requires close monitoring to prevent overheating or underheating. |
Material Hardness Reduction | High temperatures can soften metals, reducing strength and wear resistance. |
Technical Difficulty and Skilled Labor | Demands skilled operators and specialized equipment. |
High Energy Consumption | Energy-intensive process, leading to higher operational costs. |
Long Processing Times | Slower than some alternatives, especially for complex assemblies. |
High Cleaning and Environmental Costs | Requires thorough cleaning and may involve environmentally harmful fluxes. |
Design Constraints | Parts must have tight tolerances, adding complexity to design and manufacturing. |
Need help deciding if induction brazing is right for your project? Contact our experts today for personalized advice!