Powder metallurgy is a versatile and efficient manufacturing process that involves the production of metal parts from powdered materials. Key considerations in powder metallurgy include the properties of the metal powders, the process steps involved, and the advantages it offers, such as cost-effectiveness, material efficiency, and the ability to produce complex and high-precision parts. The process is particularly beneficial for industries requiring high-performance materials with exceptional wear resistance, toughness, and hardness retention. Additionally, powder metallurgy is an eco-friendly manufacturing method, with minimal waste and high material utilization.
Key Points Explained:
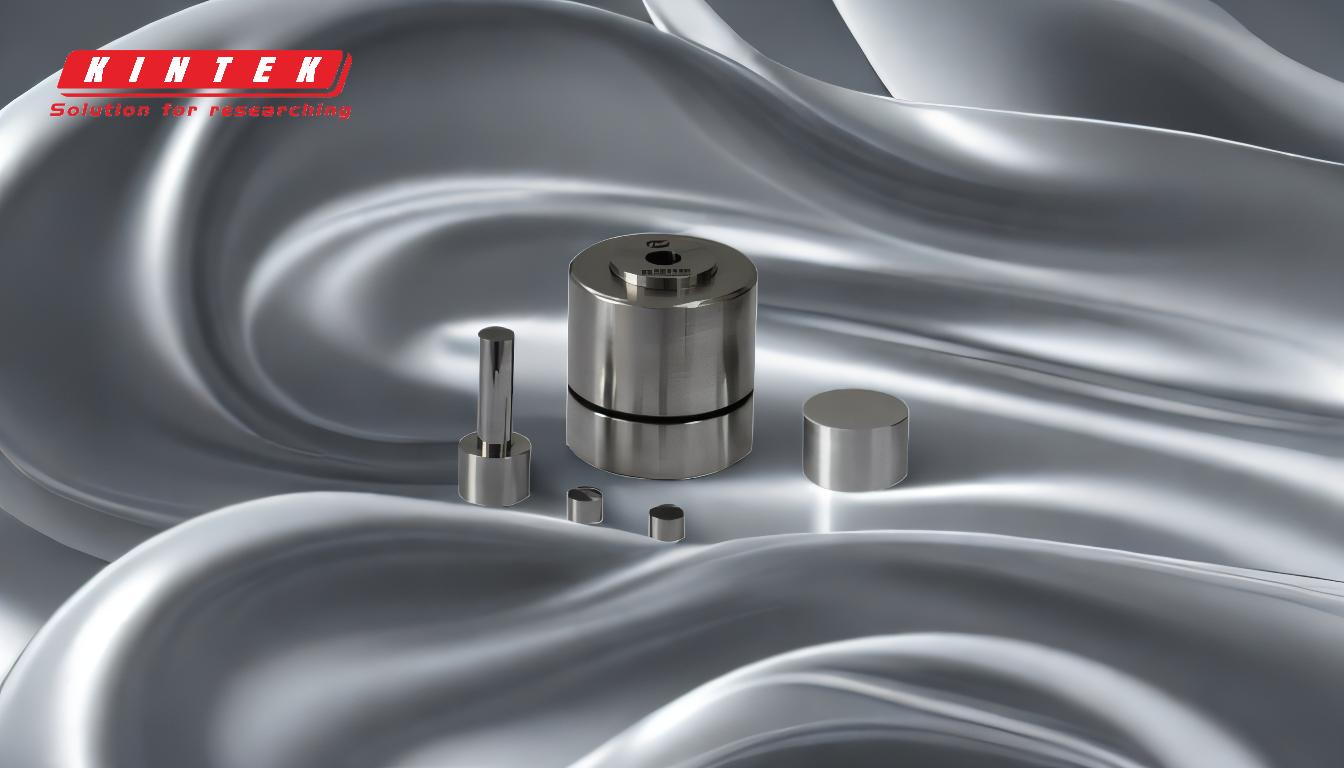
-
Properties of Metal Powders:
- Particle Size and Shape: The size and shape of the metal powder particles significantly influence the flow characteristics, compaction, and sintering processes. Fine particles generally result in better compaction and sintering, leading to stronger and more uniform parts.
- Density and Flow Characteristics: The density of the powder affects the final part's density and mechanical properties. Good flow characteristics are essential for uniform filling of the mold during compaction.
-
Process Steps in Powder Metallurgy:
- Mixing: Metal powders are often mixed with other materials, such as lubricants or alloying elements, to achieve desired properties in the final product.
- Compaction: The mixed powder is compacted under high pressure to form a "green" part, which retains the shape of the mold. This step is crucial for achieving the desired density and strength in the final part.
- Sintering: The compacted part is heated to a temperature below the melting point of the metal, allowing the particles to bond together. This step enhances the mechanical properties and density of the part.
-
Advantages of Powder Metallurgy:
- Cost-Effectiveness: Powder metallurgy is a low-cost manufacturing method due to its high material utilization (up to 97%) and minimal waste generation.
- High Precision and Complexity: The process allows for the production of complex shapes and tight tolerances, making it ideal for high-precision components.
- Eco-Friendly: With minimal waste and no scrap, powder metallurgy is considered a green manufacturing technology.
- Material Efficiency: The ability to freely assemble material structures and accurately control material properties makes it a preferred method for producing high-performance materials.
-
Applications in Industry:
- Automotive and Aerospace: Powder metallurgy is widely used in the automotive and aerospace industries for producing high-strength, lightweight components with exceptional wear resistance and toughness.
- Hand Tools: Tools produced using powder metallurgy exhibit superior wear resistance, toughness, and hardness retention, making them last significantly longer than those made using other processes.
-
Future Prospects:
- The precision and accuracy of powder metallurgy make it likely that more industries, including hand tool manufacturing, will adopt this method in the near future. Its ability to produce high-value-added materials with minimal environmental impact positions it as a key technology in the advancement of green manufacturing.
In summary, powder metallurgy is a highly efficient and versatile manufacturing process that offers numerous benefits, including cost savings, material efficiency, and the ability to produce complex, high-performance parts. Its eco-friendly nature and applicability across various industries make it a vital technology in modern manufacturing.
Summary Table:
Key Considerations | Details |
---|---|
Properties of Metal Powders | - Particle Size and Shape: Affects flow, compaction, and sintering. |
- Density and Flow Characteristics: Ensures uniform mold filling. | |
Process Steps | - Mixing: Combines powders with additives for desired properties. |
- Compaction: Forms a 'green' part under high pressure. | |
- Sintering: Bonds particles for enhanced mechanical properties. | |
Advantages | - Cost-Effective: High material utilization, minimal waste. |
- High Precision: Produces complex, tight-tolerance parts. | |
- Eco-Friendly: Minimal waste, green manufacturing. | |
Applications | - Automotive & Aerospace: High-strength, lightweight components. |
- Hand Tools: Superior wear resistance and durability. |
Discover how powder metallurgy can revolutionize your manufacturing process—contact us today for expert guidance!