Sintered parts can exhibit various defects due to improper sintering conditions or material behavior during the process. Common defects include oversintering, undersintering, blistering, sweating, warping, and sagging. These defects arise from factors such as incorrect temperature, insufficient or excessive sintering time, gas discharge, or mechanical stresses. Understanding these defects is crucial for optimizing the sintering process and ensuring the final product meets performance and quality standards.
Key Points Explained:
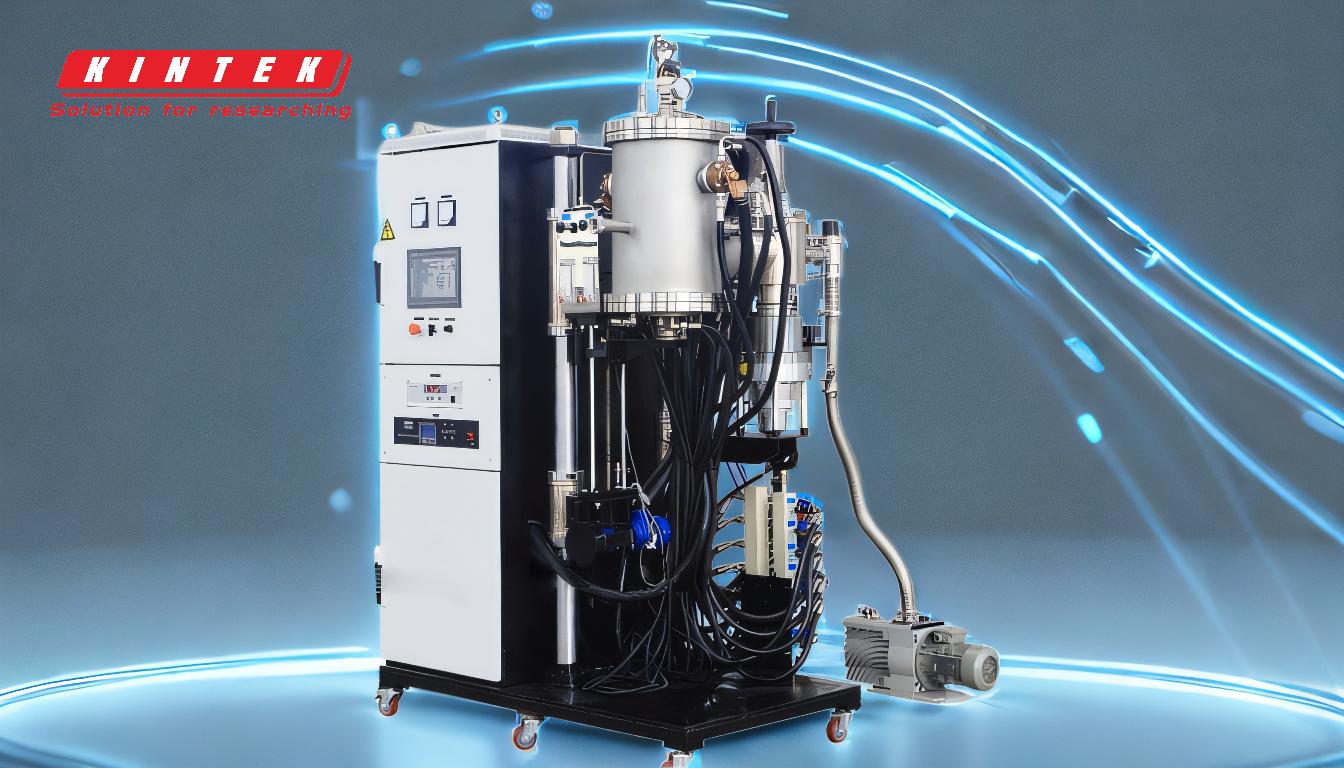
-
Oversintering:
- Cause: Occurs when the sintering temperature is too high or the sintering time is too long.
- Effect: Leads to product deterioration, such as excessive grain growth, reduced mechanical properties, or even melting of the material.
- Prevention: Carefully control temperature and time parameters to avoid exceeding optimal sintering conditions.
-
Undersintering:
- Cause: Results from insufficient sintering temperature or time.
- Effect: Produces parts with inadequate density, poor mechanical strength, and incomplete bonding between particles.
- Prevention: Ensure the sintering process reaches the required temperature and duration for proper densification.
-
Blistering:
- Cause: Surface defects caused by trapped gases discharging during sintering.
- Effect: Creates bubbles or blisters on the surface, compromising the part's integrity and aesthetics.
- Prevention: Use proper degassing techniques before sintering and optimize the heating rate to allow gases to escape gradually.
-
Sweating:
- Cause: Occurs when a liquid phase seeps out during heat treatment, often due to impurities or incorrect sintering conditions.
- Effect: Results in uneven surfaces and potential contamination of the part.
- Prevention: Use high-purity materials and control the sintering environment to minimize liquid phase formation.
-
Warping:
- Cause: Caused by gravity or friction during sintering, leading to uneven shrinkage or deformation.
- Effect: Produces parts with distorted shapes, affecting dimensional accuracy and functionality.
- Prevention: Use proper support structures during sintering and optimize heating and cooling rates to minimize stress.
-
Sagging:
- Cause: Occurs when parts deform under their own weight during sintering, especially in high-temperature processes.
- Effect: Leads to dimensional inaccuracies and structural weaknesses.
- Prevention: Use appropriate sintering supports and optimize the sintering profile to reduce deformation risks.
-
Porosity Issues:
- Cause: Influenced by the initial porosity of the green compact, sintering temperature, and duration.
- Effect: Excessive porosity can weaken the part, while insufficient porosity may hinder specific applications.
- Prevention: Adjust the sintering parameters and, if necessary, apply pressure during sintering to achieve the desired porosity.
By addressing these key points, manufacturers can identify and mitigate common sintering defects, ensuring higher-quality sintered parts and more efficient production processes.
Summary Table:
Defect | Cause | Effect | Prevention |
---|---|---|---|
Oversintering | Excessive temperature or time | Grain growth, reduced strength, melting | Control temperature and time |
Undersintering | Insufficient temperature or time | Low density, poor strength, weak bonding | Ensure proper temperature and duration |
Blistering | Trapped gases discharging | Surface bubbles, compromised integrity | Degas before sintering, optimize heating |
Sweating | Liquid phase seeping out | Uneven surfaces, contamination | Use high-purity materials, control sintering environment |
Warping | Gravity or friction during sintering | Distorted shapes, dimensional inaccuracies | Use supports, optimize heating/cooling |
Sagging | Deformation under weight during sintering | Dimensional inaccuracies, weak structures | Use supports, optimize sintering profile |
Porosity Issues | Initial porosity, temperature, duration | Weak parts or hindered applications | Adjust parameters, apply pressure if needed |
Need help optimizing your sintering process? Contact our experts today for tailored solutions!