Graphene synthesis methods can be broadly categorized into two approaches: bottom-up and top-down. The bottom-up approach involves building graphene from carbon atoms or small molecules, while the top-down approach involves breaking down larger carbon structures like graphite into graphene. Key methods include chemical vapor deposition (CVD), mechanical exfoliation, liquid-phase exfoliation, sublimation of silicon carbide (SiC), and reduction of graphene oxide. Each method has its advantages and limitations, with CVD being the most promising for large-scale, high-quality graphene production. Other methods, such as mechanical exfoliation, are more suited for research purposes, while liquid-phase exfoliation and reduction of graphene oxide are cost-effective for mass production but often result in lower-quality graphene.
Key Points Explained:
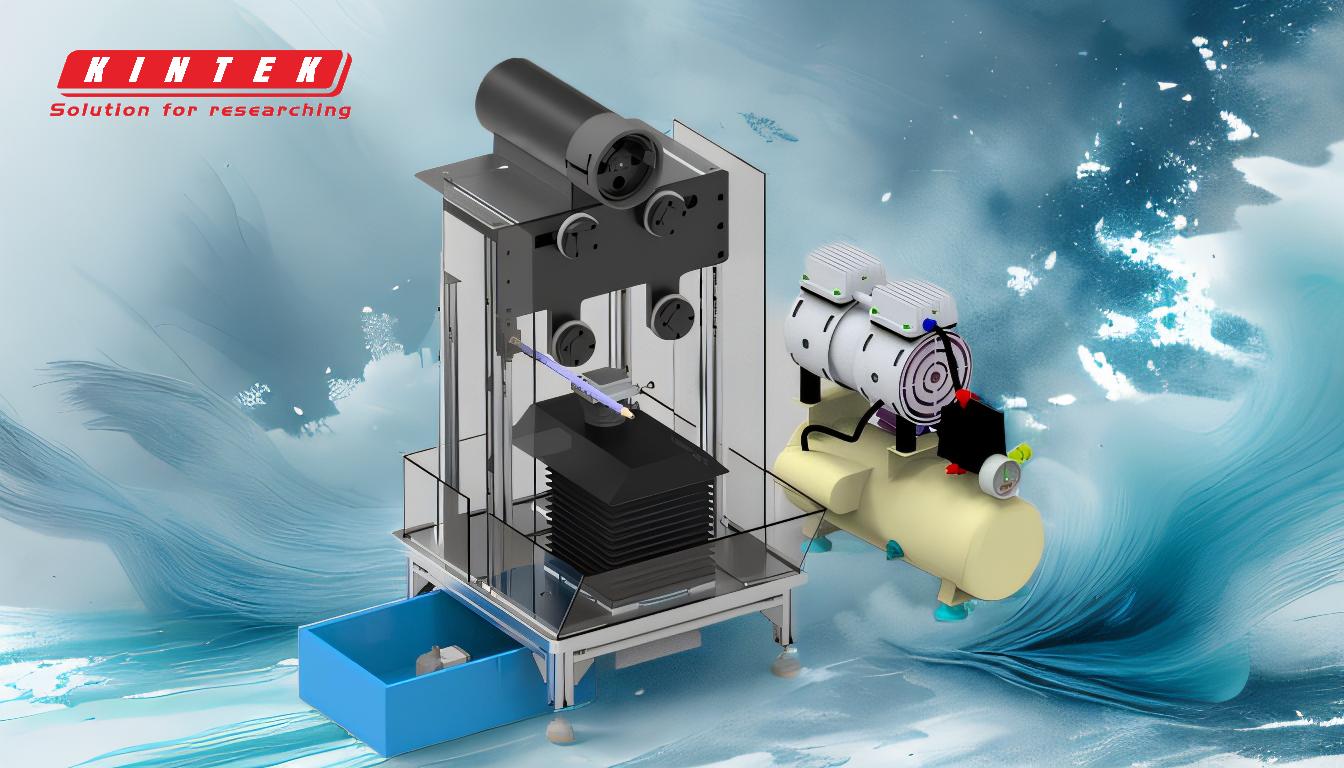
-
Bottom-Up Synthesis Methods
-
Chemical Vapor Deposition (CVD):
- CVD is the most widely used method for producing high-quality, large-area graphene. It involves decomposing carbon-containing gases (e.g., methane) at high temperatures on a substrate (e.g., transition metals like nickel or copper). The carbon atoms then form a graphene layer as they cool.
- Advantages: High-quality graphene, scalability for industrial applications.
- Limitations: Requires precise control of temperature, pressure, and gas flow; expensive equipment.
- Substrate modifications (e.g., annealing under hydrogen) can improve grain growth and produce single-crystal graphene.
-
Epitaxial Growth on Silicon Carbide (SiC):
- This method involves heating SiC to high temperatures, causing silicon atoms to sublimate and leaving behind a graphene layer.
- Advantages: High-quality graphene suitable for electronic applications.
- Limitations: High cost, limited scalability, and challenges in controlling layer thickness.
-
Arc Discharge:
- This method involves creating an arc between two graphite electrodes in an inert gas atmosphere, producing graphene sheets.
- Advantages: Simple and cost-effective.
- Limitations: Produces graphene with defects and impurities, not suitable for high-quality applications.
-
-
Top-Down Synthesis Methods
-
Mechanical Exfoliation (Scotch Tape Method):
- This method involves peeling graphene layers from graphite using adhesive tape.
- Advantages: Produces high-quality graphene suitable for fundamental research.
- Limitations: Low yield, not scalable for industrial applications.
-
Liquid-Phase Exfoliation:
- Graphite is dispersed in a solvent and subjected to sonication or shear forces to separate graphene layers.
- Advantages: Scalable, cost-effective, and suitable for mass production.
- Limitations: Graphene produced often has defects and low electrical conductivity.
-
Chemical Oxidation and Reduction of Graphene Oxide:
- Graphite is oxidized to produce graphene oxide, which is then reduced to graphene using chemical or thermal methods.
- Advantages: Cost-effective and scalable.
- Limitations: Graphene produced has structural defects and lower electrical quality compared to CVD graphene.
-
-
Carbon Sources for Graphene Synthesis
-
Methane Gas:
- The most popular carbon source for CVD due to its ability to decompose cleanly into carbon atoms.
-
Petroleum Asphalt:
- A less expensive alternative to methane but more challenging to work with due to impurities and complex decomposition processes.
-
Methane Gas:
-
Emerging and Hybrid Methods
-
Hydrothermal and Sol-Gel Methods:
- These traditional nanomaterial synthesis methods are being explored for graphene production but are not yet widely adopted.
-
Modified CVD Techniques:
- Innovations like using single-crystal substrates or catalyst films are improving the quality and scalability of CVD graphene.
-
Hydrothermal and Sol-Gel Methods:
-
Applications and Suitability of Each Method
- CVD: Best for electronics, sensors, and large-scale industrial applications due to its high-quality output.
- Mechanical Exfoliation: Ideal for fundamental research and small-scale experiments.
- Liquid-Phase Exfoliation and Graphene Oxide Reduction: Suitable for applications where cost is more critical than quality, such as composites and coatings.
- SiC Sublimation: Primarily used in high-performance electronics and research.
By understanding the strengths and limitations of each synthesis method, purchasers and researchers can select the most appropriate technique based on their specific needs, whether for high-quality graphene in electronics or cost-effective production for industrial applications.
Summary Table:
Method | Approach | Advantages | Limitations |
---|---|---|---|
Chemical Vapor Deposition (CVD) | Bottom-Up | High-quality graphene, scalable for industrial use | Expensive equipment, requires precise control |
Mechanical Exfoliation | Top-Down | High-quality graphene for research | Low yield, not scalable |
Liquid-Phase Exfoliation | Top-Down | Cost-effective, scalable for mass production | Graphene has defects, low electrical conductivity |
Graphene Oxide Reduction | Top-Down | Cost-effective, scalable | Structural defects, lower electrical quality |
SiC Sublimation | Bottom-Up | High-quality graphene for electronics | High cost, limited scalability |
Arc Discharge | Bottom-Up | Simple, cost-effective | Produces defective graphene, not suitable for high-quality applications |
Need help choosing the right graphene synthesis method for your project? Contact our experts today!