Annealing furnaces are essential in metallurgical processes, designed to soften metals, relieve internal stresses, and improve their mechanical, electrical, and physical properties. These furnaces heat materials to their recrystallization temperature, making them more ductile for further machining. There are several types of annealing furnaces, each suited to specific applications and industries. These include roller hearth furnaces, pusher furnaces, box furnaces, pot/pit furnaces, conveyor belt furnaces, and integral-quench furnaces. Among these, vacuum annealing furnaces stand out for their ability to process materials in a controlled environment, minimizing contamination and oxidation, making them ideal for high-precision applications like stainless steel components.
Key Points Explained:
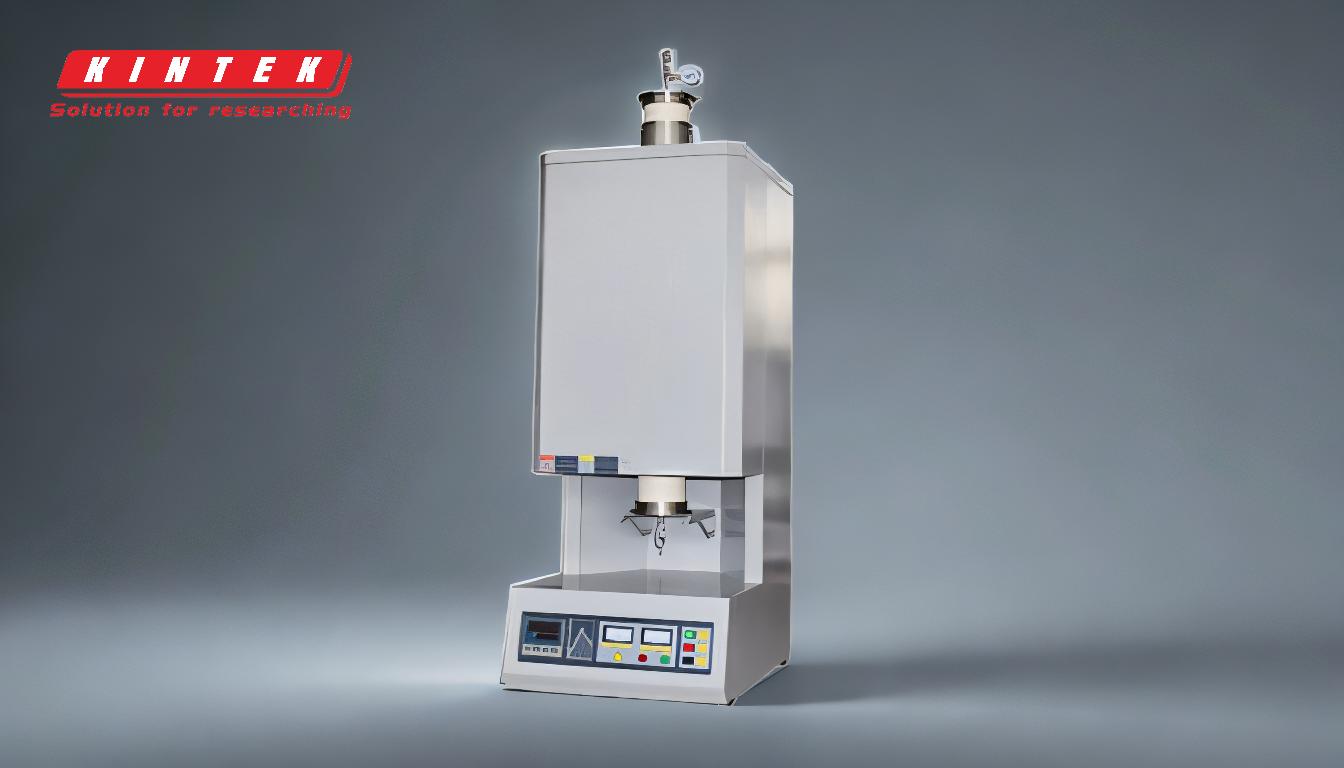
-
Purpose of Annealing Furnaces:
- Annealing furnaces are used to soften metals, allowing for cold working and improving their mechanical, electrical, and physical properties.
- They relieve internal stresses by heating materials to their recrystallization temperature, making them more ductile and easier to machine.
-
Types of Annealing Furnaces:
- Roller Hearth Furnaces: These furnaces use rollers to move materials through the heating chamber, making them ideal for continuous processing of large volumes.
- Pusher Furnaces: Materials are pushed through the furnace in batches, suitable for high-temperature annealing processes.
- Box Furnaces: These are versatile and can handle a variety of materials and batch sizes, often used for smaller-scale operations.
- Pot/Pit Furnaces: Designed for vertical loading, these furnaces are used for annealing large or heavy components.
- Conveyor Belt Furnaces: These are used for continuous annealing of small to medium-sized parts, ensuring uniform heating.
- Integral-Quench Furnaces: These combine heating and quenching processes, making them efficient for heat treatment applications.
-
Vacuum Annealing Furnace:
- A vacuum annealing furnace operates in a controlled environment, minimizing contamination and oxidation. It is particularly useful for high-precision metal components like stainless steel bearings, cutting tools, and plumbing equipment.
- Applications include annealing, brazing, sintering, and heat treatment, especially for materials sensitive to oxidation or requiring high consistency and low pollution.
-
Standard Features of Annealing Furnaces:
- Maximum temperature up to 1800°C.
- High uniformity with temperature control up to +/-5°C.
- Multisegment microprocessor-based programmable temperature controllers.
- High-quality heating elements and individual burner flame safety.
- Provision for gas inlet/outlet and gas/vacuum purging applications.
- Over-temperature protection and programmable PID controllers with data logging software.
-
Applications of Vacuum Annealing Furnaces:
- Heat treatment of steel alloys below 1,200°C.
- Vacuum carburizing (low-pressure carburizing).
- Debinding (removal of binders).
- Processing high-temperature materials in industries like electronics, medical, crystal growth, energy, and artificial gems.
-
Advantages of Vacuum Annealing:
- Protects heated steel and metal parts from the negative effects of air atmosphere.
- Ensures high consistency and low pollution in processes like annealing, brazing, and sintering.
- Ideal for stainless steel deep-drawing parts, preventing oxidation and maintaining material integrity.
By understanding the different types of annealing furnaces and their specific applications, purchasers can make informed decisions tailored to their operational needs, ensuring optimal performance and material quality.
Summary Table:
Type of Annealing Furnace | Key Features | Applications |
---|---|---|
Roller Hearth Furnace | Continuous processing, ideal for large volumes | High-volume metal processing |
Pusher Furnace | Batch processing, suitable for high temperatures | High-temperature annealing |
Box Furnace | Versatile, handles various materials and batch sizes | Small-scale operations |
Pot/Pit Furnace | Vertical loading, for large/heavy components | Annealing heavy parts |
Conveyor Belt Furnace | Continuous annealing, uniform heating | Small to medium-sized parts |
Integral-Quench Furnace | Combines heating and quenching | Heat treatment applications |
Vacuum Annealing Furnace | Controlled environment, minimizes contamination | High-precision metal components |
Ready to find the perfect annealing furnace for your needs? Contact our experts today for personalized advice!