Brazing is a versatile joining process used to bond materials, typically metals, by melting and flowing a filler metal into the joint. The types of brazing joints vary based on the application, design, and materials being joined. Understanding the different types of brazing joints is essential for ensuring strong, durable, and reliable connections. The most common types include butt joints, lap joints, tee joints, and corner joints, each with unique characteristics and applications. The choice of joint depends on factors such as load-bearing requirements, material compatibility, and the desired strength of the connection.
Key Points Explained:
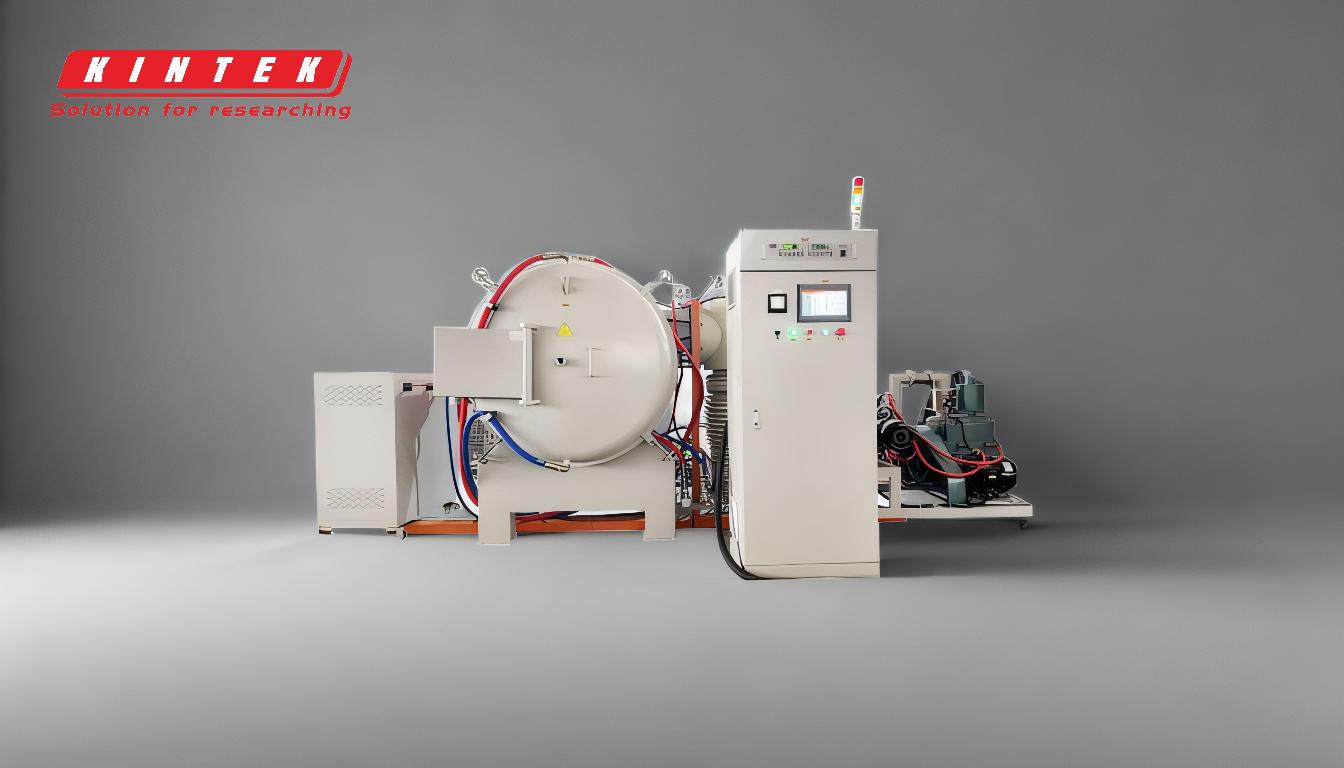
-
Butt Joints
- Definition: A butt joint is formed when two pieces of material are aligned end-to-end or edge-to-edge and joined together. The filler metal flows into the gap between the two surfaces.
- Applications: Commonly used in pipe joining, structural applications, and where a flush surface is required.
- Advantages: Simple design, easy to prepare, and provides a clean, smooth finish.
- Challenges: Requires precise alignment and sufficient surface area for the filler metal to bond effectively.
-
Lap Joints
- Definition: In a lap joint, two pieces of material overlap, and the filler metal is applied along the overlapping area.
- Applications: Widely used in sheet metal work, automotive components, and aerospace applications.
- Advantages: Provides a larger bonding area, which enhances joint strength and distributes stress more evenly.
- Challenges: Requires careful preparation to ensure proper overlap and avoid excessive material buildup.
-
Tee Joints
- Definition: A tee joint is formed when one piece of material is joined perpendicularly to the surface of another, creating a "T" shape.
- Applications: Commonly used in structural frameworks, machinery, and fabrication of metal components.
- Advantages: Offers good load-bearing capacity and is suitable for applications requiring rigidity.
- Challenges: Proper alignment and filler metal distribution are critical to avoid weak spots.
-
Corner Joints
- Definition: A corner joint is created when two pieces of material meet at a right angle, forming a corner.
- Applications: Used in the construction of frames, boxes, and enclosures.
- Advantages: Provides a neat and aesthetically pleasing finish, ideal for visible joints.
- Challenges: Requires precise alignment and careful application of filler metal to ensure a strong bond.
-
Other Joint Types
- Edge Joints: Formed when the edges of two materials are joined, often used in thin sheet metal applications.
- Scarf Joints: Similar to butt joints but with angled surfaces to increase the bonding area and strength.
- Flange Joints: Used in piping and tubing, where flared or flanged ends are joined together.
-
Factors Influencing Joint Selection
- Material Compatibility: The type of materials being joined affects the choice of joint and filler metal.
- Load Requirements: High-stress applications may require joints with larger bonding areas, such as lap joints.
- Design Constraints: The geometry and accessibility of the joint influence the selection process.
- Aesthetic Considerations: Visible joints, such as corner joints, may prioritize appearance over strength.
-
Best Practices for Brazing Joints
- Surface Preparation: Clean and deoxidize the surfaces to ensure proper adhesion of the filler metal.
- Joint Design: Optimize the joint design to maximize strength and minimize stress concentrations.
- Filler Metal Selection: Choose a filler metal with the appropriate melting point, flow characteristics, and compatibility with the base materials.
- Heat Control: Apply heat evenly to avoid overheating or underheating, which can compromise the joint's integrity.
By understanding the different types of brazing joints and their applications, you can select the most appropriate joint for your specific needs, ensuring a strong, durable, and reliable connection.
Summary Table:
Joint Type | Definition | Applications | Advantages | Challenges |
---|---|---|---|---|
Butt Joint | Two pieces aligned end-to-end, filler metal flows into the gap. | Pipe joining, structural applications. | Simple design, clean finish. | Requires precise alignment. |
Lap Joint | Two pieces overlap, filler metal applied along the overlap. | Sheet metal, automotive, aerospace. | Larger bonding area, even stress distribution. | Careful preparation needed. |
Tee Joint | One piece joined perpendicularly to another, forming a "T" shape. | Structural frameworks, machinery. | Good load-bearing capacity. | Critical alignment required. |
Corner Joint | Two pieces meet at a right angle, forming a corner. | Frames, boxes, enclosures. | Aesthetically pleasing finish. | Precise alignment needed. |
Need help selecting the right brazing joint for your project? Contact our experts today for personalized advice!