Heat transfer in furnaces is a critical process that ensures efficient and effective heating of materials. The three primary modes of heat transfer in furnaces are radiation, convection, and conduction. Radiation involves the transfer of heat through electromagnetic waves, which can occur even in a vacuum. Convection involves the movement of fluids (gases or liquids) to transfer heat, while conduction involves heat transfer through solid materials. Each mode plays a distinct role depending on the furnace design, the type of material being heated, and the specific application. Understanding these modes helps in selecting the right furnace and optimizing its performance for various industrial processes.
Key Points Explained:
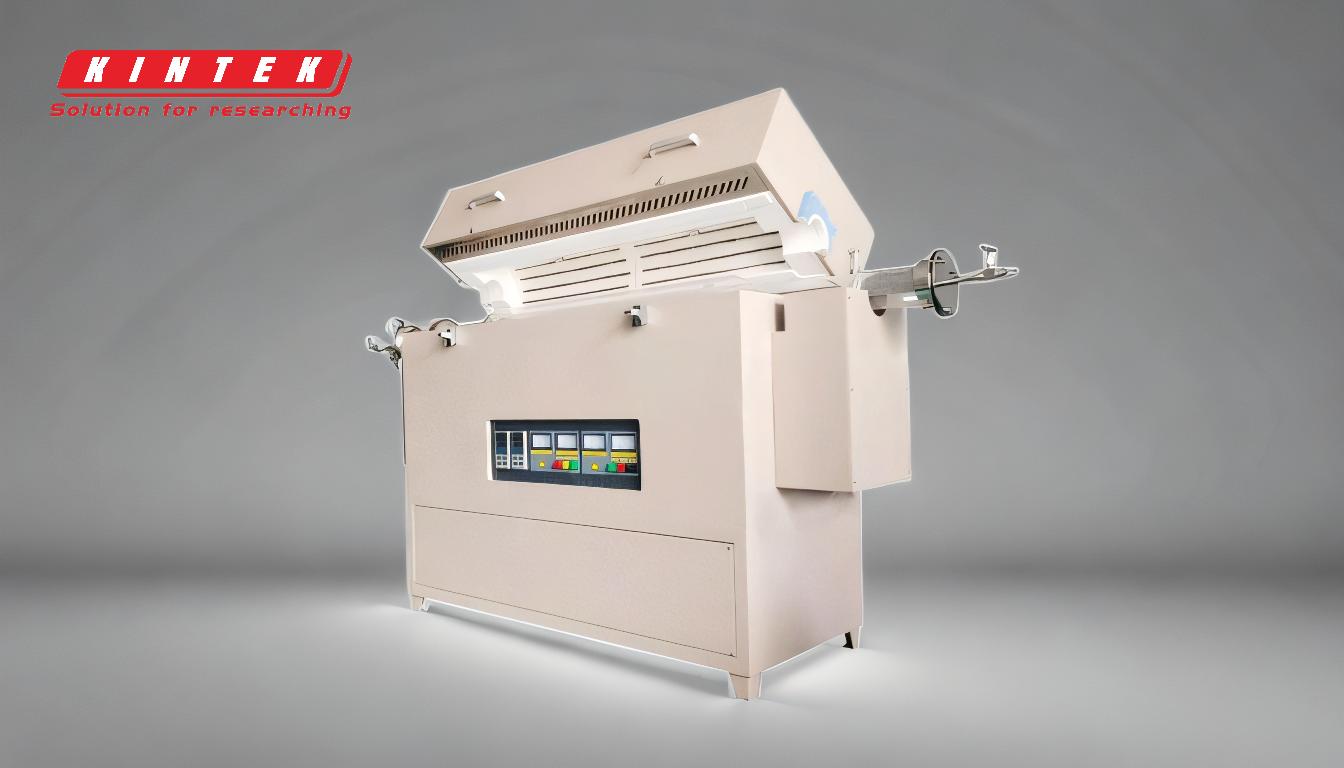
-
Radiation Heat Transfer
- Definition: Radiation is the transfer of heat energy through electromagnetic waves, which can occur through all media, including a vacuum.
- Mechanism: In furnaces, heat radiates from burners or heating elements to the surrounding materials or fluids. This mode is particularly effective in high-temperature environments where direct contact is not possible.
- Applications: Radiation is dominant in processes where the furnace operates at very high temperatures, such as in metal heat treatment or glass manufacturing.
- Advantages: It does not require a medium for heat transfer, making it suitable for vacuum or low-pressure environments.
-
Convection Heat Transfer
- Definition: Convection involves the transfer of heat through the movement of fluids (gases or liquids).
- Mechanism: Heat is initially transferred through conduction at the surface of the heating element, but the bulk heat transfer occurs due to the movement of the fluid. This can be natural (due to density differences) or forced (using fans or pumps).
- Applications: Convection is commonly used in furnaces where uniform heating of materials is required, such as in drying processes or heat treatment of metals.
- Advantages: It ensures even distribution of heat, which is crucial for processes requiring consistent temperature control.
-
Conduction Heat Transfer
- Definition: Conduction is the transfer of heat through solid materials, where energy is transmitted from one particle to another without the particles themselves moving.
- Mechanism: In furnaces, heat is conducted through the walls of the heating chamber or through tubes and other solid components.
- Applications: Conduction is essential in furnaces where direct contact between the heat source and the material is necessary, such as in melting or forging processes.
- Advantages: It is highly efficient for localized heating and is often used in conjunction with other heat transfer modes.
-
Interplay of Heat Transfer Modes in Furnaces
- Combined Use: In most furnaces, all three modes of heat transfer are utilized simultaneously. For example, a furnace may use radiation to heat the outer surface of a material, convection to distribute heat evenly, and conduction to transfer heat through the material itself.
- Optimization: The design of a furnace often involves optimizing the balance between these modes to achieve the desired heating efficiency and uniformity.
- Material Considerations: The choice of heat transfer mode may also depend on the material being heated. For instance, metals with high thermal conductivity may rely more on conduction, while gases or liquids may depend more on convection.
-
Heat Generation Methods in Furnaces
- Fuel-Powered Furnaces: These furnaces generate heat through the combustion of fuels such as natural gas, oil, or coal. They are the most common due to their cost-effectiveness and high heat output.
- Electric Furnaces: These use electrical resistance to generate heat, often employing ceramic fiber or metallic wire thermal elements. They are used in specialized processes where precise temperature control is required.
- Advancements: Modern furnaces often incorporate advanced insulation materials, such as low-mass vacuum-formed ceramic insulation, to improve thermodynamic efficiency and reduce heat loss.
By understanding the different types of heat transfer in furnaces, equipment and consumable purchasers can make informed decisions about the type of furnace best suited for their specific needs. This knowledge also aids in optimizing furnace performance, reducing energy consumption, and ensuring the quality of the heated materials.
Summary Table:
Heat Transfer Mode | Definition | Mechanism | Applications | Advantages |
---|---|---|---|---|
Radiation | Transfer of heat through electromagnetic waves | Heat radiates from burners or heating elements | High-temperature processes (e.g., metal heat treatment, glass manufacturing) | No medium required; works in vacuum/low-pressure environments |
Convection | Transfer of heat through fluid movement | Heat moves via natural or forced fluid flow | Uniform heating (e.g., drying, metal heat treatment) | Ensures even heat distribution |
Conduction | Transfer of heat through solid materials | Heat moves through solid components (e.g., walls, tubes) | Direct contact processes (e.g., melting, forging) | Highly efficient for localized heating |
Need help selecting the right furnace for your industrial needs? Contact our experts today for personalized advice!