Crucible furnaces, while useful for small-scale applications like jewelry making and hobbyist projects, come with several notable disadvantages. These include low energy efficiency, high emissions, size limitations, slower melting times, and high maintenance costs due to frequent crucible replacements. Additionally, they are not ideal for large-scale industrial production due to their limited capacity and slower heating processes. These factors make crucible furnaces less suitable for industries requiring high-volume production or rapid melting cycles.
Key Points Explained:
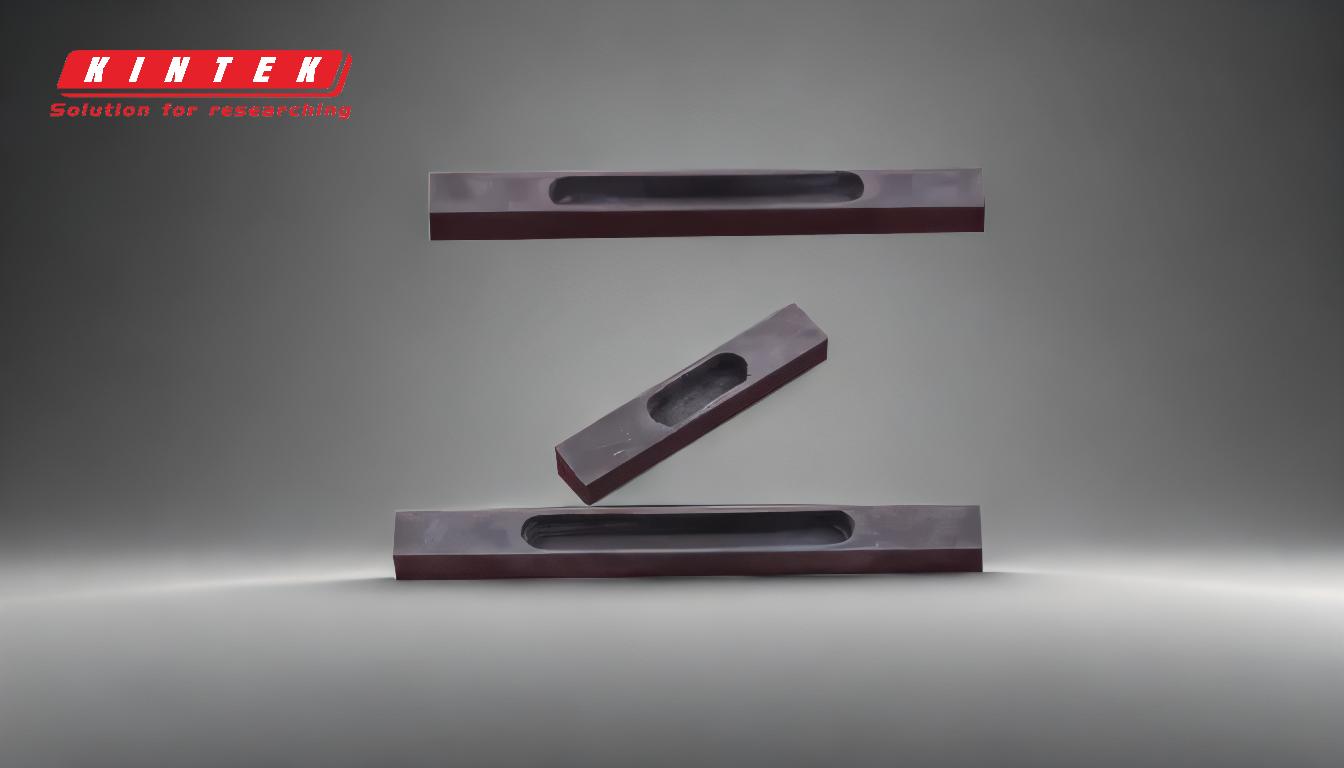
-
Low Energy Efficiency
- Crucible furnaces are notoriously inefficient, with energy efficiency as low as 12%. This means a significant portion of the energy input is lost as waste heat, making them less cost-effective for prolonged or large-scale use.
- The inefficiency also contributes to higher operational costs, as more energy is required to achieve the desired temperatures compared to other furnace types.
-
High Emissions
- Crucible furnaces tend to produce higher emissions, which can be a concern in environmentally regulated industries.
- The emissions may include harmful gases or particulates, requiring additional filtration or ventilation systems, further increasing operational costs.
-
Size Limitations
- These furnaces are typically small in size, with capacities ranging from small cups to moderate kiln-like structures. This limits their use to small-scale applications.
- For industries requiring large-scale production, such as secondary aluminum production, crucible furnaces are impractical due to their limited capacity (typically no more than 8-10 tons).
-
Slower Melting Times
- Crucible furnaces often have longer warm-up and melting times compared to other furnace types, such as induction or open-flame furnaces.
- This makes them less suitable for projects requiring rapid heating or high-throughput production.
-
High Maintenance Costs
- The crucibles themselves are subject to wear and tear from high temperatures and chemical reactions with molten metals. This necessitates frequent replacements, adding to maintenance costs.
- Labor costs can also be higher, as positioning materials and maintaining the furnace require careful handling.
-
Limited Industrial Use
- Due to their small capacity and slower processing times, crucible furnaces are not ideal for large-scale industrial applications.
- They are better suited for remelting fine aluminum chips or small batches of metal, rather than continuous or high-volume production.
-
Expensive Operation
- Running a crucible furnace at high temperatures can be costly, particularly for extended periods. The energy consumption and maintenance requirements contribute to higher operational expenses.
- In comparison to other furnace types, crucible furnaces may offer less heat energy output relative to their input, further increasing costs.
-
Difficulty in Accessing Materials
- Accessing the inside of a crucible furnace can be challenging, requiring careful positioning of materials. This can slow down the workflow and increase the risk of accidents or material spills.
- The enclosed nature of the furnace also makes it less versatile for certain types of projects.
In summary, while crucible furnaces are simple and effective for small-scale applications, their disadvantages—such as low efficiency, high emissions, size limitations, and high maintenance costs—make them less suitable for large-scale or industrial use. These factors should be carefully considered when selecting a furnace for specific applications.
Summary Table:
Disadvantage | Details |
---|---|
Low Energy Efficiency | Energy efficiency as low as 12%, leading to higher operational costs. |
High Emissions | Produces harmful gases and particulates, requiring additional filtration. |
Size Limitations | Limited capacity (8-10 tons), unsuitable for large-scale production. |
Slower Melting Times | Longer warm-up and melting times compared to other furnace types. |
High Maintenance Costs | Frequent crucible replacements and higher labor costs. |
Limited Industrial Use | Not ideal for high-volume or continuous production. |
Expensive Operation | High energy consumption and maintenance expenses. |
Material Access Issues | Challenging to position materials, increasing workflow risks. |
Need a furnace better suited for industrial production? Contact us today to explore alternatives!