Filter presses, including lab filter presses, are widely used for solid-liquid separation in various industries. However, they come with several disadvantages that can affect their efficiency, cost, and operational feasibility. These drawbacks include high initial and maintenance costs, time-consuming operation, limited flexibility in handling different materials, and potential issues with filter cake quality. Understanding these disadvantages is crucial for making informed decisions when selecting filtration equipment.
Key Points Explained:
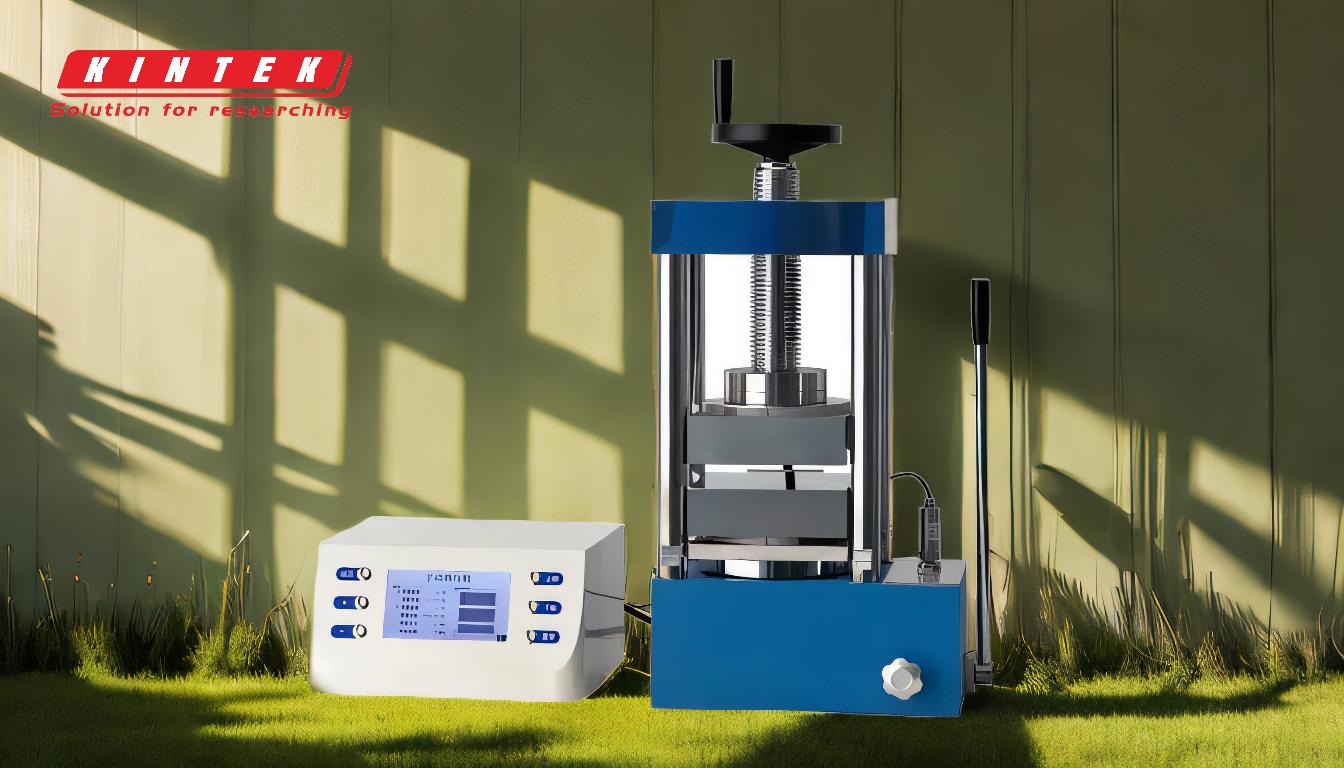
-
High Initial and Maintenance Costs:
- Initial Investment: Filter presses, especially high-quality models, require a significant upfront investment. This includes the cost of the press itself, auxiliary equipment, and installation.
- Maintenance Expenses: Regular maintenance is necessary to ensure optimal performance. This includes replacing filter cloths, cleaning the equipment, and repairing any wear and tear. Over time, these costs can add up, making the overall expense of owning and operating a filter press quite high.
-
Time-Consuming Operation:
- Cycle Time: The filtration process in a filter press can be slow, particularly when dealing with large volumes of slurry or materials with fine particles. The time required to fill, filter, and discharge the filter cake can be a bottleneck in production processes.
- Manual Labor: Some filter presses require manual intervention for tasks such as opening and closing the press, removing the filter cake, and cleaning the filter plates. This can increase labor costs and slow down the overall process.
-
Limited Flexibility:
- Material Compatibility: Filter presses may not be suitable for all types of materials. For example, they may struggle with highly viscous slurries or materials that form compressible filter cakes. This limits their versatility in handling different types of filtration tasks.
- Adjustability: Once a filter press is set up for a specific type of material, it can be challenging to adjust it for different materials or filtration requirements. This lack of flexibility can be a significant drawback in industries where the nature of the slurry varies frequently.
-
Filter Cake Quality Issues:
- Moisture Content: The filter cake produced by a filter press may still contain a significant amount of moisture, which can be problematic if a dry cake is required. Additional drying steps may be necessary, adding to the overall cost and time.
- Cake Discharge: In some cases, the filter cake may not discharge cleanly from the filter plates, leading to blockages and reduced efficiency. This can be particularly problematic with sticky or compressible materials.
-
Space and Energy Requirements:
- Footprint: Filter presses can be large and require a significant amount of space, which can be a limitation in facilities with limited floor area.
- Energy Consumption: The operation of a filter press, especially high-pressure models, can be energy-intensive. This can lead to higher operational costs and a larger environmental footprint.
-
Environmental and Safety Concerns:
- Waste Disposal: The disposal of filter cakes and used filter cloths can pose environmental challenges, particularly if the filtered materials are hazardous or toxic.
- Safety Risks: The high pressures involved in some filter press operations can pose safety risks to operators. Proper training and safety measures are essential to mitigate these risks.
In conclusion, while filter presses, including lab filter presses, offer effective solid-liquid separation, they come with several disadvantages that need to be carefully considered. High costs, time-consuming operations, limited flexibility, filter cake quality issues, space and energy requirements, and environmental and safety concerns are all factors that can impact the overall efficiency and feasibility of using a filter press. Understanding these drawbacks is essential for making informed decisions and ensuring that the chosen filtration method meets the specific needs of the application.
Summary Table:
Disadvantages | Key Details |
---|---|
High Initial and Maintenance Costs | Significant upfront investment and ongoing maintenance expenses. |
Time-Consuming Operation | Slow cycle times and manual labor requirements. |
Limited Flexibility | Challenges with material compatibility and adjustability. |
Filter Cake Quality Issues | High moisture content and discharge problems. |
Space and Energy Requirements | Large footprint and high energy consumption. |
Environmental and Safety Concerns | Waste disposal challenges and safety risks for operators. |
Need help selecting the right filtration equipment? Contact us today for expert advice!