Chemical vapor deposition (CVD) is a widely used technique for depositing thin films and coatings, but it comes with several disadvantages. These include high operating temperatures that can limit substrate compatibility, the need for toxic and volatile chemical precursors, and the generation of hazardous by-products. Additionally, CVD processes are energy-intensive, costly, and require precise control over multiple parameters. The method is also limited in terms of substrate size and the types of materials that can be synthesized, particularly for multi-component systems. Despite its advantages, such as high purity and uniformity, these drawbacks make CVD less suitable for certain applications and more challenging to implement compared to other deposition techniques.
Key Points Explained:
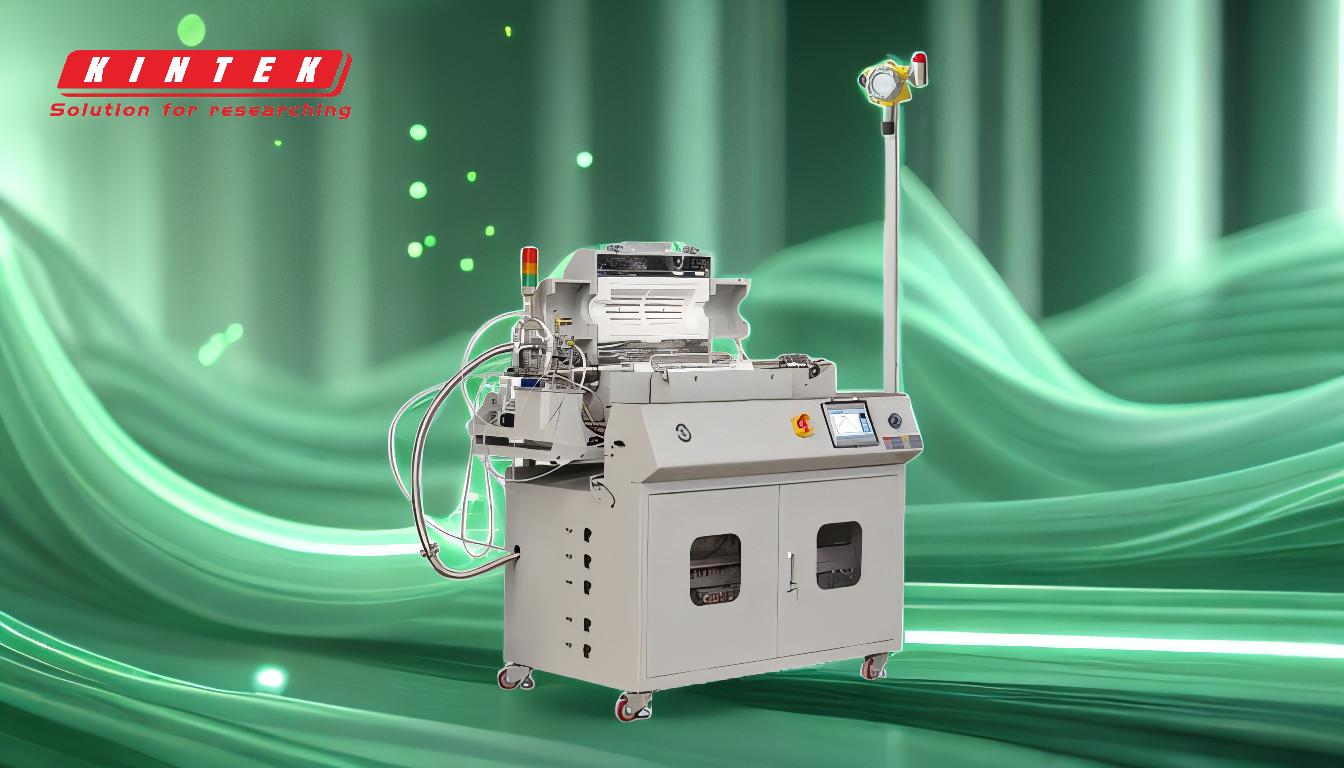
-
High Operating Temperatures:
- CVD typically requires temperatures exceeding 600°C, which can cause thermal instability in many substrates. This limits the types of materials that can be used, as some may degrade or deform at such high temperatures.
- The high energy consumption associated with these temperatures also increases operational costs.
-
Toxic and Volatile Chemical Precursors:
- CVD relies on chemical precursors with high vapor pressure, such as halides and metal-carbonyl compounds, which are often toxic, pyrophoric, or hazardous. This poses significant health and safety risks during handling and processing.
- The scarcity of nontoxic and nonpyrophoric precursors further complicates the process.
-
Hazardous By-Products:
- The CVD process generates by-products that are often toxic and corrosive, such as hydrogen chloride or other volatile compounds. Neutralizing these by-products requires additional equipment and processes, increasing both complexity and cost.
-
High Cost and Energy Consumption:
- CVD equipment is expensive, and the process is energy-intensive due to the high temperatures and precise control required. This makes CVD less economically viable for some applications compared to alternative methods like physical vapor deposition (PVD).
-
Limited Substrate Size and Compatibility:
- The size of substrates that can be processed is limited by the dimensions of the CVD chamber. This restricts the scalability of the process for larger applications.
- Additionally, the high temperatures and chemical reactivity of precursors can limit the types of substrates that are compatible with CVD.
-
Complexity and Precision Requirements:
- CVD requires precise control over multiple parameters, including gas flow rates, substrate temperature, and processing time. This makes the process more complex and less forgiving compared to other deposition techniques.
-
Limitations in Material Synthesis:
- Synthesizing multi-component materials is challenging due to variations in vapor pressure, nucleation, and growth rates during the gas-to-particle conversion. This often results in heterogeneous compositions and inconsistent material properties.
-
Thickness and Structural Limitations:
- CVD is primarily suited for depositing thin films ranging from a few nanometers to a few micrometers. It is not well-suited for creating thicker films or three-dimensional structures, which limits its applicability in certain fields.
-
Environmental and Safety Concerns:
- The use of hazardous gases and chemicals in CVD processes raises environmental and safety concerns. Proper handling, storage, and disposal of these materials are necessary, adding to the overall complexity and cost.
While CVD offers advantages such as high purity and uniformity, these disadvantages highlight the challenges associated with the technique. For applications requiring lower temperatures, simpler processes, or larger-scale production, alternative deposition methods may be more suitable.
Summary Table:
Disadvantage | Description |
---|---|
High Operating Temperatures | Requires >600°C, limiting substrate compatibility and increasing energy costs. |
Toxic Chemical Precursors | Uses hazardous, volatile precursors, posing health and safety risks. |
Hazardous By-Products | Generates toxic and corrosive by-products, requiring additional neutralization. |
High Cost and Energy Consumption | Expensive equipment and energy-intensive processes reduce economic viability. |
Limited Substrate Size | Restricted by chamber dimensions, limiting scalability for larger applications. |
Complexity and Precision | Requires precise control over multiple parameters, increasing process complexity. |
Material Synthesis Limitations | Challenges in synthesizing multi-component materials with consistent properties. |
Thickness and Structural Limits | Suitable only for thin films, not thicker or 3D structures. |
Environmental and Safety Concerns | Handling and disposal of hazardous materials add complexity and cost. |
Looking for a better deposition solution? Contact us today to explore alternatives tailored to your needs!