Electro-deposition, while widely used for coating and material fabrication, has several disadvantages that can impact its efficiency, cost, and environmental footprint. Key drawbacks include limited material compatibility, high energy consumption, uneven coating thickness, environmental concerns due to toxic byproducts, and challenges in achieving uniform deposition on complex geometries. Additionally, the process often requires precise control of parameters, which can increase operational complexity and costs. These limitations make electro-deposition less suitable for certain applications, particularly those requiring high precision, environmental sustainability, or cost-effectiveness.
Key Points Explained:
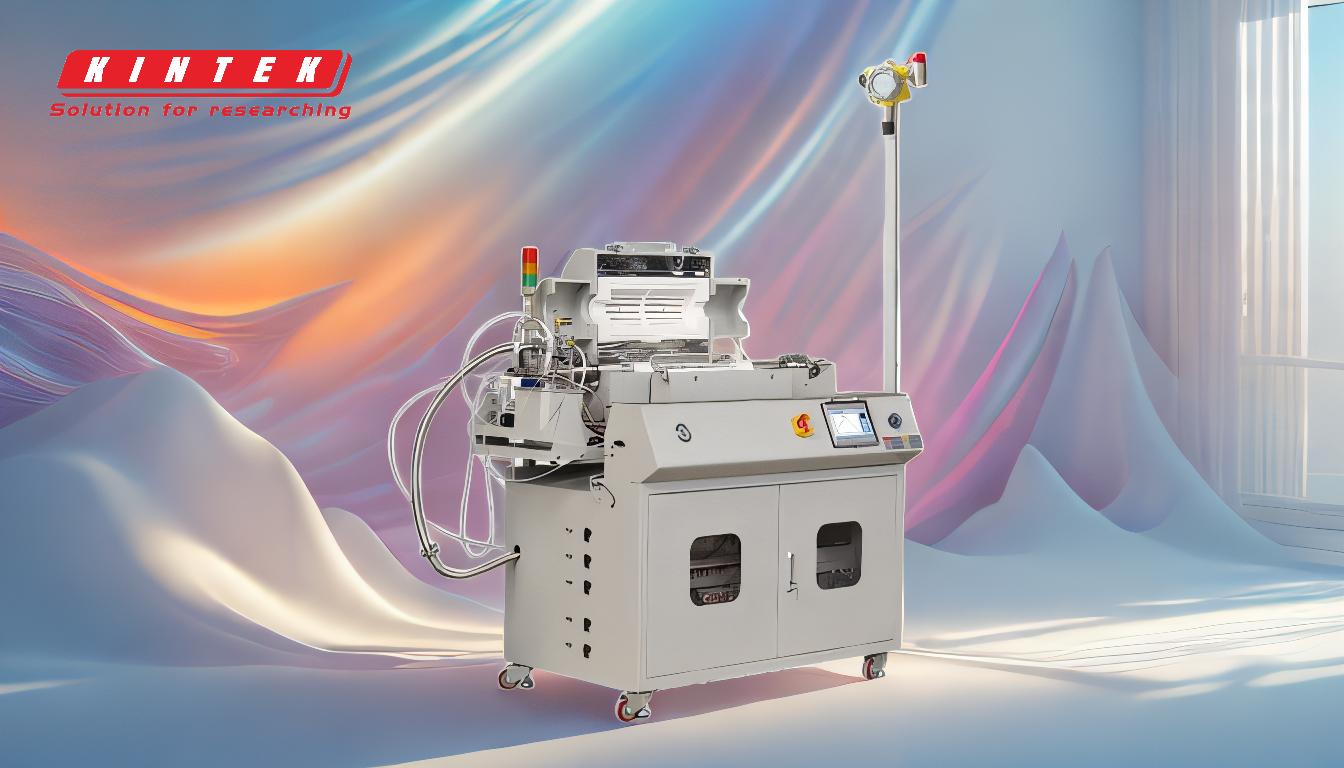
-
Limited Material Compatibility
- Electro-deposition is primarily suited for conductive materials, as it relies on the flow of electric current to deposit ions onto a substrate.
- Non-conductive materials require additional pre-treatment (e.g., metallization), which increases costs and complexity.
- Certain materials may also react unfavorably with the electrolyte, leading to poor adhesion or contamination.
-
High Energy Consumption
- The process requires a continuous supply of electrical energy to maintain the electrochemical reactions.
- Energy costs can be significant, especially for large-scale or prolonged operations.
- Inefficiencies in the process, such as resistance in the electrolyte or substrate, can further exacerbate energy consumption.
-
Uneven Coating Thickness
- Electro-deposition often results in non-uniform coating thickness, particularly on edges, corners, or complex geometries.
- This phenomenon, known as the "edge effect," occurs because electric fields concentrate at sharp features, leading to faster deposition in these areas.
- Achieving uniform thickness may require additional steps, such as masking or post-processing, which increase time and cost.
-
Environmental Concerns
- The process generates toxic byproducts, including heavy metals and hazardous chemicals, which must be carefully managed to prevent environmental contamination.
- Wastewater treatment and disposal of spent electrolytes add to operational costs and regulatory compliance burdens.
- The use of environmentally harmful substances, such as cyanide-based electrolytes, further exacerbates these issues.
-
Challenges with Complex Geometries
- Electro-deposition struggles to provide uniform coatings on substrates with intricate shapes or deep recesses.
- Shielding effects can prevent adequate deposition in hard-to-reach areas, leading to incomplete coverage.
- This limitation restricts its use in applications requiring precise and consistent coating across all surfaces.
-
Operational Complexity and Cost
- The process demands precise control of parameters such as voltage, current density, temperature, and electrolyte composition.
- Maintaining these conditions requires advanced equipment and skilled personnel, increasing operational costs.
- Regular maintenance of equipment and replenishment of electrolytes further add to expenses.
-
Potential for Defects
- Common defects include pinholes, blistering, and poor adhesion, which can compromise the quality and durability of the coating.
- These defects often arise from impurities in the electrolyte, improper substrate preparation, or fluctuations in process parameters.
- Addressing defects may necessitate rework or scrapping of parts, leading to material wastage and higher costs.
-
Limited Deposition Rate
- Electro-deposition is generally slower compared to other coating methods, such as physical vapor deposition (PVD) or thermal spraying.
- The slow deposition rate can be a bottleneck in high-volume production environments.
- Increasing the deposition rate often requires higher current densities, which can lead to quality issues like roughness or porosity.
-
Dependence on Substrate Conductivity
- The substrate must be electrically conductive for the process to work effectively.
- Non-conductive substrates require pre-treatment steps, such as applying a conductive layer, which adds time and cost.
- Even with pre-treatment, achieving good adhesion and uniformity can be challenging.
-
Health and Safety Risks
- The use of hazardous chemicals and high-voltage equipment poses risks to workers.
- Proper safety measures, such as protective gear and ventilation systems, are essential but increase operational complexity and costs.
- Accidental exposure to toxic substances or electrical hazards can lead to serious health and safety incidents.
By understanding these disadvantages, equipment and consumable purchasers can make informed decisions about whether electro-deposition is suitable for their specific applications. Alternative coating methods may be more appropriate in cases where cost, environmental impact, or precision are critical factors.
Summary Table:
Disadvantage | Key Details |
---|---|
Limited Material Compatibility | Only works with conductive materials; non-conductive substrates need pre-treatment. |
High Energy Consumption | Requires continuous electrical energy, increasing operational costs. |
Uneven Coating Thickness | Non-uniform deposition, especially on edges and complex geometries. |
Environmental Concerns | Generates toxic byproducts, requiring costly waste management. |
Complex Geometries Challenges | Struggles with uniform coating on intricate shapes or deep recesses. |
Operational Complexity | Requires precise control of parameters, increasing costs and complexity. |
Potential for Defects | Risks include pinholes, blistering, and poor adhesion. |
Limited Deposition Rate | Slower compared to other coating methods, impacting high-volume production. |
Dependence on Substrate Conductivity | Non-conductive substrates need pre-treatment, adding time and cost. |
Health and Safety Risks | Involves hazardous chemicals and high-voltage equipment, requiring safety measures. |
Need a better coating solution for your application? Contact our experts today to explore alternatives!