Graphene coatings, despite their impressive properties and wide range of applications, come with several disadvantages that limit their widespread adoption. These drawbacks include high production costs, challenges in achieving uniform and defect-free coatings, environmental and health concerns, and limitations in scalability and durability. Understanding these disadvantages is crucial for purchasers and manufacturers to make informed decisions about the use of graphene coatings in various industries.
Key Points Explained:
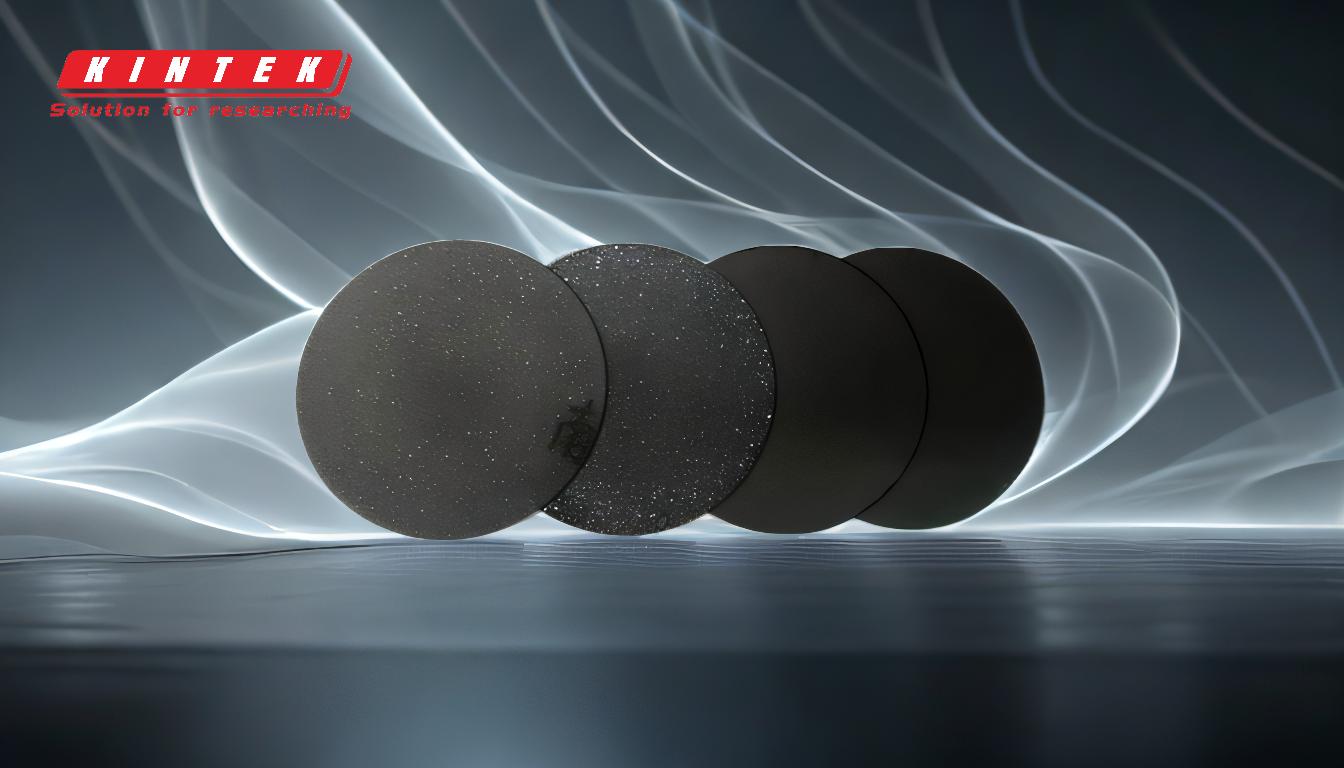
-
High Production Costs:
- Explanation: The production of high-quality graphene is expensive due to the complex and energy-intensive processes involved, such as chemical vapor deposition (CVD). This makes graphene coatings costly compared to traditional coatings.
- Impact: The high cost can be a significant barrier for industries looking to adopt graphene coatings, especially for large-scale applications where cost-effectiveness is critical.
-
Challenges in Uniformity and Defect-Free Coatings:
- Explanation: Achieving a uniform and defect-free graphene coating is challenging. Even minor defects or inconsistencies in the coating can significantly impact its performance, such as reducing its anti-corrosion properties or electrical conductivity.
- Impact: This limitation can lead to inconsistent product quality, making it difficult to guarantee the reliability of graphene-coated materials in critical applications.
-
Environmental and Health Concerns:
- Explanation: The production and handling of graphene can pose environmental and health risks. Graphene particles, especially in nanoparticulate form, can be harmful if inhaled or if they enter water systems.
- Impact: These concerns necessitate stringent safety measures and regulations, which can increase operational costs and complicate the manufacturing process. Additionally, the environmental impact of graphene production may deter its use in eco-conscious industries.
-
Scalability Issues:
- Explanation: Scaling up the production of graphene coatings to meet industrial demands is a significant challenge. Current methods are often limited to small-scale production, making it difficult to produce graphene coatings in large quantities.
- Impact: This limitation restricts the use of graphene coatings to niche applications or small-scale projects, preventing their widespread adoption in industries that require large volumes of coated materials.
-
Durability and Longevity Concerns:
- Explanation: While graphene coatings offer excellent properties such as high strength and conductivity, their long-term durability is still under investigation. Factors like wear and tear, exposure to harsh environments, and potential degradation over time can affect the performance of graphene coatings.
- Impact: Durability issues may necessitate frequent maintenance or replacement of graphene-coated materials, increasing the overall cost and reducing the practicality of using graphene coatings in long-term applications.
-
Limited Compatibility with Certain Substrates:
- Explanation: Graphene coatings may not adhere well to all types of substrates, particularly those with complex geometries or rough surfaces. This can limit the range of materials that can be effectively coated with graphene.
- Impact: The limited compatibility restricts the versatility of graphene coatings, making them unsuitable for certain applications where traditional coatings might perform better.
-
Regulatory and Standardization Challenges:
- Explanation: The lack of standardized testing methods and regulatory frameworks for graphene coatings can create uncertainty in the market. Different manufacturers may have varying quality standards, making it difficult to compare products.
- Impact: This lack of standardization can lead to inconsistencies in product performance and quality, making it challenging for purchasers to make informed decisions and for manufacturers to ensure compliance with industry standards.
In summary, while graphene coatings offer numerous advantages, their disadvantages—such as high production costs, challenges in achieving uniform coatings, environmental concerns, scalability issues, durability concerns, limited substrate compatibility, and regulatory challenges—must be carefully considered. These factors can significantly impact the feasibility and practicality of using graphene coatings in various applications.
Summary Table:
Disadvantage | Explanation | Impact |
---|---|---|
High Production Costs | Expensive due to complex processes like CVD. | Barrier for large-scale adoption. |
Uniformity & Defect-Free Challenges | Difficult to achieve consistent, defect-free coatings. | Inconsistent product quality and reliability. |
Environmental & Health Concerns | Graphene particles can harm health and the environment. | Increased safety measures and operational costs. |
Scalability Issues | Difficult to produce in large quantities. | Limited to niche or small-scale applications. |
Durability Concerns | Long-term performance under harsh conditions is uncertain. | Frequent maintenance or replacement may be required. |
Limited Substrate Compatibility | May not adhere well to all materials or surfaces. | Restricts versatility in applications. |
Regulatory Challenges | Lack of standardized testing and regulatory frameworks. | Inconsistent product quality and market uncertainty. |
Need help evaluating graphene coatings for your application? Contact our experts today for tailored solutions!