Low-pressure chemical vapor deposition (LPCVD) is a widely used technique for depositing thin films, but it comes with several disadvantages. These include high costs due to expensive equipment and energy-intensive processes, limitations on substrate size, and the complexity of controlling precise parameters. Additionally, LPCVD is restricted to depositing thin films, making it unsuitable for thicker or three-dimensional structures. Health and safety concerns also arise due to the use of hazardous gases. These drawbacks make LPCVD less ideal for large-scale production and applications requiring thicker coatings or complex geometries.
Key Points Explained:
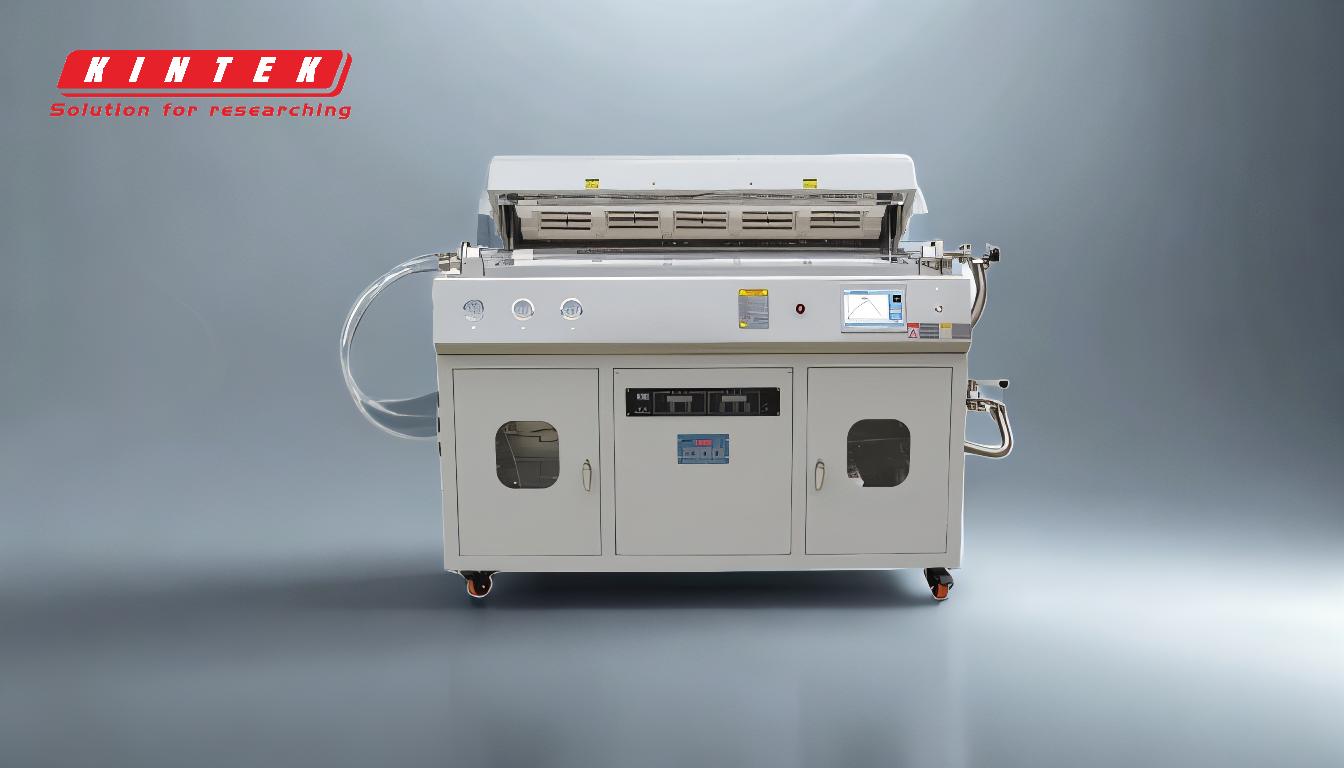
-
High Cost:
- LPCVD requires sophisticated and expensive equipment, including vacuum systems and precise temperature control mechanisms. The energy-intensive nature of the process further increases operational costs, making it less economical for large-scale production.
-
Substrate Size Limitations:
- The process is typically restricted to substrates that fit within the processing chamber. This limitation can be a significant drawback for industries requiring large or irregularly shaped substrates.
-
Complexity and Control:
- LPCVD demands precise control over multiple parameters, such as gas flow rates, substrate temperature, and processing time. This complexity increases the likelihood of errors and requires highly skilled personnel to operate the equipment effectively.
-
Thin Film Limitations:
- LPCVD is primarily used for depositing thin films with thicknesses ranging from a few nanometers to a few micrometers. This makes it unsuitable for applications requiring thicker films or three-dimensional structures, limiting its versatility.
-
Health and Safety Concerns:
- The use of hazardous gases and chemicals in some LPCVD processes poses significant health and safety risks. Proper handling, storage, and disposal of these materials are essential, adding to the overall complexity and cost of the process.
-
Environmental Impact:
- While LPCVD is considered environmentally friendly compared to some other deposition methods, the use of hazardous materials and high energy consumption can still have a negative environmental impact. This necessitates further optimization to make the process more sustainable.
In summary, while LPCVD offers precise and uniform thin film deposition, its high cost, substrate size limitations, complexity, and health and safety concerns make it less suitable for certain industrial applications. For processes requiring lower temperatures and reduced pressure, such as short path vacuum distillation, alternative methods may be more appropriate.
Summary Table:
Disadvantage | Details |
---|---|
High Cost | Expensive equipment and energy-intensive processes increase operational costs. |
Substrate Size Limitations | Restricted to substrates that fit within the processing chamber. |
Complexity and Control | Requires precise control over gas flow, temperature, and processing time. |
Thin Film Limitations | Limited to thin films, unsuitable for thicker or 3D structures. |
Health and Safety Concerns | Use of hazardous gases poses risks, requiring careful handling and disposal. |
Environmental Impact | High energy consumption and hazardous materials can negatively impact the environment. |
Need a better solution for your thin film deposition? Contact our experts today to explore alternatives!