Metal casting, while a widely used manufacturing process, comes with several disadvantages that can impact cost, quality, and efficiency. These drawbacks include high initial costs, limitations in material selection, potential for defects, environmental concerns, and challenges in achieving precise dimensional accuracy. Understanding these disadvantages is crucial for manufacturers and purchasers to make informed decisions about whether metal casting is the best method for their specific application.
Key Points Explained:
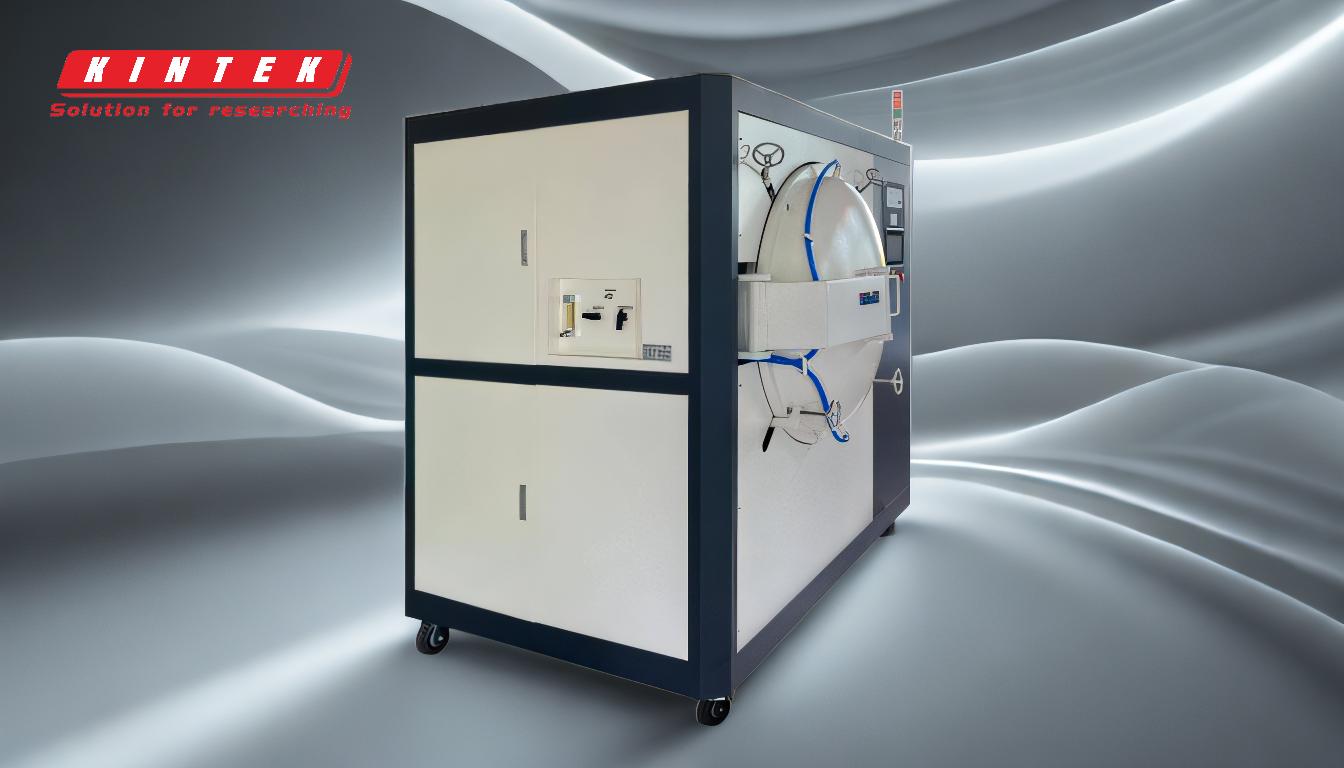
-
High Initial Costs:
- Metal casting requires significant upfront investment in equipment, molds, and tooling. The creation of molds, especially for complex shapes, can be expensive and time-consuming.
- Additionally, the process often necessitates specialized machinery and skilled labor, further driving up costs.
-
Material Limitations:
- Not all metals are suitable for casting. Some materials may have poor flow characteristics or may not solidify properly, leading to defects.
- The choice of material can also be limited by the need to balance properties such as strength, ductility, and thermal conductivity.
-
Potential for Defects:
- Metal casting is prone to various defects such as porosity, shrinkage, and inclusions. These defects can compromise the structural integrity and performance of the final product.
- Post-casting inspections and quality control measures are often required to identify and address these issues, adding to the overall cost and time.
-
Environmental Concerns:
- The metal casting process can generate significant amounts of waste, including scrap metal, used sand, and emissions. Proper disposal and treatment of these wastes are necessary to minimize environmental impact.
- Energy consumption during the melting and casting processes can also be high, contributing to the overall carbon footprint.
-
Challenges in Achieving Precise Dimensional Accuracy:
- Achieving tight tolerances and precise dimensions can be difficult with metal casting, especially for complex geometries. This may necessitate additional machining or finishing processes, increasing production time and cost.
- Variations in cooling rates and shrinkage can lead to dimensional inconsistencies, requiring careful design and process control to mitigate.
-
Long Production Cycles:
- The metal casting process, from mold creation to final product, can be time-consuming. This can be a disadvantage in industries where rapid production and turnaround times are critical.
- The need for cooling and solidification further extends the production cycle, especially for large or thick-walled castings.
-
Health and Safety Risks:
- The metal casting process involves high temperatures and molten metal, posing significant health and safety risks to workers. Proper safety measures and protective equipment are essential to mitigate these risks.
- Exposure to fumes, dust, and noise can also have long-term health implications for workers.
In conclusion, while metal casting offers many advantages, such as the ability to produce complex shapes and large components, it is important to carefully consider the associated disadvantages. These include high costs, material limitations, potential defects, environmental impact, challenges in achieving precise dimensions, long production cycles, and health and safety risks. By understanding these drawbacks, manufacturers and purchasers can make more informed decisions and explore alternative methods if necessary.
Summary Table:
Disadvantage | Description |
---|---|
High Initial Costs | Significant investment in equipment, molds, and skilled labor. |
Material Limitations | Not all metals are suitable for casting due to flow and solidification issues. |
Potential for Defects | Prone to porosity, shrinkage, and inclusions, requiring costly inspections. |
Environmental Concerns | Generates waste, emissions, and high energy consumption. |
Dimensional Accuracy Challenges | Difficult to achieve tight tolerances, often requiring additional machining. |
Long Production Cycles | Time-consuming process, especially for large or complex castings. |
Health and Safety Risks | High temperatures and exposure to fumes, dust, and noise pose risks to workers. |
Want to learn more about metal casting alternatives? Contact our experts today for tailored solutions!