Physical Vapor Deposition (PVD) is a widely used coating technique for creating protective films with anti-corrosion and wear-resistant properties. However, it comes with several disadvantages that can impact its efficiency, cost, and applicability. These include the high capital cost of equipment, slow deposition rates, limitations in coating complex geometries, and the need for skilled operators and specialized cooling systems. Additionally, PVD is a line-of-sight process, making it challenging to coat undercuts and intricate surface features. These factors collectively make PVD a complex and expensive process, particularly for large-scale or intricate applications.
Key Points Explained:
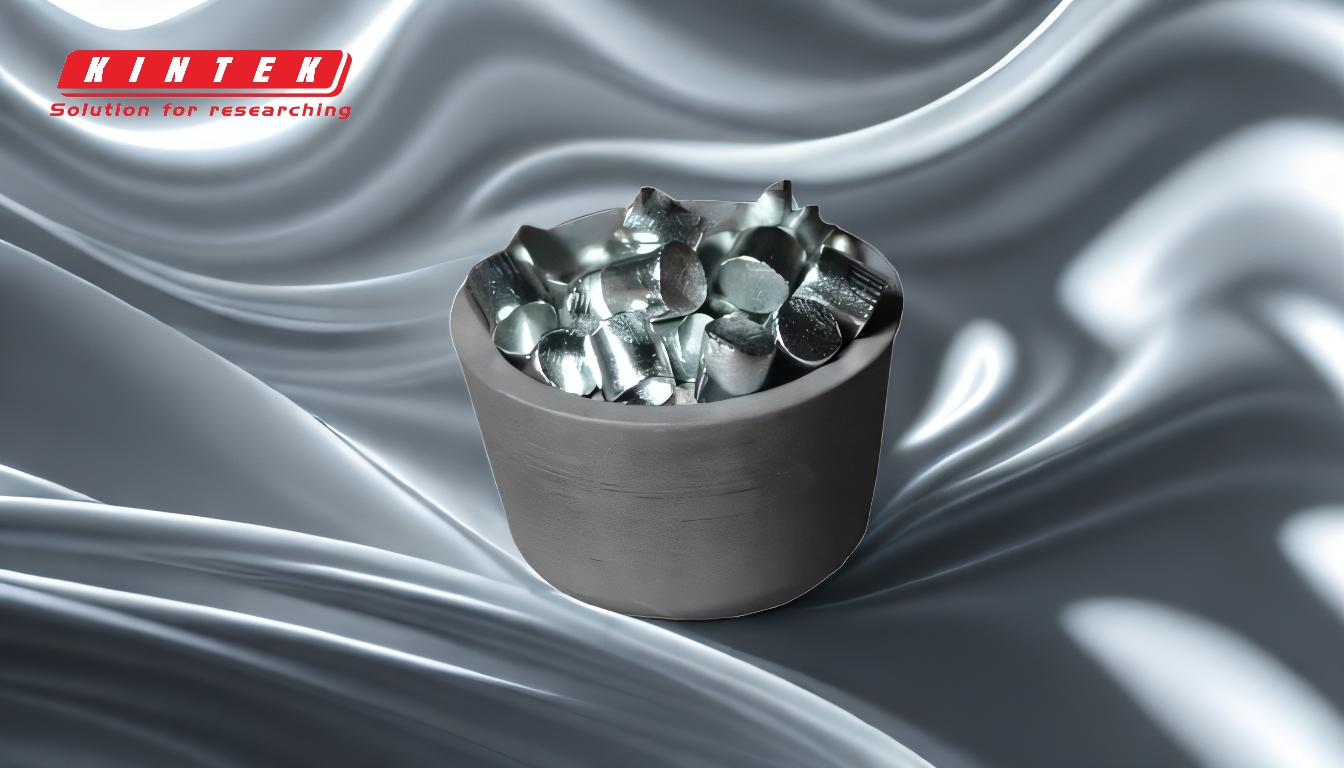
-
High Capital Cost:
- PVD requires complex and expensive equipment, including vacuum chambers and high-temperature systems. The initial investment for setting up a PVD facility is substantial, which can be a barrier for smaller businesses or those with limited budgets.
- The need for specialized cooling systems to manage the heat generated during the process further adds to the cost.
-
Slow Deposition Rates:
- Compared to other coating deposition processes, PVD is relatively slow. This can be a significant drawback in industries where high throughput is essential.
- The slow rate of deposition can also lead to longer production times, which may not be feasible for large-scale manufacturing or time-sensitive projects.
-
Line-of-Sight Limitation:
- PVD is a line-of-sight technique, meaning it can only coat surfaces that are directly exposed to the vapor source. This makes it difficult to coat undercuts, recesses, and other complex geometries.
- As a result, PVD is less suitable for applications where uniform coating of intricate or hidden surfaces is required.
-
High Temperature and Vacuum Requirements:
- PVD processes often require extremely high temperatures and vacuum conditions, which necessitate skilled operators and specialized equipment.
- The high temperatures can also lead to material degradation or changes in substrate properties, which may not be desirable in all applications.
-
Need for Skilled Operators:
- Operating PVD equipment requires a high level of expertise due to the complex nature of the process and the need to maintain precise conditions (e.g., vacuum levels, temperature control).
- The requirement for skilled personnel can increase labor costs and make the process less accessible for companies without experienced staff.
-
Cooling System Requirements:
- PVD processes generate significant heat, necessitating the use of cooling systems to dissipate this heat and maintain process stability.
- The cooling systems add to the overall complexity and cost of the PVD setup, as well as the operational expenses.
-
Material Wastage and Color Destruction:
- PVD can aggressively destroy colors, leading to material wastage and potentially affecting the aesthetic properties of the coated product.
- This can be a significant drawback in industries where color consistency and material efficiency are critical.
-
Limited Applicability to Complex Geometries:
- Due to its line-of-sight nature, PVD is not well-suited for coating substrates with complex geometries or hidden features.
- This limitation can restrict the use of PVD in certain applications, such as those requiring uniform coating of intricate parts or components with internal cavities.
In summary, while PVD offers several advantages in terms of producing high-quality, durable coatings, its disadvantages—such as high costs, slow deposition rates, and limitations in coating complex geometries—can make it less suitable for certain applications. These factors should be carefully considered when deciding whether PVD is the right coating method for a particular project.
Summary Table:
Disadvantage | Description |
---|---|
High Capital Cost | Requires expensive equipment and cooling systems, making initial setup costly. |
Slow Deposition Rates | Slower compared to other coating methods, impacting production efficiency. |
Line-of-Sight Limitation | Cannot coat undercuts or complex geometries effectively. |
High Temperature and Vacuum Needs | Demands skilled operators and specialized equipment for precise conditions. |
Skilled Operators Required | Increases labor costs and limits accessibility for smaller businesses. |
Cooling System Requirements | Adds complexity and operational expenses to the process. |
Material Wastage and Color Loss | Can destroy colors and lead to material inefficiency. |
Limited Applicability to Complex Parts | Unsuitable for uniform coating of intricate or hidden features. |
Considering PVD for your project? Contact our experts to determine if it’s the right solution for your needs!