Pelletization is a critical process in various industries, particularly in pharmaceuticals, materials science, and environmental studies, where materials are compressed into dense, uniform pellets for analysis or use. One of the challenges in pelletization is the expansion of the compressed ring and sample after pressure is released. This expansion can lead to height differences between the sample surface and the ring, affecting X-ray intensity measurements or even causing pellet breakage. Understanding the factors influencing pelletization is essential to mitigate these issues and ensure consistent, high-quality pellets.
Key Points Explained:
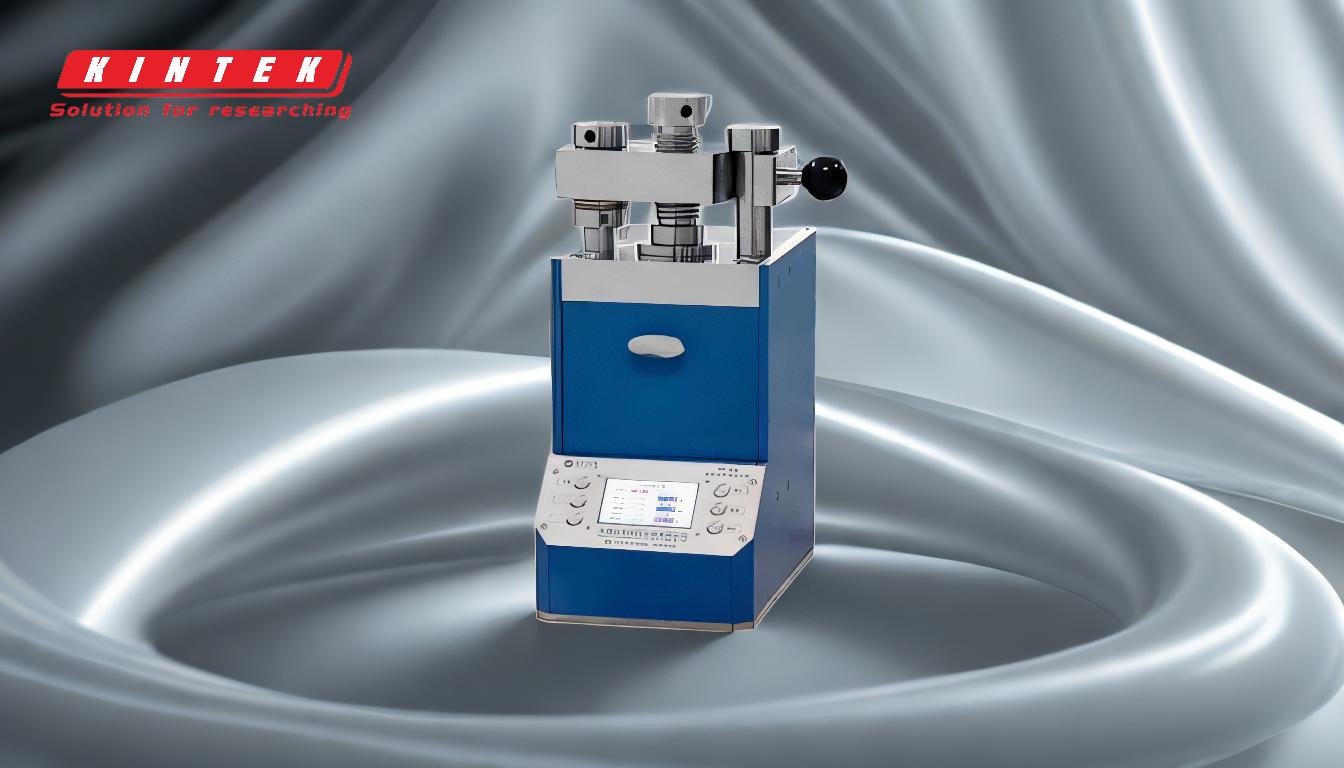
-
Material Properties:
- Particle Size and Distribution: Smaller, uniformly sized particles tend to pack more densely, reducing the likelihood of expansion after compression. Irregular or larger particles may not compress uniformly, leading to post-compression expansion.
- Moisture Content: Excessive moisture can cause swelling or deformation of the pellet after compression. Conversely, too little moisture can make the material brittle and prone to cracking.
- Elasticity and Plasticity: Materials with high elasticity may rebound after compression, while those with high plasticity are more likely to retain their shape. Balancing these properties is crucial for stable pellet formation.
-
Compression Parameters:
- Pressure Applied: Insufficient pressure may result in loosely packed pellets that expand after compression. Excessive pressure can cause over-compaction, leading to internal stresses that may cause the pellet to crack or expand unevenly.
- Compression Time: The duration of applied pressure affects the pellet's density and stability. Longer compression times allow for better particle rearrangement and bonding, reducing post-compression expansion.
- Die Design: The geometry and surface finish of the die can influence how evenly the material is compressed. A poorly designed die may lead to uneven pressure distribution, causing the pellet to expand or break.
-
Binder and Additives:
- Type of Binder: Binders help hold particles together during and after compression. The choice of binder (e.g., organic, inorganic, or polymeric) affects the pellet's mechanical strength and stability.
- Binder Concentration: Too much binder can make the pellet too soft, while too little may result in weak pellets that break or expand. Finding the optimal concentration is key.
- Additives: Lubricants, plasticizers, or other additives can improve the flowability of the material during compression and reduce friction, leading to more uniform pellets.
-
Environmental Conditions:
- Temperature: High temperatures during compression can soften the material, making it easier to compress but also more prone to expansion upon cooling. Low temperatures may make the material too rigid, increasing the risk of cracking.
- Humidity: High humidity can introduce moisture into the material, affecting its compressibility and stability. Controlled humidity conditions are often necessary for consistent pelletization.
-
Post-Compression Handling:
- Curing or Drying: Some pellets require curing or drying to stabilize their structure. Improper curing can lead to expansion or cracking.
- Storage Conditions: Pellets stored in environments with fluctuating temperature or humidity may expand or degrade over time. Proper storage is essential to maintain pellet integrity.
-
Application-Specific Considerations:
- X-ray Analysis: For pellets used in X-ray analysis, even minor height differences between the sample surface and the ring can significantly affect measurement accuracy. Ensuring uniform compression and minimizing expansion is critical.
- Mechanical Stress: Pellets subjected to mechanical stress (e.g., during handling or transport) must have sufficient strength to resist breakage or deformation.
By carefully controlling these factors, manufacturers and researchers can produce high-quality pellets with minimal post-compression expansion, ensuring accurate analysis and reliable performance.
Summary Table:
Factor | Key Considerations |
---|---|
Material Properties | Particle size, moisture content, elasticity, and plasticity affect pellet stability. |
Compression Parameters | Pressure, compression time, and die design impact pellet density and uniformity. |
Binder and Additives | Binder type, concentration, and additives influence pellet strength and flowability. |
Environmental Conditions | Temperature and humidity during compression affect pellet compressibility and stability. |
Post-Compression Handling | Curing, drying, and storage conditions are critical for maintaining pellet integrity. |
Application-Specific Needs | X-ray analysis and mechanical stress require pellets with precise dimensions and strength. |
Need help optimizing your pelletization process? Contact our experts today for tailored solutions!