Calcination is a thermal treatment process applied to ores and other solid materials to bring about thermal decomposition, phase transition, or removal of a volatile fraction. The process is influenced by several factors, including temperature, time, atmosphere, particle size, and the chemical composition of the material. Understanding these factors is crucial for optimizing calcination to achieve desired outcomes such as improved material properties or efficient removal of impurities. Below, we explore the key factors affecting calcination and their implications.
Key Points Explained:
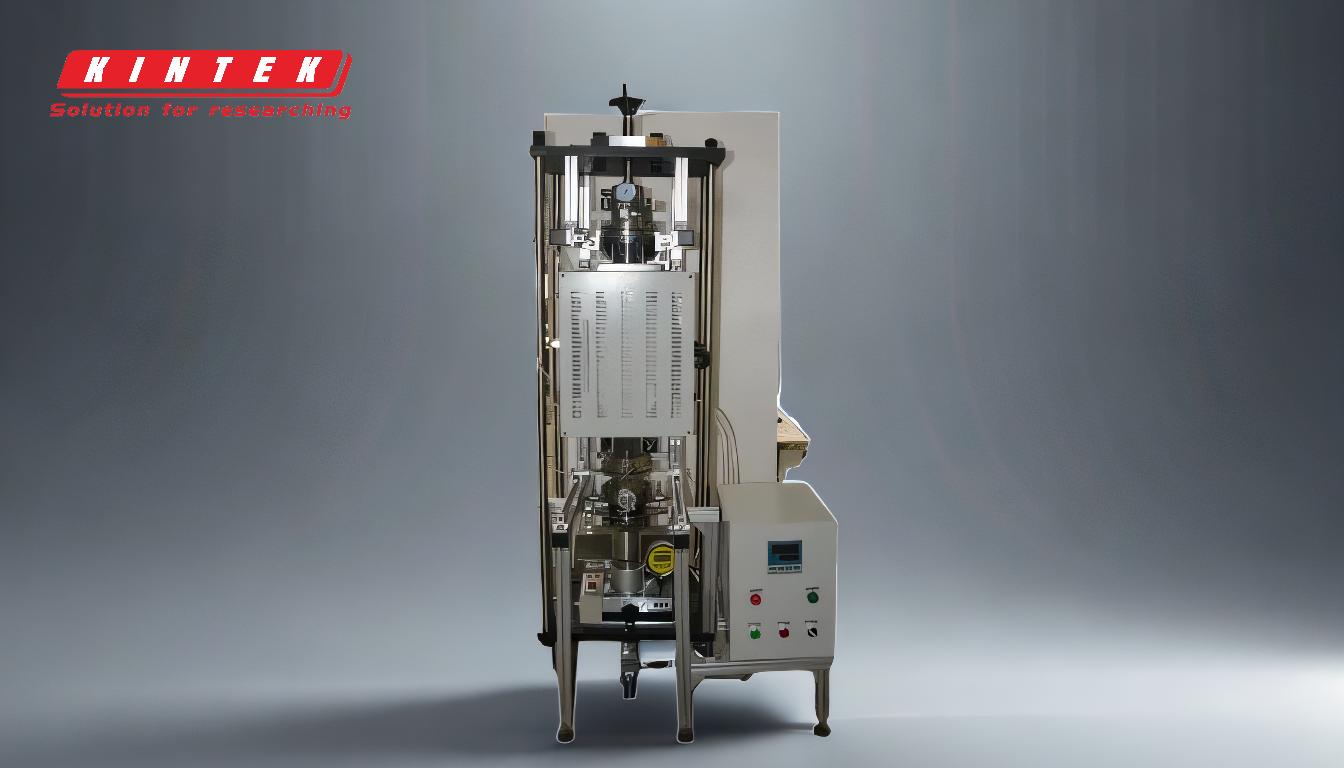
-
Temperature
- Role: Temperature is the most critical factor in calcination, as it directly influences the rate and extent of chemical reactions.
-
Impact:
- Too low a temperature may result in incomplete decomposition or phase transition.
- Too high a temperature can lead to over-calcination, causing undesirable changes in material properties, such as sintering or loss of reactivity.
- Example: For limestone (CaCO₃), calcination typically occurs at 800–900°C to produce lime (CaO) and CO₂. Deviating from this range can affect the quality of the lime.
-
Time
- Role: The duration of calcination determines how thoroughly the material undergoes the desired transformation.
-
Impact:
- Insufficient time may leave unreacted or partially reacted material.
- Excessive time can lead to over-calcination, wasting energy and potentially degrading the material.
- Optimization: Time must be balanced with temperature to ensure efficient and complete calcination.
-
Atmosphere
- Role: The gaseous environment during calcination can significantly affect the process.
-
Impact:
- In an oxidizing atmosphere, oxygen can react with certain materials, altering their composition.
- In a reducing atmosphere, oxygen is limited, which can prevent oxidation or facilitate the removal of volatile components.
- Inert atmospheres (e.g., nitrogen or argon) are used when reactivity with gases must be minimized.
- Example: Calcination of metal carbonates often requires a controlled atmosphere to prevent unwanted oxidation of the resulting metal oxides.
-
Particle Size
- Role: The size of the particles being calcined affects heat transfer and reaction kinetics.
-
Impact:
- Smaller particles have a larger surface area, enabling faster and more uniform heating.
- Larger particles may experience uneven heating, leading to incomplete calcination in the core.
- Optimization: Grinding materials to a consistent and appropriate particle size can enhance calcination efficiency.
-
Chemical Composition
- Role: The inherent properties of the material, such as its chemical composition and structure, influence how it responds to calcination.
-
Impact:
- Materials with higher volatile content (e.g., hydrates or carbonates) require careful control of temperature and time to ensure complete decomposition.
- Impurities in the material can alter the calcination process, either by lowering the required temperature or by forming undesirable byproducts.
- Example: The presence of silica in bauxite can affect the calcination of alumina, requiring adjustments in process parameters.
-
Heating Rate
- Role: The rate at which the material is heated can influence the uniformity and quality of calcination.
-
Impact:
- Rapid heating may cause thermal shock, leading to cracking or uneven decomposition.
- Slow heating ensures uniform temperature distribution but may prolong the process, increasing energy consumption.
- Optimization: A balanced heating rate is essential to achieve efficient and high-quality calcination.
-
Cooling Rate
- Role: The rate at which the material is cooled after calcination can affect its final properties.
-
Impact:
- Rapid cooling may result in thermal stress, causing cracks or phase instability.
- Slow cooling allows for controlled crystallization and stabilization of the material.
- Example: In the production of cement clinker, controlled cooling is critical to achieving the desired crystalline phases.
-
Equipment Design
- Role: The type of calcination equipment (e.g., rotary kilns, fluidized bed reactors, or static furnaces) affects heat transfer, residence time, and overall efficiency.
-
Impact:
- Rotary kilns provide continuous processing and uniform heating but may have higher energy consumption.
- Fluidized bed reactors offer excellent heat transfer and shorter processing times but may not be suitable for all materials.
- Optimization: Selecting the right equipment based on material properties and process requirements is essential for effective calcination.
-
Energy Input
- Role: The amount and type of energy used for calcination influence the process's cost and environmental impact.
-
Impact:
- High energy consumption increases operational costs and carbon footprint.
- Renewable or waste heat sources can reduce energy costs and improve sustainability.
- Optimization: Energy-efficient designs and alternative energy sources can enhance the economic and environmental viability of calcination.
-
Material Feed Rate
- Role: The rate at which material is fed into the calcination system affects residence time and heat distribution.
-
Impact:
- A high feed rate may reduce residence time, leading to incomplete calcination.
- A low feed rate ensures thorough processing but may reduce throughput.
- Optimization: Balancing feed rate with other parameters is crucial for achieving optimal results.
By carefully controlling these factors, calcination can be optimized to achieve the desired material properties, minimize energy consumption, and reduce environmental impact. Each factor interacts with the others, requiring a holistic approach to process design and operation.
Summary Table:
Factor | Role | Impact |
---|---|---|
Temperature | Influences rate and extent of chemical reactions. | Too low: Incomplete decomposition. Too high: Over-calcination and material degradation. |
Time | Determines thoroughness of transformation. | Insufficient: Unreacted material. Excessive: Energy waste and material degradation. |
Atmosphere | Affects chemical reactions during calcination. | Oxidizing, reducing, or inert atmospheres alter material composition and decomposition. |
Particle Size | Influences heat transfer and reaction kinetics. | Smaller particles: Faster, uniform heating. Larger particles: Uneven heating. |
Chemical Composition | Determines material response to calcination. | Volatile content and impurities affect decomposition and byproduct formation. |
Heating Rate | Affects uniformity and quality of calcination. | Rapid heating: Thermal shock. Slow heating: Uniform temperature but higher energy use. |
Cooling Rate | Influences final material properties. | Rapid cooling: Thermal stress. Slow cooling: Controlled crystallization. |
Equipment Design | Impacts heat transfer, residence time, and efficiency. | Rotary kilns, fluidized bed reactors, or static furnaces affect process outcomes. |
Energy Input | Determines cost and environmental impact. | High energy use increases costs. Renewable sources improve sustainability. |
Material Feed Rate | Affects residence time and heat distribution. | High feed rate: Incomplete calcination. Low feed rate: Thorough processing but lower output. |
Optimize your calcination process with expert guidance—contact us today!