The yield of bio-oil from the pyrolysis of coconut shell is influenced by a combination of factors related to the biomass properties, pyrolysis conditions, and reactor design. Key factors include pyrolysis temperature, residence time, heating rate, and the type of reactor used. Additionally, the moisture content, fixed carbon, and volatile matter in the coconut shell play a significant role in determining the yield and quality of bio-oil. Optimizing these parameters can enhance the efficiency of the pyrolysis process, leading to higher bio-oil yields and improved product quality.
Key Points Explained:
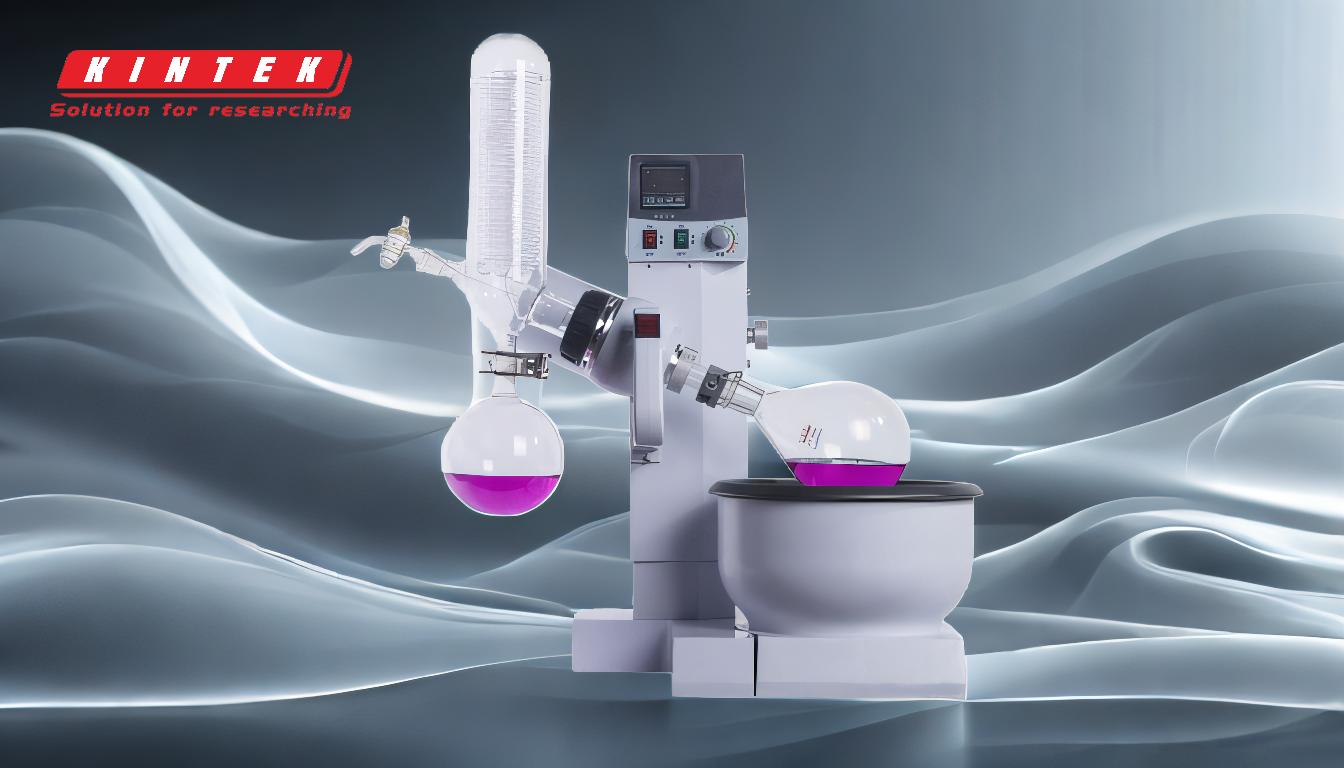
-
Pyrolysis Temperature:
- Temperature is one of the most critical factors affecting bio-oil yield. Higher temperatures generally favor the production of syngas and reduce bio-oil and char yields due to increased thermal cracking and tar decomposition.
- For bio-oil production, moderate temperatures (typically between 400°C to 600°C) are optimal, as they maximize the liquid fraction while minimizing gas and char formation.
-
Residence Time:
- Residence time refers to the duration that the biomass remains in the pyrolysis reactor. Shorter residence times are favorable for bio-oil production, as they prevent secondary reactions that can degrade the oil into gases or char.
- Longer residence times, on the other hand, can lead to increased gas yields due to further cracking of the bio-oil.
-
Heating Rate:
- The heating rate significantly impacts the distribution of pyrolysis products. High heating rates promote the formation of bio-oil by rapidly decomposing the biomass into volatile compounds.
- Slow heating rates tend to favor char formation, as they allow more time for secondary reactions that lead to carbonization.
-
Reactor Type:
- The design of the pyrolysis reactor plays a crucial role in determining product yields. Fast pyrolysis reactors, such as fluidized bed reactors, are preferred for bio-oil production due to their ability to achieve high heating rates and short residence times.
- Other reactor types, like fixed-bed or auger reactors, may yield different product distributions depending on their operating conditions.
-
Biomass Properties:
- Moisture Content: High moisture content in the coconut shell can reduce bio-oil yield, as energy is consumed in evaporating water rather than pyrolyzing the biomass.
- Volatile Matter: Coconut shells with higher volatile matter content tend to produce more bio-oil, as volatiles are the primary precursors for liquid products.
- Fixed Carbon: Higher fixed carbon content can lead to increased char formation, reducing bio-oil yield.
-
Pretreatment Conditions:
- Pretreatment of the coconut shell, such as drying or grinding, can improve bio-oil yield by reducing moisture content and increasing the surface area for heat transfer.
- Removal of impurities, such as soil or ash, also enhances the quality and yield of bio-oil.
-
Feedstock Configuration and Structure:
- The physical and chemical structure of the coconut shell influences the pyrolysis process. For example, the lignin, cellulose, and hemicellulose content in the shell affect the decomposition pathways and product distribution.
- A well-balanced composition of these components can lead to higher bio-oil yields.
-
Operating Conditions:
- Gas Residence Time: Short gas residence times are preferred for bio-oil production to minimize secondary reactions that convert oil into gas or char.
- Pressure: While most pyrolysis processes operate at atmospheric pressure, variations in pressure can influence product yields, with higher pressures sometimes favoring char formation.
By carefully controlling these factors, it is possible to optimize the pyrolysis process for coconut shell to maximize bio-oil yield and quality. Each parameter must be balanced to achieve the desired product distribution and ensure efficient conversion of biomass into valuable bio-oil.
Summary Table:
Factor | Impact on Bio-Oil Yield |
---|---|
Pyrolysis Temperature | Moderate temperatures (400°C–600°C) maximize bio-oil yield; higher temps favor syngas. |
Residence Time | Shorter times prevent secondary reactions, increasing bio-oil yield. |
Heating Rate | High rates promote bio-oil formation; slow rates favor char. |
Reactor Type | Fast pyrolysis reactors (e.g., fluidized bed) optimize bio-oil production. |
Biomass Properties | High volatile matter increases bio-oil; moisture and fixed carbon reduce yield. |
Pretreatment | Drying and grinding improve yield by reducing moisture and increasing surface area. |
Feedstock Structure | Balanced lignin, cellulose, and hemicellulose content enhances bio-oil yield. |
Operating Conditions | Short gas residence times and atmospheric pressure optimize bio-oil production. |
Ready to optimize your pyrolysis process? Contact our experts today to maximize your bio-oil yield!