Heat generation in induction heating depends on several interrelated factors, including the material properties of the workpiece, the design and configuration of the induction coil, the characteristics of the power supply, and the operating conditions. These factors influence the efficiency and effectiveness of the heating process, determining how much heat is generated and how quickly the material reaches the desired temperature. Understanding these factors is crucial for optimizing induction heating systems for specific applications.
Key Points Explained:
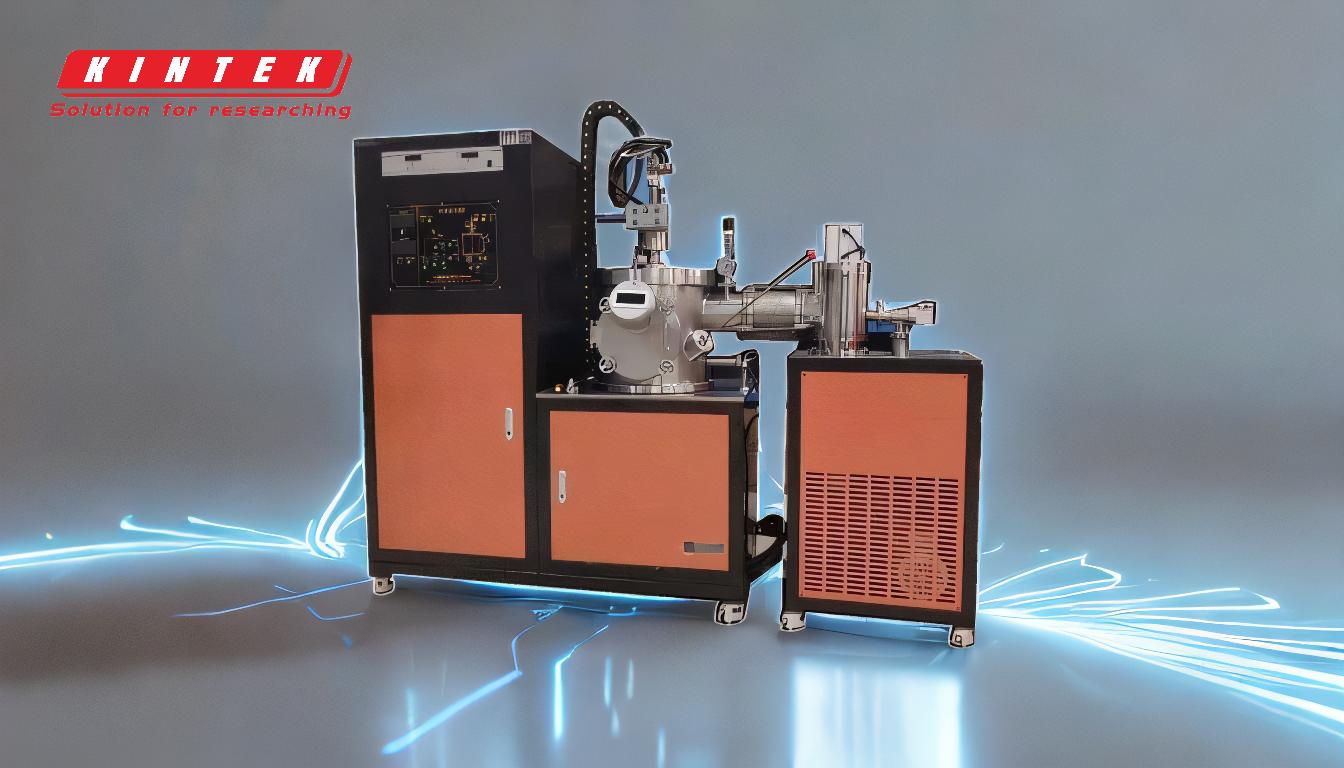
-
Material Properties:
- Type of Material: Induction heating works best with conductive materials, such as metals. Magnetic materials (e.g., iron, steel) heat up due to both eddy currents and hysteresis losses, while non-magnetic conductive materials (e.g., copper, aluminum) rely solely on eddy currents.
- Resistivity: Materials with higher resistivity generate more heat because they resist the flow of eddy currents, converting more electrical energy into thermal energy.
- Size and Thickness: Smaller and thinner materials heat up faster because the induced currents penetrate the material more effectively. Thicker materials may require lower frequencies to achieve deeper heating.
- Specific Heat and Mass: The amount of energy required to raise the temperature of the material depends on its specific heat and mass. Higher specific heat or larger mass requires more energy for the same temperature rise.
-
Induction Coil Design:
- Coil Geometry: The shape and size of the induction coil must match the workpiece to ensure uniform heating. Poorly designed coils can lead to uneven heating or energy losses.
- Number of Turns: The number of turns in the coil affects the magnetic field strength and distribution. More turns can increase the magnetic field but may also increase resistance and energy losses.
- Proximity to Workpiece: The distance between the coil and the workpiece (coupling) affects heating efficiency. Closer coupling improves energy transfer but must be balanced to avoid physical interference.
-
Power Supply Characteristics:
- Frequency: Higher frequencies result in shallower heating depths (skin effect), making them suitable for heating thin materials or surface treatments. Lower frequencies penetrate deeper, ideal for thicker materials.
- Power Capacity: The power supply must provide sufficient energy to achieve the required temperature rise, accounting for the material's specific heat, mass, and heat losses.
- Control and Modulation: Advanced power supplies allow precise control of frequency and power output, enabling optimization for different materials and heating requirements.
-
Operating Conditions:
- Temperature Variation: The degree of temperature change required influences the power needed. Greater temperature variations demand more energy and higher power capacity.
- Heat Losses: Heat can be lost through conduction, convection, and radiation. Insulating the workpiece or using protective atmospheres can minimize these losses.
- Environmental Factors: The presence of impurities, oxidants, or slags can affect heating efficiency and material properties, especially in melting applications.
-
Magnetic and Electrical Phenomena:
- Eddy Currents: These are induced currents within the conductive material that generate heat due to resistance. The magnitude of eddy currents depends on the material's conductivity and the magnetic field strength.
- Hysteresis Losses: In magnetic materials, heat is generated due to the repeated alignment and realignment of magnetic domains under the alternating magnetic field. This effect is negligible in non-magnetic materials.
-
System Efficiency:
- Energy Transfer Efficiency: The efficiency of energy transfer from the power supply to the workpiece depends on the coil design, coupling, and material properties.
- Thermal Efficiency: Minimizing heat losses to the environment and ensuring uniform heating improve overall system efficiency.
By carefully considering these factors, induction heating systems can be optimized for specific applications, ensuring efficient and effective heat generation. This understanding is essential for equipment and consumable purchasers to select the right components and configurations for their needs.
Summary Table:
Factor | Key Considerations |
---|---|
Material Properties | Type, resistivity, size, thickness, specific heat, and mass. |
Induction Coil Design | Coil geometry, number of turns, and proximity to workpiece. |
Power Supply | Frequency, power capacity, and control/modulation capabilities. |
Operating Conditions | Temperature variation, heat losses, and environmental factors. |
Efficiency | Energy transfer efficiency and thermal efficiency. |
Optimize your induction heating system for maximum efficiency—contact our experts today!