Inductor design in induction heating is a critical process that directly impacts the efficiency, effectiveness, and practicality of the heating system. A well-designed inductor ensures optimal heating patterns, maximizes energy efficiency, and accommodates the workpiece's requirements. Key factors to consider include the frequency band selection, material properties of the workpiece, inductor geometry, cooling mechanisms, and power supply compatibility. Each of these factors must be carefully evaluated to achieve the desired heating effect while balancing cost and operational efficiency.
Key Points Explained:
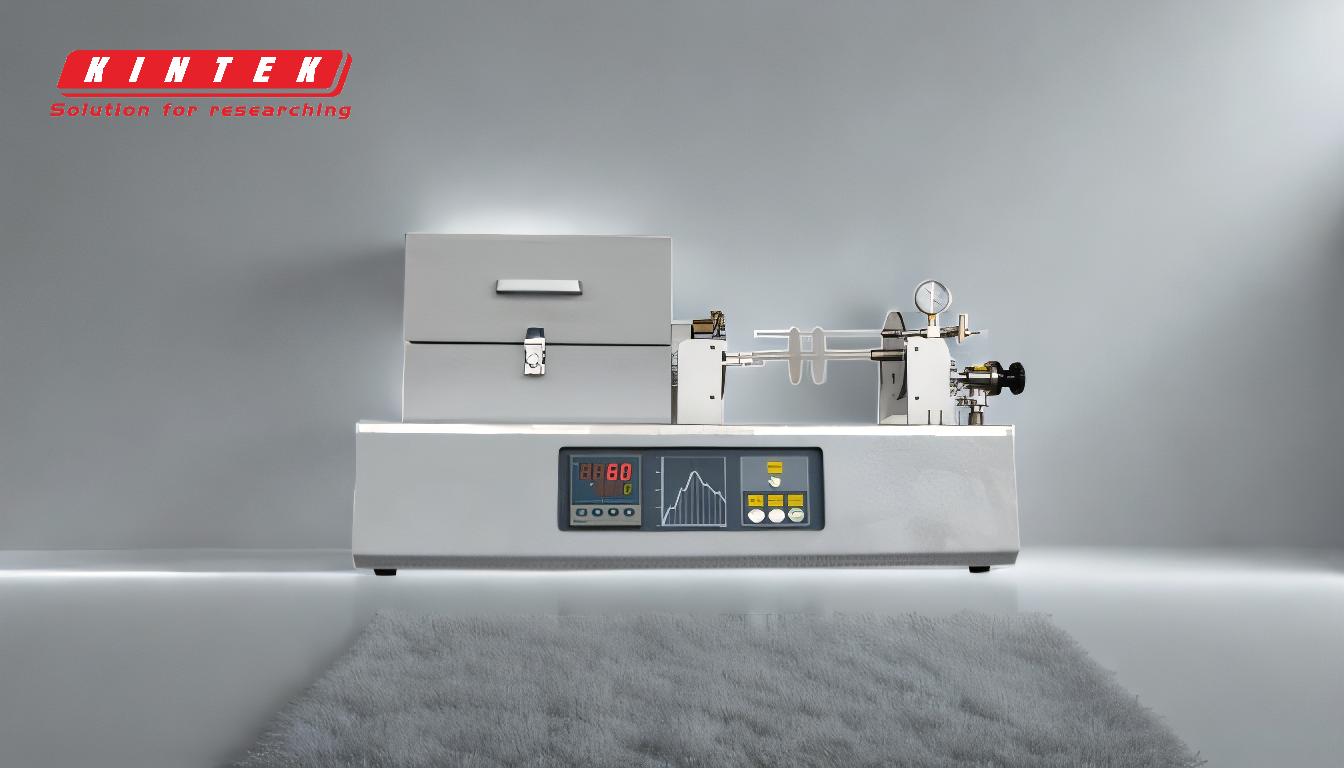
-
Frequency Band Selection
- The frequency of the alternating current used in induction heating significantly influences the heating pattern and depth.
- Lower frequencies (e.g., 50 Hz to 10 kHz) are suitable for deeper penetration in larger workpieces, while higher frequencies (e.g., 10 kHz to 1 MHz) are ideal for surface heating or smaller components.
- The choice of frequency should align with the workpiece material, size, and desired heating effect, while also considering the cost and availability of equipment.
-
Workpiece Material Properties
- The electrical conductivity and magnetic permeability of the workpiece material determine how effectively it can be heated.
- Materials with high electrical conductivity (e.g., copper, aluminum) and magnetic permeability (e.g., iron, steel) are more responsive to induction heating.
- Non-conductive or weakly conductive materials may require special techniques or coatings to enable effective heating.
-
Inductor Geometry and Design
- The shape and size of the inductor coil must match the workpiece geometry to ensure uniform heating.
- Common inductor designs include helical coils, pancake coils, and channel coils, each suited for specific applications.
- The number of turns, spacing between turns, and coil diameter influence the magnetic field distribution and heating efficiency.
-
Cooling Mechanisms
- Induction coils generate heat during operation and require effective cooling to prevent overheating and maintain performance.
- Water cooling is the most common method, with coolant flowing through channels in the inductor or around the coil.
- Proper cooling design ensures longevity and consistent operation of the inductor.
-
Power Supply Compatibility
- The inductor must be compatible with the induction heating power supply in terms of voltage, current, and frequency.
- Impedance matching between the inductor and power supply is essential to maximize energy transfer and minimize losses.
- Custom inductors may be required for specialized applications to achieve optimal performance.
-
Operational Considerations
- The inductor design should facilitate easy loading and unloading of the workpiece to streamline the heating process.
- Durability and maintenance requirements should be considered to minimize downtime and operational costs.
- Safety features, such as insulation and shielding, protect operators and equipment from electrical and thermal hazards.
By addressing these factors, a well-designed inductor can significantly enhance the performance and efficiency of an induction heating system, ensuring reliable and cost-effective operation.
Summary Table:
Factor | Key Considerations |
---|---|
Frequency Band Selection | - Lower frequencies for deep penetration; higher frequencies for surface heating. |
Workpiece Material | - High conductivity and permeability materials (e.g., steel, copper) heat effectively. |
Inductor Geometry | - Match coil shape to workpiece; helical, pancake, or channel designs. |
Cooling Mechanisms | - Water cooling is common; ensures longevity and consistent performance. |
Power Supply Compatibility | - Impedance matching is critical for energy efficiency. |
Operational Considerations | - Ensure easy loading/unloading, durability, and safety features. |
Ready to optimize your induction heating system? Contact our experts today for tailored inductor design solutions!