Muffle furnaces are specialized heating devices designed for high-temperature applications, offering precise temperature control, uniform heating, and protection against contamination. They are widely used in laboratories and industrial settings for processes like annealing, sintering, and heat treatment. Key features include a separate combustion and heating chamber, high-temperature resistance, and advanced control options. Their compact design, durable construction, and ability to operate under controlled atmospheres make them indispensable for producing metal products and conducting material testing.
Key Points Explained:
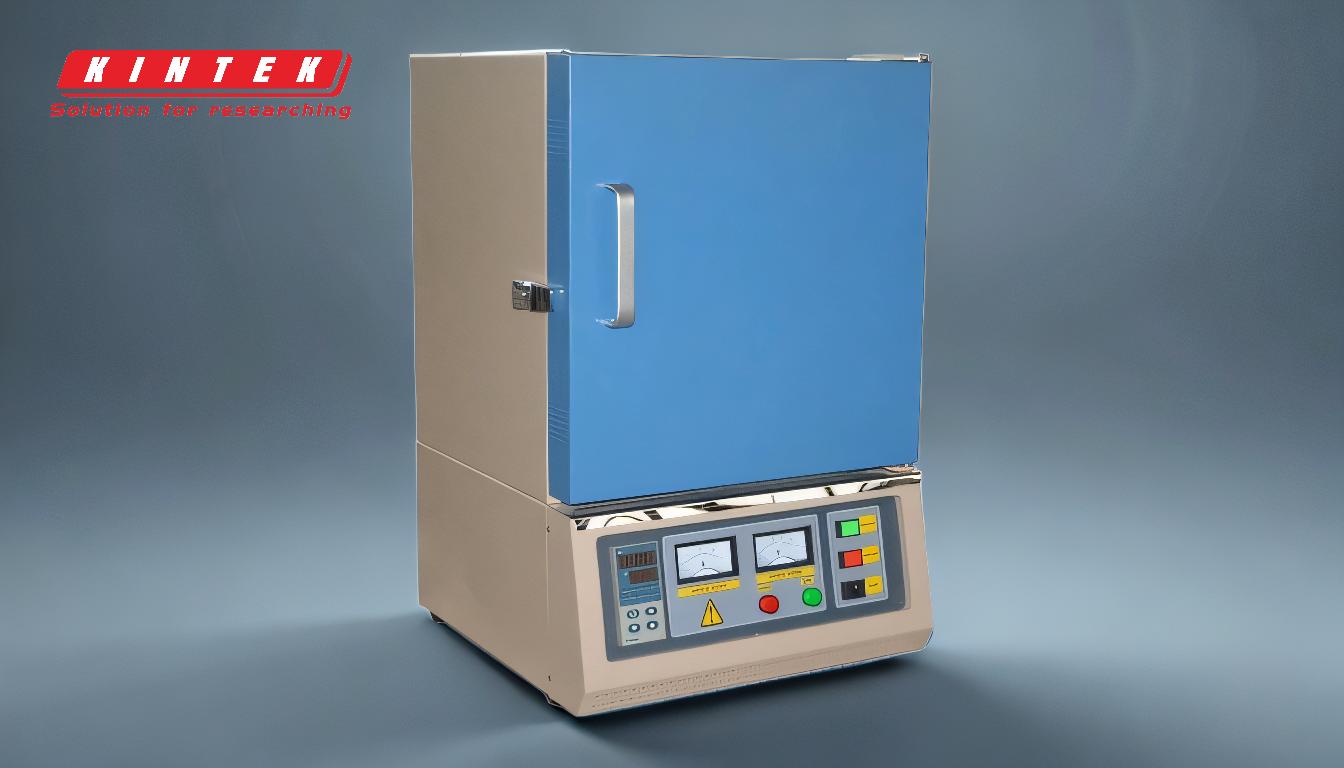
-
Separate Combustion and Heating Chambers
- The muffle furnace features an independent combustion chamber and heating chamber, ensuring that combustion byproducts do not contaminate the materials being heated.
- The heating chamber, often called the "dehydration tank," is airtight, providing a clean environment for processing materials.
- This design is particularly beneficial for applications requiring high purity, such as laboratory experiments or metal production.
-
High-Temperature Capability
- Muffle furnaces can reach extremely high temperatures, typically ranging from 1100°C to 1800°C, depending on the model.
- This makes them suitable for demanding applications like annealing, brazing, sintering, and stress relief.
- The high-temperature alloy removable chambers enhance durability and performance under extreme conditions.
-
Uniform Temperature Distribution
- The furnace ensures excellent temperature uniformity across the chamber, which is critical for consistent results in material processing.
- This is achieved through a combination of radiant and convection heat transfer methods, ensuring homogeneous treatment of workpieces.
- Embedded ceramic muffles further enhance resistance to aggressive gases and vapors, maintaining a stable environment.
-
Heat-Resistant Construction
- Muffle furnaces are built with heat-resistant materials, such as textured stainless steel and ceramic, which provide high thermal conductivity and durability.
- The furnace door is often made of fiber insulation, reducing heat loss and improving energy efficiency.
- These materials also contribute to the furnace's ability to withstand prolonged exposure to high temperatures.
-
Compact and Efficient Design
- Muffle furnaces are designed to be compact, with thicker insulating walls to maintain high temperatures efficiently.
- Smaller chamber sizes are common, making them ideal for laboratory use where space is limited.
- The compact design also minimizes processing time and operational costs.
-
Advanced Control Options
- Modern muffle furnaces come with various control options, including manual, digital, and programmable controls.
- Programmable controls allow users to set specific temperature profiles, ensuring precise and repeatable results.
- Digital interfaces provide real-time monitoring and adjustments, enhancing user convenience and accuracy.
-
Versatile Applications
- Muffle furnaces are used in a wide range of industries, including metallurgy, ceramics, and materials science.
- They are ideal for producing metal products like stainless steel, copper, and low carbon steel.
- Common processes include hardening, drawing, annealing, and sintering, performed in both air and controlled atmospheres.
-
Protective Atmosphere Operation
- Many muffle furnaces operate under a protective atmosphere, preventing oxidation and other chemical reactions that could compromise material integrity.
- This feature is particularly useful for heat-treating sensitive materials or conducting experiments requiring controlled environments.
-
Durability and Practicality
- Constructed with high-quality materials, muffle furnaces are durable and practical for long-term use.
- They are designed to withstand harsh conditions and frequent use, making them a reliable choice for industrial and laboratory settings.
- The robust construction ensures minimal maintenance and extended service life.
-
Cost and Time Efficiency
- Muffle furnaces are engineered to minimize processing time and operational costs, making them a cost-effective solution for high-temperature applications.
- Their efficient insulation and advanced heating mechanisms reduce energy consumption, further enhancing their economic appeal.
In summary, muffle furnaces are sophisticated instruments designed for high-temperature applications, offering precise control, uniform heating, and contamination-free environments. Their compact design, durable construction, and versatile functionality make them essential tools in both industrial and laboratory settings.
Summary Table:
Feature | Description |
---|---|
Separate Chambers | Independent combustion and heating chambers prevent contamination. |
High-Temperature Capability | Reaches 1100°C to 1800°C, ideal for annealing, sintering, and stress relief. |
Uniform Heating | Ensures consistent temperature distribution for reliable results. |
Heat-Resistant Materials | Built with textured stainless steel and ceramic for durability and efficiency. |
Compact Design | Space-saving and energy-efficient, perfect for labs and small spaces. |
Advanced Controls | Programmable and digital controls for precise and repeatable temperature profiles. |
Versatile Applications | Used in metallurgy, ceramics, and materials science for various processes. |
Protective Atmosphere | Operates under controlled environments to prevent oxidation and contamination. |
Durability | High-quality construction ensures long-term use with minimal maintenance. |
Cost Efficiency | Reduces processing time and energy consumption, offering economic benefits. |
Ready to enhance your lab or industrial processes with a muffle furnace? Contact us today to find the perfect solution!