Pyrolysis is a versatile process that can convert a wide range of feedstocks into valuable products like bio-oil, syngas, and biochar. The feedstocks for pyrolysis are broadly categorized into biomass (organic materials) and non-biomass (synthetic or industrial waste materials). Biomass feedstocks include wood, agricultural residues, municipal waste, and energy crops, while non-biomass feedstocks encompass materials like tires, plastics, oil sludge, and rubber. The choice of feedstock depends on factors such as availability, composition, cost, and the desired end products. This answer explores the various feedstocks used in pyrolysis, their sources, and their suitability for the process.
Key Points Explained:
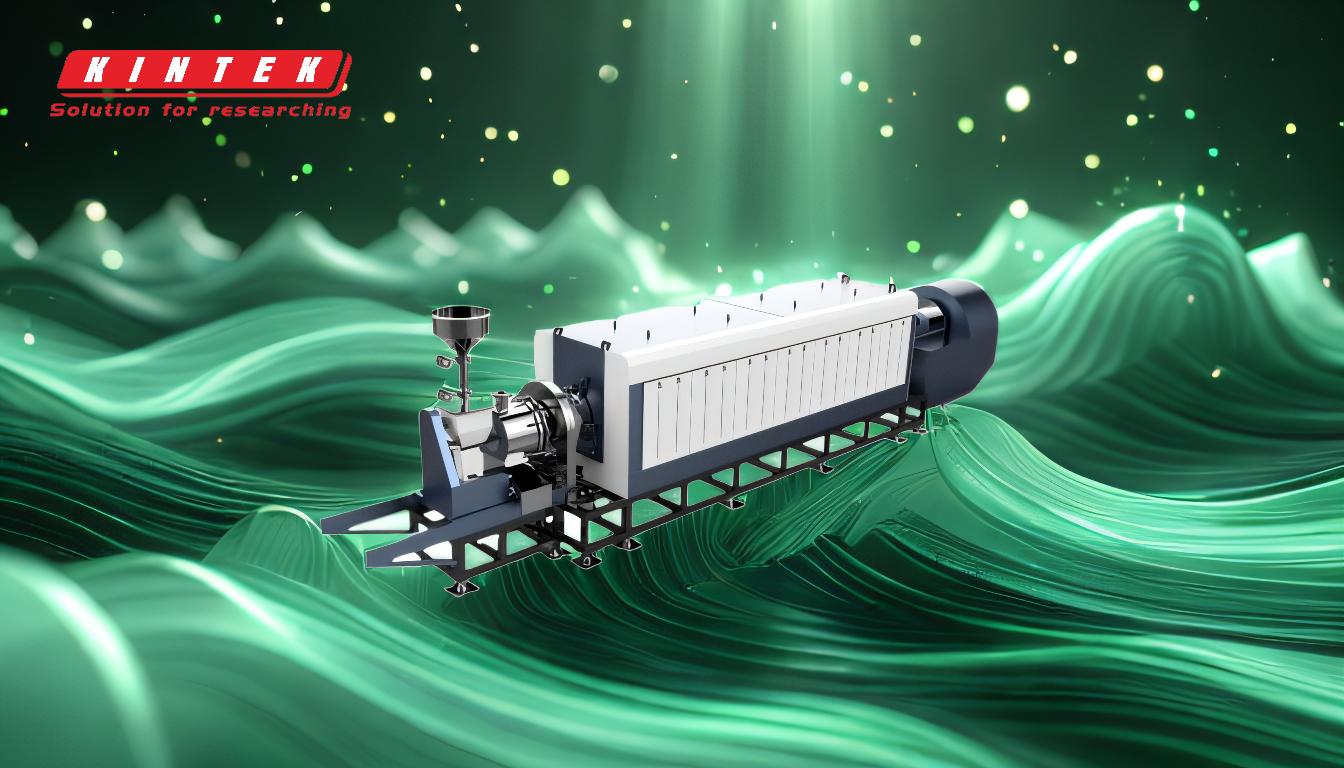
-
Biomass Feedstocks
Biomass is the most common feedstock for pyrolysis due to its renewable nature and abundance. It includes:- Wood and Forestry Residues: Forest trees, branches, sawmill waste, and burned trees are widely used. These materials are rich in lignin and cellulose, making them ideal for pyrolysis.
- Agricultural Residues: Materials like sugarcane bagasse, rice straw, cotton stalks, wheat straw, and corn stover are commonly used. These residues are often by-products of farming and do not compete with food production.
- Municipal Solid Waste (MSW): Organic components of MSW, such as yard waste and food scraps, can be processed through pyrolysis.
- Energy Crops: Dedicated crops like switchgrass and miscanthus, grown specifically for energy production, are suitable feedstocks.
- Algae and Invasive Species: Algae and invasive plants like phragmites and kudzu are emerging as potential feedstocks due to their high growth rates and low competition with food crops.
-
Non-Biomass Feedstocks
Non-biomass materials are increasingly being used in pyrolysis to address waste management challenges and produce valuable outputs:- Tires: Various types of tires, including car, truck, and industrial tires, can be processed. Pyrolysis breaks down the rubber into oil, gas, and carbon black.
- Plastics: Certain plastics like HDPE, LDPE, PP, and PS are suitable for pyrolysis. However, PVC and PET are avoided due to the release of harmful chemicals during decomposition.
- Oil Sludge: Waste materials from oil spills, refinery sludge, and drill cuttings can be converted into useful products through pyrolysis.
- Rubber: Both natural and synthetic rubber products can be processed, providing an alternative to traditional disposal methods like landfilling.
-
Factors Influencing Feedstock Suitability
The choice of feedstock depends on several factors:- Composition: High lignin and cellulose content in biomass makes it more suitable for pyrolysis. For non-biomass materials, the absence of harmful chemicals is crucial.
- Availability: Locally available feedstocks reduce transportation costs and make the process more economically viable.
- Cost: Low-cost or waste materials are preferred to minimize production expenses.
- End Products: The desired outputs (bio-oil, syngas, or biochar) influence the choice of feedstock. For example, high-lignin materials yield more biochar, while plastics produce more oil.
-
Emerging Trends in Feedstock Selection
Recent developments in pyrolysis feedstock include:- Co-Feeding: Combining biomass with non-biomass materials, such as mixed plastics and animal waste, to optimize resource utilization and product yields.
- Waste Valorization: Increasing focus on converting waste materials like tires, plastics, and oil sludge into valuable products, addressing both environmental and economic challenges.
- Diverse Biomass Sources: Exploring unconventional biomass sources like algae and invasive species to diversify feedstock options and reduce reliance on traditional materials.
By understanding the wide range of feedstocks available for pyrolysis, stakeholders can make informed decisions about material selection, process optimization, and product development. This knowledge is particularly valuable for equipment and consumable purchasers, as it helps them tailor their investments to specific feedstock requirements and market demands.
Summary Table:
Category | Examples | Key Characteristics |
---|---|---|
Biomass Feedstocks | Wood, agricultural residues, municipal waste, energy crops, algae | Renewable, abundant, high lignin and cellulose content |
Non-Biomass Feedstocks | Tires, plastics, oil sludge, rubber | Waste-derived, suitable for waste management, produces oil, gas, and carbon black |
Factors Influencing Suitability | Composition, availability, cost, desired end products | Determines feedstock choice for optimal pyrolysis outcomes |
Emerging Trends | Co-feeding, waste valorization, diverse biomass sources | Optimizes resource use, addresses environmental and economic challenges |
Discover how pyrolysis feedstocks can transform your operations—contact our experts today for tailored solutions!