Heat treatment is a critical process in metallurgy that alters the physical and mechanical properties of metals to enhance their performance in various applications. The five basic heat treatment processes of metals are annealing, quenching, tempering, case hardening, and normalizing. Each process involves controlled heating and cooling to achieve specific material properties such as improved ductility, hardness, toughness, and stress relief. These processes are widely used in manufacturing to prepare metals for further processing or to meet the desired functional requirements of the final product.
Key Points Explained:
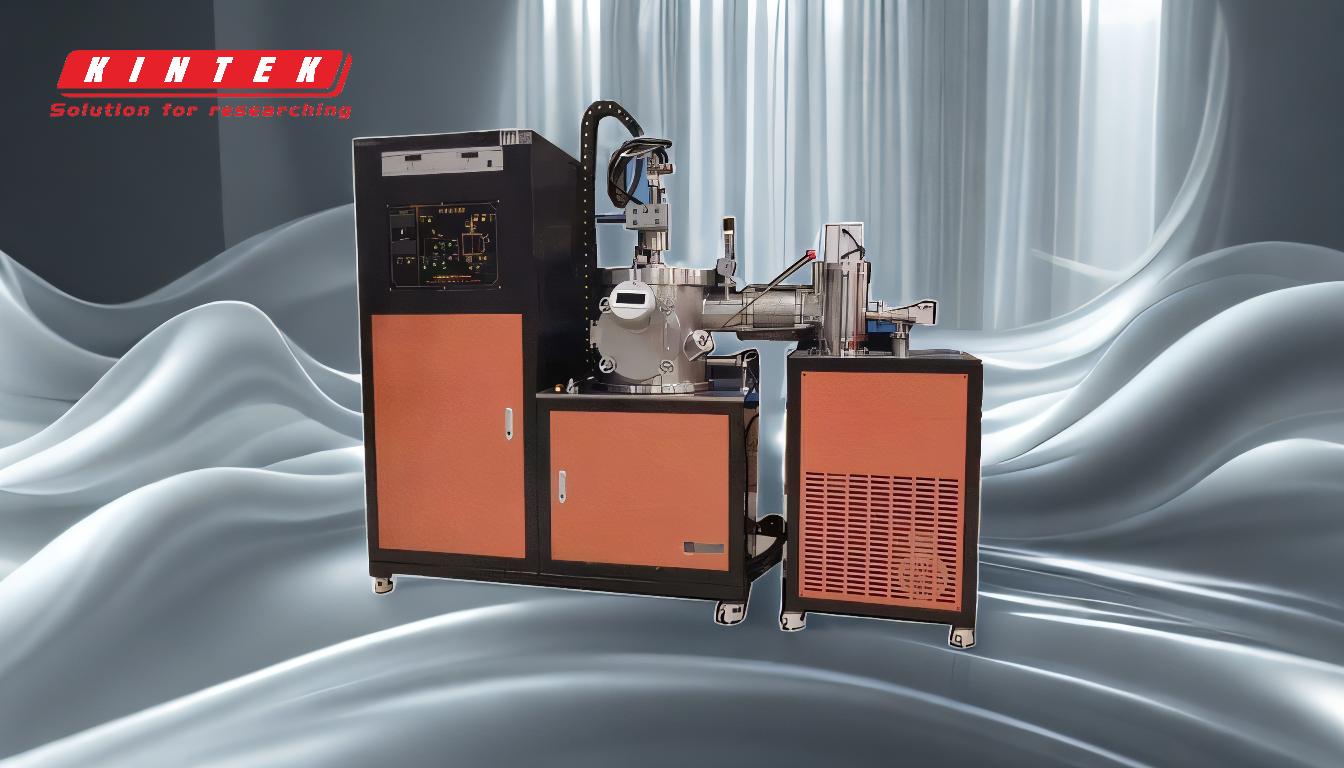
-
Annealing:
- Purpose: Annealing is used to soften metals, improve ductility, and relieve internal stresses.
- Process: The metal is heated to a specific temperature (above its recrystallization temperature) and then slowly cooled in a furnace or air.
- Outcome: This process refines the grain structure, making the metal more workable and less brittle.
- Applications: Commonly used in steel manufacturing to prepare materials for cold working or machining.
-
Quenching:
- Purpose: Quenching is employed to increase the hardness and strength of metals.
- Process: The metal is heated to a high temperature and then rapidly cooled by immersion in water, oil, or another quenching medium.
- Outcome: This creates a hardened structure, often martensite, which is very hard but also brittle.
- Applications: Used in tools, gears, and components requiring high surface hardness.
-
Tempering:
- Purpose: Tempering reduces the brittleness caused by quenching while maintaining hardness.
- Process: The quenched metal is reheated to a temperature below its critical point and then cooled at a controlled rate.
- Outcome: This process improves toughness and reduces internal stresses, balancing hardness and ductility.
- Applications: Essential for tools, springs, and structural components.
-
Case Hardening:
- Purpose: Case hardening increases the surface hardness of metals while maintaining a softer, tougher core.
- Process: Techniques like carburizing, nitriding, or carbonitriding are used to introduce carbon or nitrogen into the surface layer of the metal.
- Outcome: The surface becomes hard and wear-resistant, while the core remains ductile.
- Applications: Ideal for gears, bearings, and components subjected to wear and fatigue.
-
Normalizing:
- Purpose: Normalizing refines the grain structure and improves mechanical properties.
- Process: The metal is heated to a temperature above its upper critical temperature and then cooled in air.
- Outcome: This results in a uniform microstructure, improved strength, and better machinability.
- Applications: Commonly used for steel to prepare it for further heat treatment or machining.
These five processes are fundamental in the heat treatment of metals, each serving a unique purpose to enhance specific properties. Understanding these methods is essential for selecting the appropriate treatment to achieve the desired material characteristics for a given application.
Summary Table:
Process | Purpose | Process Details | Outcome | Applications |
---|---|---|---|---|
Annealing | Soften metals, improve ductility, relieve internal stresses | Heated above recrystallization temperature, then slowly cooled | Refined grain structure, increased workability | Steel manufacturing, cold working, machining |
Quenching | Increase hardness and strength | Heated to high temperature, rapidly cooled in water/oil | Hardened structure (martensite), increased brittleness | Tools, gears, high-hardness components |
Tempering | Reduce brittleness, maintain hardness | Reheated below critical temperature, cooled at controlled rate | Improved toughness, reduced internal stresses | Tools, springs, structural components |
Case Hardening | Increase surface hardness, maintain softer core | Techniques like carburizing, nitriding, or carbonitriding | Hard, wear-resistant surface, ductile core | Gears, bearings, wear-resistant components |
Normalizing | Refine grain structure, improve mechanical properties | Heated above upper critical temperature, cooled in air | Uniform microstructure, improved strength, better machinability | Steel preparation for further heat treatment or machining |
Need expert advice on heat treatment processes? Contact us today to optimize your metal properties!