Heat treatment is a critical process in metallurgy that alters the physical and mechanical properties of metals to make them suitable for specific applications. The four primary types of heat treatment are annealing, hardening, quenching, and tempering. Each method involves controlled heating and cooling to achieve desired outcomes such as increased ductility, hardness, toughness, or stress relief. These processes are essential for enhancing the performance and longevity of metal components in various industries.
Key Points Explained:
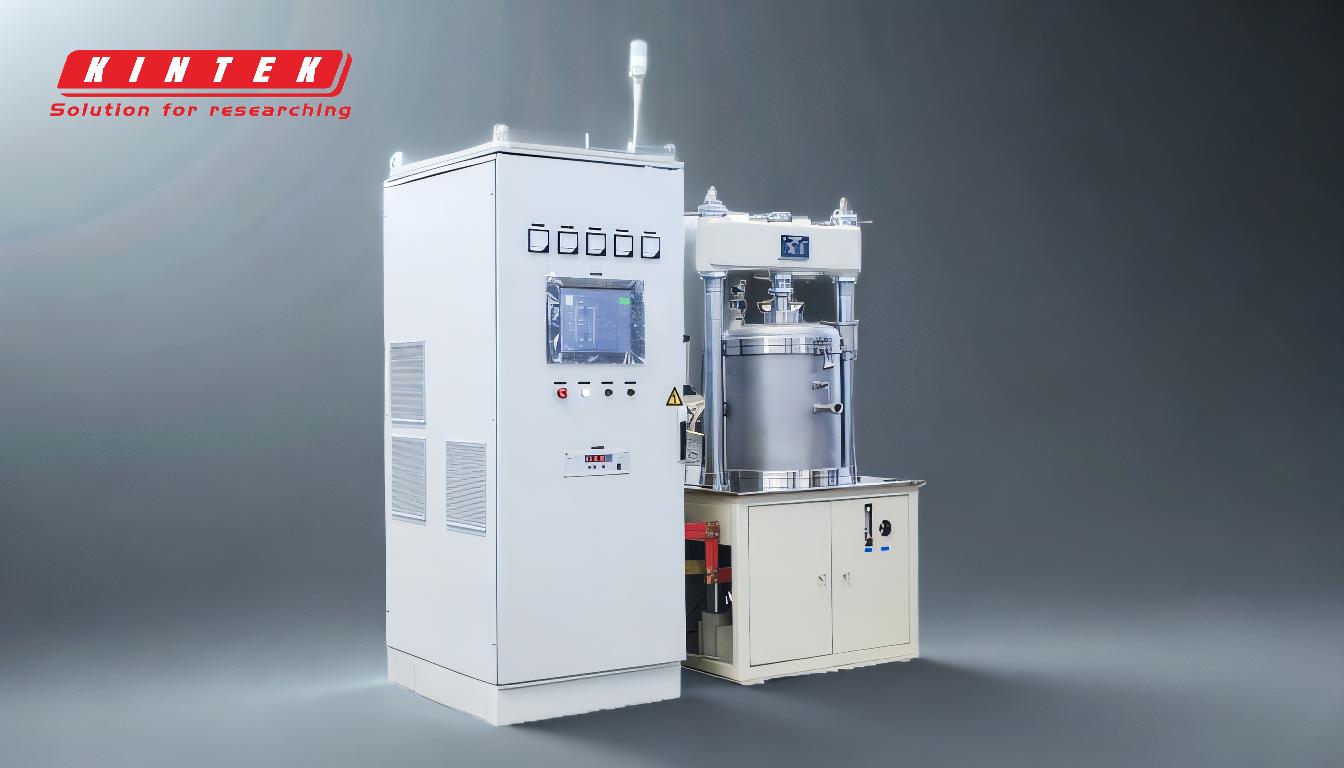
-
Annealing
- Process: Annealing involves heating the metal to a specific temperature (above its recrystallization temperature but below its melting point), holding it at that temperature for a period, and then slowly cooling it.
- Purpose: This process softens the metal, improves ductility, and reduces internal stresses, making it easier to machine or form.
- Mechanism: The heat allows the metal's microstructure to reorganize, reducing dislocations and internal stresses. Slow cooling ensures that the metal remains soft and ductile.
- Applications: Commonly used for steels, copper, and brass to improve workability and prepare them for further processing.
-
Hardening
- Process: Hardening involves heating the metal to a high temperature (above its critical point) and then rapidly cooling it, often through quenching.
- Purpose: This process increases the hardness and strength of the metal by creating a martensitic structure, which is hard but brittle.
- Mechanism: The rapid cooling prevents the formation of softer phases like pearlite, locking the carbon atoms in a supersaturated solution within the metal's crystal lattice.
- Applications: Used for tools, gears, and components that require high wear resistance and strength.
-
Quenching
- Process: Quenching is a rapid cooling process that follows heating. The metal is immersed in a cooling medium like water, oil, or air.
- Purpose: It locks the metal's microstructure in a hardened state, increasing hardness and strength. However, it can also make the metal brittle.
- Mechanism: The rapid cooling rate prevents the formation of softer phases, resulting in a hard, martensitic structure.
- Applications: Often used in conjunction with hardening to achieve high hardness in steels and other alloys.
-
Tempering
- Process: Tempering involves reheating the hardened metal to a temperature below its critical point and then cooling it, usually in air.
- Purpose: This process reduces brittleness and internal stresses while maintaining a balance of hardness and toughness.
- Mechanism: The reheating allows some of the martensite to transform into softer phases like tempered martensite, improving ductility and toughness.
- Applications: Essential for tools, blades, and structural components that require a combination of hardness and resilience.
Summary of Key Differences:
Process | Temperature Range | Cooling Rate | Primary Outcome |
---|---|---|---|
Annealing | Above recrystallization | Slow | Softens, improves ductility |
Hardening | Above critical point | Rapid (quenching) | Increases hardness and strength |
Quenching | After hardening | Very rapid | Locks in hardness, increases brittleness |
Tempering | Below critical point | Slow (air cooling) | Reduces brittleness, balances properties |
By understanding these four heat treatment processes, manufacturers can tailor the properties of metals to meet specific application requirements, ensuring optimal performance and durability.
Summary Table:
Process | Temperature Range | Cooling Rate | Primary Outcome |
---|---|---|---|
Annealing | Above recrystallization | Slow | Softens, improves ductility |
Hardening | Above critical point | Rapid (quenching) | Increases hardness and strength |
Quenching | After hardening | Very rapid | Locks in hardness, increases brittleness |
Tempering | Below critical point | Slow (air cooling) | Reduces brittleness, balances properties |
Optimize your metal components with the right heat treatment—contact our experts today!