Spark plasma sintering (SPS) is an advanced powder metallurgy technique that combines plasma activation, hot pressing, and resistance heating to achieve rapid and efficient sintering of materials. The process leverages Joule heating, plastic deformation, and DC pulse voltage generation between powder particles to facilitate densification at lower temperatures and shorter times compared to conventional sintering methods. Key steps include powder preparation, compaction, controlled heating, and cooling, which result in dense, high-quality sintered products. SPS is particularly advantageous for sintering metals, ceramics, and composites due to its ability to remove impurities, activate particle surfaces, and achieve uniform heating. The process is characterized by its high heating rates, up to 1000°C/min, and the application of electric current, which enhances sintering mechanisms such as surface oxide removal and electromigration.
Key Points Explained:
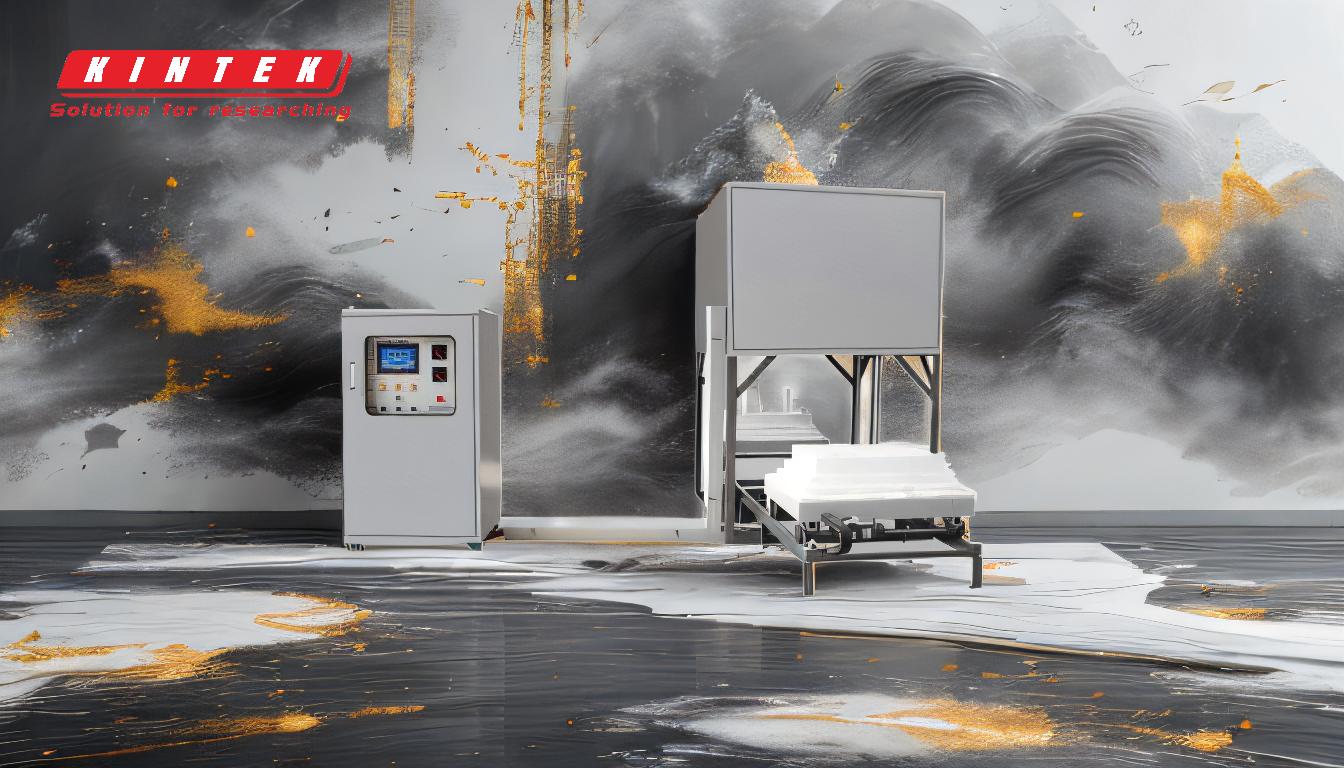
-
Integration of Plasma Activation, Hot Pressing, and Resistance Heating:
- SPS combines three key mechanisms: plasma activation, hot pressing, and resistance heating. This integration allows for rapid and efficient sintering by leveraging Joule heat, plastic deformation, and DC pulse voltage between particles. The process utilizes discharge between particles, surface activation, and self-heating, which are unique to SPS and contribute to its effectiveness.
-
Sintering Mechanism:
- The sintering mechanism in SPS involves several key processes:
- Joule Heating: Heat is generated by the resistance of the powder particles to the electric current, facilitating rapid heating.
- Plastic Deformation: Pressure applied during sintering causes plastic deformation, which helps in eliminating voids and achieving densification.
- DC Pulse Voltage: The generation of DC pulse voltage between particles enhances particle bonding and surface activation.
- The sintering mechanism in SPS involves several key processes:
-
Stages of the Sintering Process:
- The SPS process can be broken down into several stages:
- Powder Preparation: The raw material is prepared in powder form, often mixed with sintering aids or coupling agents to enhance sintering.
- Compaction: The powder is compacted under pressure to form a specific shape and ensure uniformity.
- Heating: The compacted material is subjected to controlled heating, where the temperature is regulated to facilitate particle bonding without complete melting. This stage involves diffusion, neck formation, and densification.
- Cooling: The sintered product is cooled to solidify into a rigid and cohesive structure.
- The SPS process can be broken down into several stages:
-
Advantages of SPS:
- Rapid Sintering: SPS achieves densification at lower temperatures and shorter times compared to conventional methods, with heating rates up to 1000°C/min.
- High-Quality Sintered Products: The process removes impurities and adsorbed gases from powder particles, activates their surfaces, and improves sintering quality and efficiency.
- Versatility: SPS can be used to sinter a wide range of materials, including metals, ceramics, and composites.
-
Key Characteristics of SPS:
- Electric Current Application: The use of electric current enhances sintering by activating mechanisms such as surface oxide removal, electromigration, and electroplasticity.
- High Heating Rate: The ability to achieve high heating rates allows for rapid densification, making SPS suitable for materials that require fast sintering.
-
Applications of SPS:
- SPS is widely used in the preparation of advanced materials, including:
- Metal Alloys: SPS can produce dense metal alloys with improved mechanical properties.
- Ceramics: The process is particularly effective for sintering ceramics, such as silicon carbide (SiC) with sintering aids like Al2O3 and Y2O3, to achieve dense structures.
- Composites: SPS is used to create composite materials with enhanced properties by sintering different materials together.
- SPS is widely used in the preparation of advanced materials, including:
In summary, spark plasma sintering is a highly efficient and versatile sintering technique that leverages the integration of plasma activation, hot pressing, and resistance heating to achieve rapid densification of materials. Its unique mechanisms, including Joule heating, plastic deformation, and DC pulse voltage, make it particularly effective for sintering a wide range of materials, resulting in high-quality, dense sintered products.
Summary Table:
Key Aspect | Details |
---|---|
Integration of Mechanisms | Combines plasma activation, hot pressing, and resistance heating. |
Sintering Mechanism | Joule heating, plastic deformation, and DC pulse voltage enhance bonding. |
Process Stages | Powder preparation, compaction, controlled heating, and cooling. |
Advantages | Rapid sintering, high-quality products, and versatility for various materials. |
Key Characteristics | Electric current application and high heating rates (up to 1000°C/min). |
Applications | Metal alloys, ceramics, and composites with enhanced properties. |
Unlock the potential of spark plasma sintering for your materials—contact our experts today!