Graphene transfer techniques are essential for moving graphene from its growth substrate to a target substrate for various applications. These techniques ensure the integrity, cleanliness, and functionality of graphene during the transfer process. The most common methods include wet transfer, dry transfer, and electrochemical delamination. Each method has its advantages and limitations, depending on the application requirements, such as avoiding contamination, maintaining structural integrity, or achieving large-area transfers. Below, we explore the key techniques in detail, their mechanisms, and their suitability for different scenarios.
Key Points Explained:
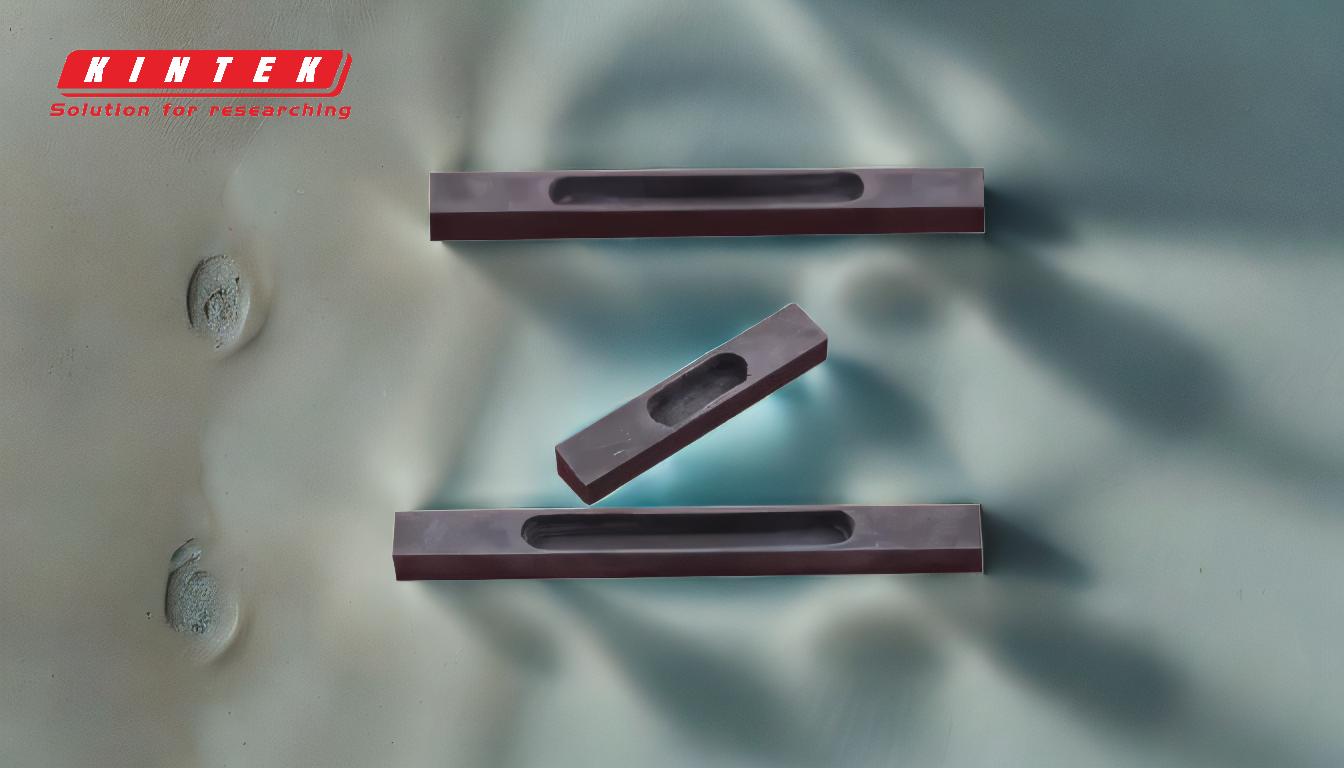
-
Wet Transfer Technique:
- Process: This method involves using a polymer support layer (e.g., PMMA) to coat the graphene on its growth substrate (often copper or nickel). The substrate is then etched away using a chemical solution (e.g., ferric chloride for copper), leaving the graphene on the polymer film. The graphene-polymer stack is transferred to the target substrate, and the polymer is dissolved using solvents like acetone.
-
Advantages:
- Suitable for large-area transfers.
- Effective for transferring graphene onto various substrates, including silicon wafers and glass.
-
Limitations:
- Risk of introducing contaminants from the polymer and etching chemicals.
- Potential for cracks or tears due to mechanical handling.
-
Dry Transfer Technique:
- Process: In this method, graphene is directly lifted from its growth substrate using a stamping material (e.g., PDMS or thermal release tape). The stamp is pressed onto the graphene, and the growth substrate is peeled away. The graphene is then stamped onto the target substrate, often with heat or pressure to ensure adhesion.
-
Advantages:
- Minimal chemical contamination compared to wet transfer.
- Better preservation of graphene's intrinsic properties.
-
Limitations:
- Challenging for large-area transfers.
- Requires precise alignment and control during stamping.
-
Electrochemical Delamination:
- Process: This technique uses an electrochemical cell to delaminate graphene from its growth substrate. A voltage is applied to the substrate, causing hydrogen bubbles to form at the graphene-substrate interface, which lifts the graphene. The graphene is then transferred to the target substrate.
-
Advantages:
- Clean and efficient transfer with minimal contamination.
- Suitable for high-quality graphene required for electronic applications.
-
Limitations:
- Requires specialized equipment and setup.
- Limited to specific growth substrates.
-
Comparison of Techniques:
- Wet Transfer: Best for large-area applications but may introduce contaminants.
- Dry Transfer: Ideal for high-quality, small-area transfers with minimal contamination.
- Electrochemical Delamination: Offers clean transfers for high-performance applications but is more complex.
-
Applications and Considerations:
- Electronics: Dry transfer and electrochemical delamination are preferred for high-performance electronic devices due to their cleanliness and preservation of graphene's properties.
- Optics and Sensors: Wet transfer is often used for large-area applications like transparent conductive films or sensors.
- Research and Development: The choice of technique depends on the specific requirements of the experiment, such as substrate compatibility and desired graphene quality.
By understanding these techniques, researchers and engineers can select the most appropriate method for their specific graphene transfer needs, balancing factors like contamination risk, scalability, and application requirements.
Summary Table:
Technique | Advantages | Limitations | Best For |
---|---|---|---|
Wet Transfer | - Suitable for large-area transfers. | - Risk of contamination. | Optics, sensors, and large-area applications. |
- Works on various substrates (e.g., silicon wafers, glass). | - Potential for mechanical damage. | ||
Dry Transfer | - Minimal chemical contamination. | - Challenging for large-area transfers. | High-quality, small-area electronic devices. |
- Preserves graphene's intrinsic properties. | - Requires precise alignment and control. | ||
Electrochemical Delamination | - Clean and efficient transfer. | - Requires specialized equipment. | High-performance electronic applications. |
- Minimal contamination. | - Limited to specific growth substrates. |
Need help choosing the right graphene transfer technique? Contact our experts today for tailored solutions!