Heat treatment is a critical process in metallurgy, and its success depends on several key factors. These include precise control of temperature, time, and cooling rates, as well as considerations like uniform temperature distribution, gas circulation, and cycle optimization. The type of material, its end application, and desired properties also play a significant role in determining the heat treatment process. Properly managing these factors ensures the material achieves the necessary metallurgical transformation without compromising quality or causing downtime.
Key Points Explained:
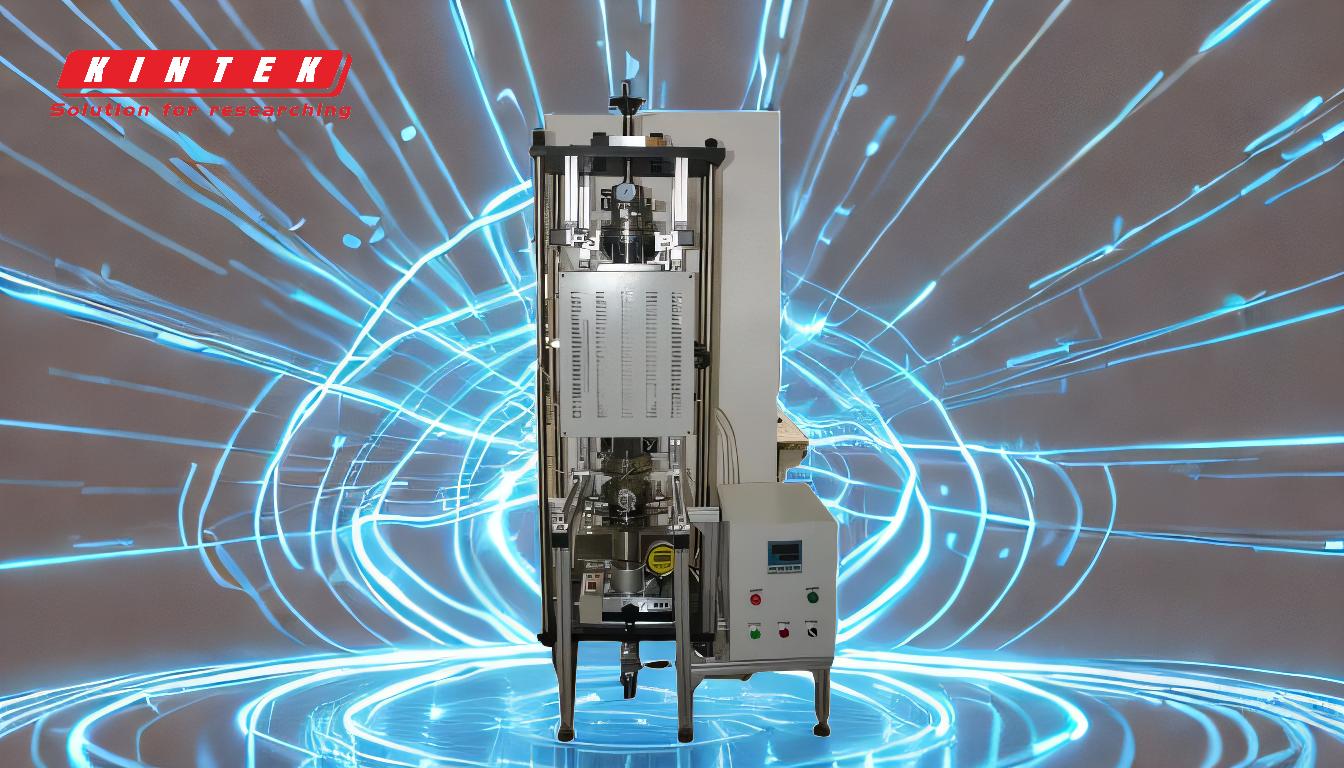
-
Temperature Control:
- Precision: Temperature must be controlled within tight tolerances to ensure the material reaches the required state for transformation.
- Restrictions: Maximum temperatures must not exceed limits to avoid damaging the material.
- Heat-Up and Cool-Down Rates: Controlled rates are essential to prevent thermal stress and ensure uniform transformation.
-
Time at Temperature:
- Holding Time: The duration the material is held at the target temperature directly impacts the metallurgical changes. Too short or too long can lead to under- or over-treatment.
- Process Time Optimization: Minimizing process time without compromising quality is critical for efficiency.
-
Cooling Method and Rate:
- Cooling Techniques: Methods like quenching, air cooling, or furnace cooling are chosen based on the desired material properties.
- Rate Control: The cooling rate affects the final microstructure and hardness of the material.
-
Uniform Temperature Distribution:
- Hot Zone Uniformity: Ensuring even temperature distribution throughout the material prevents inconsistencies in properties.
- Gas Circulation: Proper gas flow (e.g., partial pressure or quench gas) is vital for uniform heating and cooling.
-
Material and Application Considerations:
- Material Type: Different materials require specific heat treatment parameters to achieve desired properties.
- End Application: The intended use of the part determines whether full or localized heat treatment is necessary.
-
Cycle Optimization:
- Cycle Times and Temperatures: These must be carefully chosen to balance efficiency and quality.
- Problem Anticipation: Identifying potential issues (e.g., equipment failure or process deviations) helps avoid downtime and maintenance costs.
-
Quality Assurance:
- Final Product Quality: Factors like uniform heating, proper cooling, and adherence to process parameters ensure consistent and high-quality results.
- Metallurgical Integrity: Maintaining the material's metallurgical properties is paramount to avoid defects or failures.
By carefully managing these critical factors, heat treatment processes can achieve the desired material properties while maintaining efficiency and quality.
Summary Table:
Key Factor | Details |
---|---|
Temperature Control | Precision, restrictions, and controlled heat-up/cool-down rates. |
Time at Temperature | Holding time and process time optimization for efficiency. |
Cooling Method and Rate | Techniques like quenching, air cooling, and rate control for microstructure. |
Uniform Temperature Distribution | Hot zone uniformity and gas circulation for consistency. |
Material and Application | Material type and end application considerations. |
Cycle Optimization | Cycle times, temperatures, and problem anticipation. |
Quality Assurance | Uniform heating, proper cooling, and metallurgical integrity. |
Ensure your heat treatment process achieves the best results—contact our experts today!