High-temperature furnaces operating in oxidizing environments require specific elements and materials that can withstand extreme conditions without degrading. Key materials include platinum, tungsten disilicide, molybdenum disilicide, molybdenum, and silicon carbide for heating elements, as they offer excellent thermal stability and resistance to oxidation. Additionally, alumina tubes and furnace chambers made of alumina ceramic or quartz glass are essential for maintaining structural integrity and thermal performance. These materials are chosen for their high temperature resistance, corrosion resistance, and, in the case of quartz glass, transparency for process observation.
Key Points Explained:
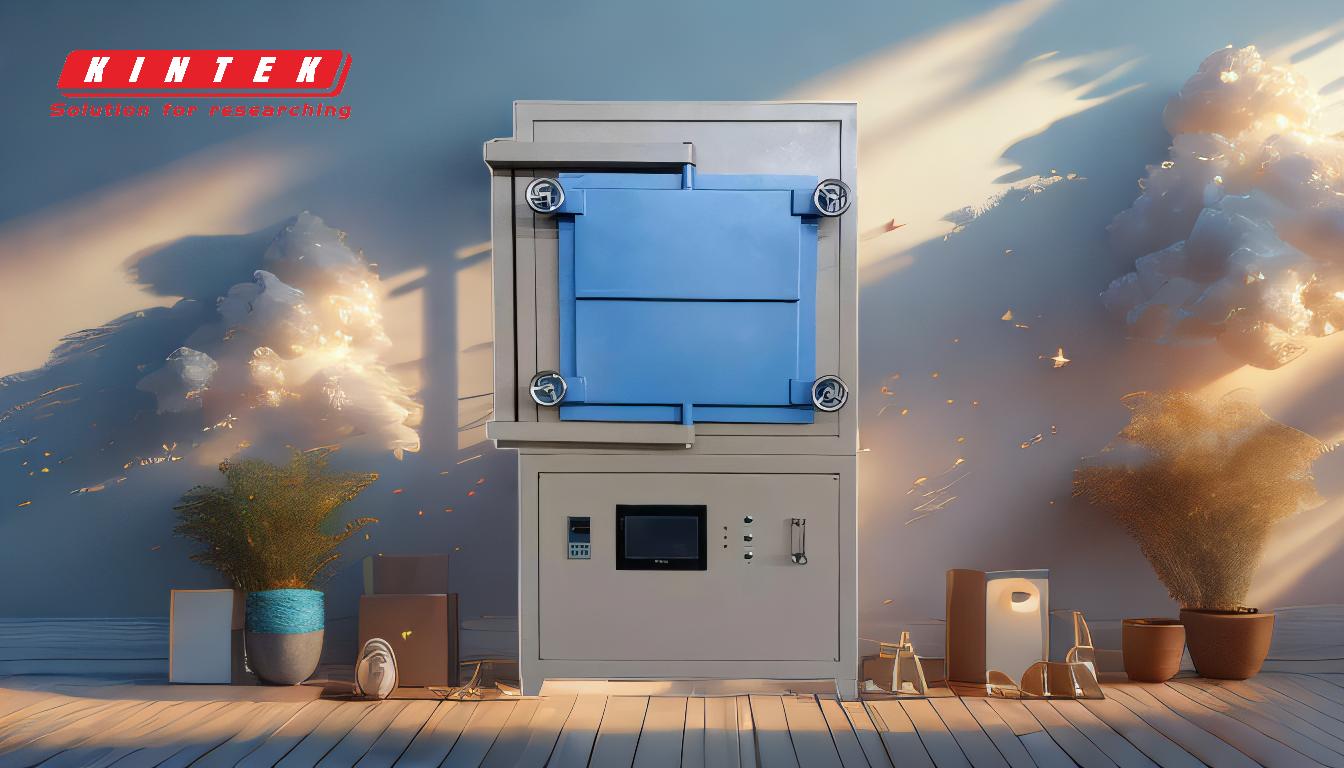
-
Heating Elements for Oxidizing Environments:
- Platinum: Platinum is highly resistant to oxidation and can withstand extreme temperatures, making it ideal for use in oxidizing environments. However, its high cost limits its use to specialized applications.
- Tungsten Disilicide (WSi₂): This material is known for its excellent oxidation resistance and high melting point, making it suitable for high-temperature applications.
- Molybdenum Disilicide (MoSi₂): MoSi₂ heating elements are widely used in oxidizing environments due to their ability to form a protective silicon oxide layer at high temperatures, which prevents further oxidation.
- Molybdenum: While molybdenum has excellent high-temperature strength, it is prone to oxidation at elevated temperatures unless used in a protective atmosphere.
- Silicon Carbide (SiC): Silicon carbide is a popular choice for heating elements in oxidizing environments due to its high thermal conductivity, oxidation resistance, and durability at high temperatures.
-
Alumina Tubes for High-Temperature Applications:
- Alumina tubes are essential components in tube furnaces, providing a stable environment for high-temperature processes. They are made from alumina (Al₂O₃), which offers excellent thermal shock resistance and high-temperature stability.
- Smaller-diameter alumina tubes perform better in terms of thermal shock resistance, as they can dissipate heat more efficiently and reduce the risk of cracking.
-
Furnace Chamber Materials:
- Alumina Ceramic: Alumina ceramic is commonly used for furnace chambers due to its high temperature resistance, corrosion resistance, and mechanical strength. It is ideal for applications requiring a robust and durable material.
- Quartz Glass: Quartz glass is another material used for furnace chambers, particularly in applications where transparency is necessary to observe the experimental process. It offers excellent thermal stability and resistance to thermal shock.
-
Considerations for High-Temperature Furnace Design:
- Thermal Shock Resistance: Materials must be able to withstand rapid temperature changes without cracking or degrading.
- Oxidation Resistance: In oxidizing environments, materials must resist oxidation to maintain their structural integrity and performance.
- Thermal Conductivity: High thermal conductivity ensures efficient heat transfer and uniform temperature distribution within the furnace.
- Cost and Availability: While exotic materials like platinum offer superior performance, their high cost may limit their use. Alternatives like silicon carbide provide a balance of performance and affordability.
By carefully selecting materials and components such as high temperature furnace elements, alumina tubes, and furnace chambers, manufacturers can ensure reliable and efficient operation in oxidizing environments. This approach minimizes degradation and maximizes the lifespan of the furnace, making it suitable for demanding industrial and research applications.
Summary Table:
Material | Key Properties | Applications |
---|---|---|
Platinum | High oxidation resistance, extreme temperature stability | Specialized high-temperature applications |
Tungsten Disilicide | Excellent oxidation resistance, high melting point | High-temperature heating elements |
Molybdenum Disilicide | Forms protective silicon oxide layer, resists oxidation | Widely used in oxidizing environments |
Molybdenum | High-temperature strength, requires protective atmosphere | High-temperature processes in controlled environments |
Silicon Carbide | High thermal conductivity, oxidation resistance, durability | Popular choice for heating elements in oxidizing environments |
Alumina Tubes | Thermal shock resistance, high-temperature stability | Essential for tube furnaces in high-temperature processes |
Alumina Ceramic | High temperature resistance, corrosion resistance, mechanical strength | Ideal for robust furnace chambers |
Quartz Glass | Thermal stability, transparency for process observation | Furnace chambers requiring visibility and thermal shock resistance |
Need help selecting the right materials for your high-temperature furnace? Contact our experts today for tailored solutions!