Induction brazing, while efficient and precise, has several limitations that can impact its effectiveness in certain applications. These limitations include the need for clean, oxide-free materials, the potential loss of alloying elements due to oxidation, and challenges with materials like aluminum that form stable oxide layers. Additionally, precise temperature control and homogeneous thermal distribution are critical, especially when working with materials that have closely matched melting ranges. Understanding these limitations is essential for selecting the appropriate brazing method and ensuring high-quality results.
Key Points Explained:
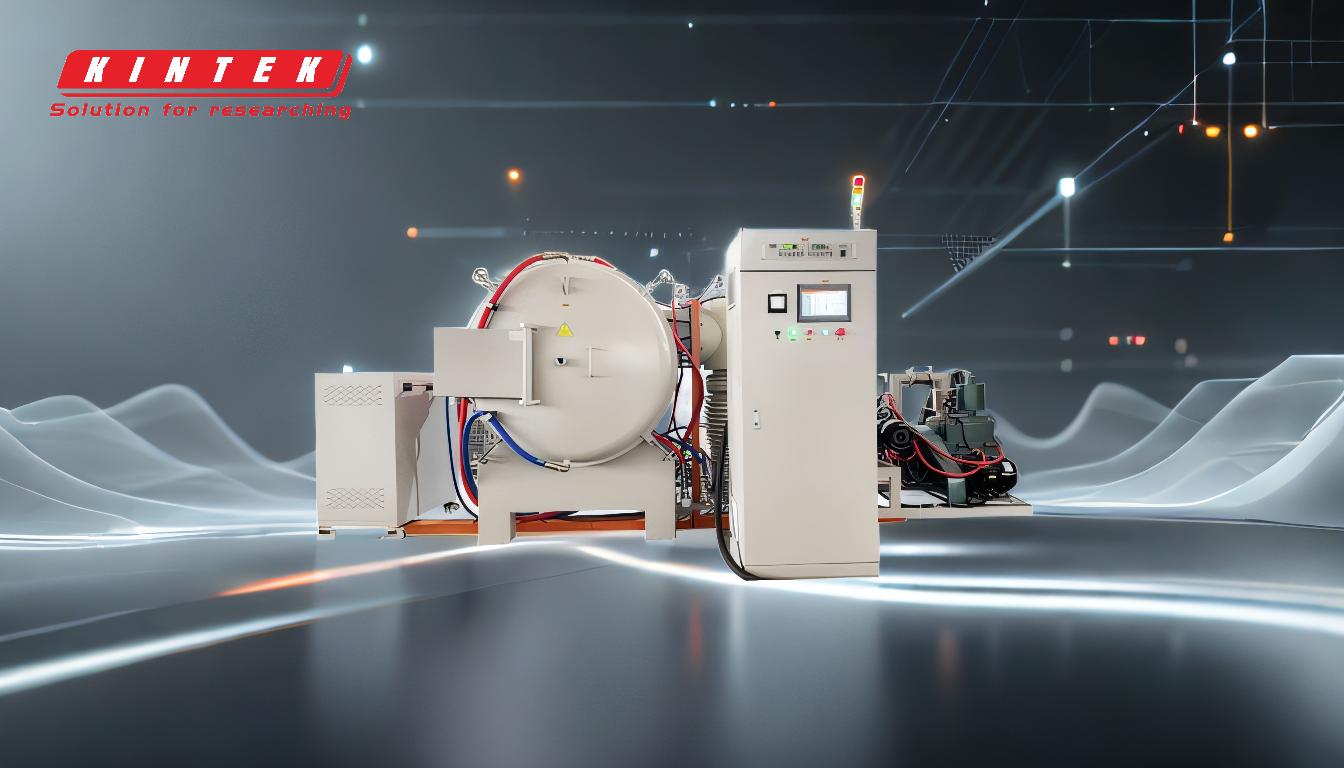
-
Lack of Refining Capacity:
- Induction brazing requires charge materials to be free of oxides and of a known composition. This means that any impurities or oxides present in the materials can negatively affect the brazing process.
- The process does not have the capability to refine or purify the materials during brazing, which can be a significant drawback when working with materials that are prone to oxidation or contamination.
-
Oxidation and Loss of Alloying Elements:
- During the induction brazing process, some alloying elements may be lost due to oxidation. This necessitates the re-addition of these elements to the melt to achieve the desired composition.
- The loss of alloying elements can lead to inconsistencies in the final product, requiring careful monitoring and adjustment during the brazing process.
-
Challenges with Aluminum and Other Oxidizable Materials:
- Aluminum, in particular, is highly oxidizable and forms a stable aluminum oxide layer (Al2O3) that can prevent filler metals from wetting the surface. This oxide layer must be suppressed before brazing and prevented from reforming until the filler metal solidifies.
- The need to manage this oxide layer adds complexity to the brazing process, requiring additional steps and precautions to ensure a successful bond.
-
Precise Temperature Control and Homogeneous Thermal Distribution:
- Induction brazing requires precise temperature control, especially when the melting ranges of the base and filler metals are very close. Any deviation in temperature can lead to incomplete brazing or damage to the materials.
- Achieving homogeneous thermal distribution is also critical to ensure that the entire joint reaches the necessary temperature uniformly. Inconsistent heating can result in weak joints or localized overheating, which can compromise the integrity of the brazed assembly.
-
Material Compatibility:
- Not all materials are suitable for induction brazing. Materials that are highly reactive or have complex compositions may require alternative brazing methods to achieve the desired results.
- The compatibility of the base and filler metals must be carefully considered to ensure that they can form a strong, durable bond without adverse reactions.
-
Equipment and Process Complexity:
- Induction brazing equipment can be complex and expensive, requiring skilled operators to manage the process effectively.
- The process itself can be more complex than other brazing methods, necessitating a thorough understanding of the materials, equipment, and techniques involved.
In summary, while induction brazing offers many advantages, including rapid heating and precise control, it also has several limitations that must be carefully managed. These include the need for clean, oxide-free materials, the potential loss of alloying elements, challenges with oxidizable materials like aluminum, and the requirement for precise temperature control and homogeneous thermal distribution. Understanding these limitations is crucial for selecting the appropriate brazing method and ensuring high-quality results.
Summary Table:
Limitation | Key Challenges |
---|---|
Lack of Refining Capacity | Requires clean, oxide-free materials; no refining during brazing. |
Oxidation and Loss of Alloying Elements | Alloying elements may oxidize, requiring re-addition and careful monitoring. |
Challenges with Aluminum | Aluminum oxide layer must be suppressed and managed for successful brazing. |
Precise Temperature Control | Critical for materials with closely matched melting ranges. |
Material Compatibility | Not all materials are suitable; base and filler metals must be compatible. |
Equipment and Process Complexity | Requires skilled operators and complex, expensive equipment. |
Need help overcoming induction brazing challenges? Contact our experts today for tailored solutions!