Preventive maintenance for a hydraulic system is essential to ensure its longevity, efficiency, and reliability. By regularly inspecting, cleaning, and servicing the system, potential issues can be identified and addressed before they lead to costly breakdowns or failures. This involves tasks such as checking fluid levels, inspecting hoses and seals, monitoring pressure levels, and cleaning components. A well-maintained hydraulic system not only operates more efficiently but also minimizes downtime and extends the lifespan of the equipment.
Key Points Explained:
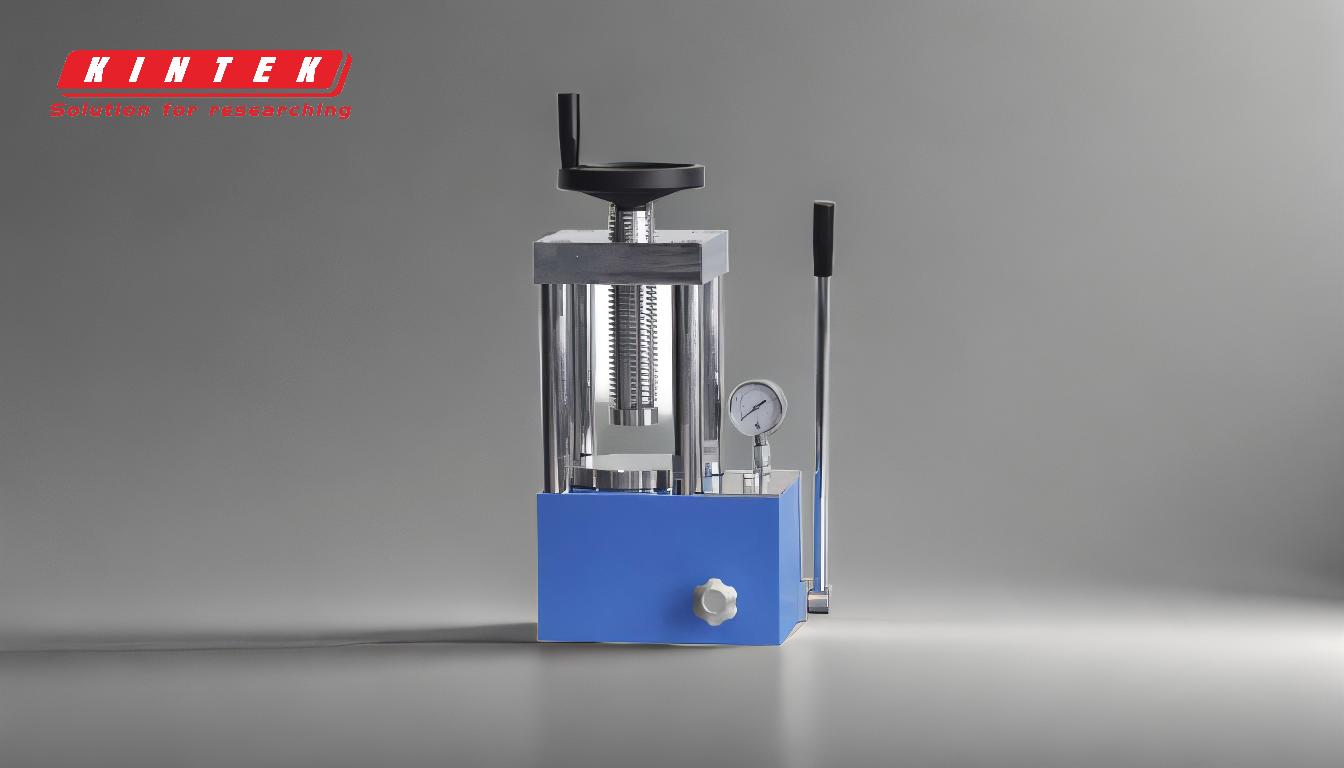
-
Regularly Check Hydraulic Fluid Levels and Quality
- Why it's important: Hydraulic fluid is the lifeblood of the system, and its quality directly impacts performance. Low or contaminated fluid can lead to overheating, increased wear, and system failure.
-
How to do it:
- Check fluid levels weekly or as recommended by the manufacturer.
- Inspect the fluid for contamination, such as water, dirt, or metal particles.
- Replace the fluid if it appears discolored or has a burnt smell.
- Use the correct type of hydraulic fluid as specified in the system's manual.
-
Inspect Hoses, Seals, and Fittings for Wear and Leaks
- Why it's important: Damaged hoses, seals, or fittings can cause leaks, leading to fluid loss and reduced system efficiency. They can also pose safety hazards.
-
How to do it:
- Look for cracks, bulges, or abrasions on hoses.
- Check for leaks around seals and fittings.
- Tighten loose fittings and replace worn-out components immediately.
- Schedule routine inspections to catch issues early.
-
Monitor System Pressure and Temperature
- Why it's important: Abnormal pressure or temperature levels can indicate underlying problems, such as blockages, pump issues, or excessive load.
-
How to do it:
- Use pressure gauges to ensure the system operates within the recommended range.
- Monitor temperature using sensors or infrared thermometers.
- Investigate and resolve any deviations from normal operating conditions.
-
Clean and Replace Filters Regularly
- Why it's important: Filters prevent contaminants from entering the hydraulic system, which can cause damage to components like pumps and valves.
-
How to do it:
- Check filters for clogs or damage during routine maintenance.
- Clean or replace filters as per the manufacturer's guidelines.
- Use high-quality filters that match the system's specifications.
-
Inspect and Lubricate Moving Parts
- Why it's important: Proper lubrication reduces friction and wear on moving components, ensuring smooth operation and preventing premature failure.
-
How to do it:
- Identify all moving parts that require lubrication, such as cylinders and linkages.
- Apply the appropriate lubricant as specified in the manual.
- Avoid over-lubrication, which can attract dirt and debris.
-
Check for Abnormal Noises or Vibrations
- Why it's important: Unusual noises or vibrations can indicate issues like cavitation, air entrapment, or misalignment.
-
How to do it:
- Listen for knocking, whining, or grinding sounds during operation.
- Feel for excessive vibrations in the system.
- Investigate and address the root cause of any abnormalities.
-
Perform System Flushing and Cleaning
- Why it's important: Over time, contaminants can accumulate in the system, leading to reduced efficiency and potential damage.
-
How to do it:
- Flush the system with clean hydraulic fluid to remove debris.
- Clean reservoirs, pumps, and valves thoroughly.
- Schedule flushing as part of a comprehensive maintenance plan.
-
Test and Calibrate System Components
- Why it's important: Accurate calibration ensures the system operates at optimal performance levels.
-
How to do it:
- Test pressure relief valves, flow controls, and other critical components.
- Calibrate sensors and gauges to ensure accurate readings.
- Follow the manufacturer's guidelines for testing and calibration procedures.
-
Keep Detailed Maintenance Records
- Why it's important: Documentation helps track maintenance activities, identify recurring issues, and plan future tasks.
-
How to do it:
- Record all inspections, repairs, and replacements.
- Note any abnormalities or changes in system performance.
- Use a digital or paper-based logbook for easy reference.
-
Train Personnel on Proper Maintenance Practices
- Why it's important: Skilled personnel are better equipped to identify and address issues, reducing the risk of errors and accidents.
-
How to do it:
- Provide training on hydraulic system components and maintenance procedures.
- Emphasize safety protocols and the importance of regular inspections.
- Encourage continuous learning and adherence to best practices.
By following these preventive maintenance tasks, hydraulic system operators can ensure reliable performance, minimize downtime, and extend the lifespan of their equipment. Regular maintenance not only saves costs but also enhances safety and productivity in the long run.
Summary Table:
Task | Why It's Important | How to Do It |
---|---|---|
Check Hydraulic Fluid Levels & Quality | Ensures optimal performance; prevents overheating and system failure. | Inspect weekly, check for contamination, replace if discolored, use correct fluid type. |
Inspect Hoses, Seals, and Fittings | Prevents leaks, fluid loss, and safety hazards. | Look for cracks, tighten fittings, replace worn parts, schedule routine inspections. |
Monitor Pressure & Temperature | Detects blockages, pump issues, or excessive load. | Use gauges and sensors, investigate deviations, resolve abnormalities. |
Clean and Replace Filters | Prevents contaminants from damaging pumps and valves. | Check for clogs, clean or replace filters, use high-quality filters. |
Inspect and Lubricate Moving Parts | Reduces friction, ensures smooth operation, and prevents premature failure. | Apply appropriate lubricant, avoid over-lubrication, identify all moving parts needing lubrication. |
Check for Abnormal Noises or Vibrations | Identifies cavitation, air entrapment, or misalignment. | Listen for unusual sounds, feel for vibrations, investigate root causes. |
Perform System Flushing and Cleaning | Removes contaminants, maintains efficiency, and prevents damage. | Flush with clean fluid, clean reservoirs and valves, schedule regular flushing. |
Test and Calibrate System Components | Ensures optimal performance and accurate readings. | Test valves and sensors, calibrate gauges, follow manufacturer guidelines. |
Keep Detailed Maintenance Records | Tracks activities, identifies recurring issues, and plans future tasks. | Record inspections, repairs, and abnormalities; use a logbook. |
Train Personnel on Maintenance Practices | Reduces errors, enhances safety, and ensures proper system handling. | Provide training, emphasize safety, encourage continuous learning. |
Need expert advice on maintaining your hydraulic system? Contact us today for tailored solutions and support!