Thin film coating methods are essential for creating high-quality, uniform layers on substrates, with applications ranging from electronics to optics. The primary techniques include Physical Vapor Deposition (PVD) and Chemical Vapor Deposition (CVD), each encompassing several methods. PVD involves vaporizing a solid material in a vacuum and depositing it onto a substrate, with techniques like thermal evaporation, sputtering, and electron-beam deposition. CVD relies on chemical reactions to produce thin films, often achieving uniform coatings over large areas. Other methods like Atomic Layer Deposition (ALD) and Spray Pyrolysis offer precise control and versatility. Understanding these methods helps in selecting the right technique for specific applications.
Key Points Explained:
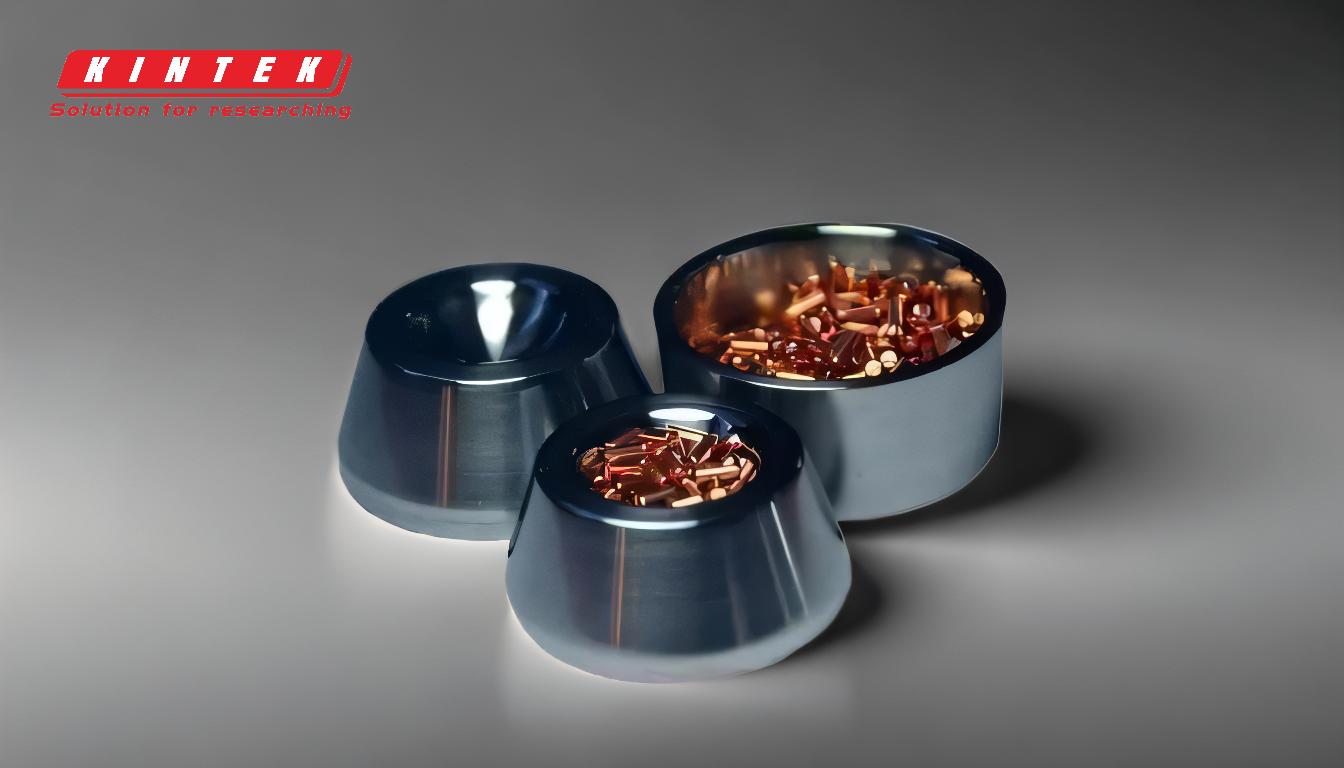
-
Physical Vapor Deposition (PVD):
- PVD involves vaporizing a solid material in a vacuum and depositing it onto a substrate.
- Thermal Evaporation: A material is heated until it vaporizes, and the vapor condenses on the substrate. This method is simple and cost-effective but may lack uniformity for complex shapes.
- Sputtering: A target material is bombarded with ions, ejecting atoms that deposit onto the substrate. This technique offers better adhesion and uniformity compared to evaporation.
- Electron-Beam Deposition: An electron beam heats the material to high temperatures, vaporizing it for deposition. This method is precise and suitable for high-melting-point materials.
- Magnetron Sputtering: A variation of sputtering that uses magnetic fields to enhance the ionization of gas, improving deposition rates and film quality.
-
Chemical Vapor Deposition (CVD):
- CVD involves chemical reactions to deposit thin films on a substrate.
- A precursor gas decomposes on a heated substrate, forming a solid film. This method is ideal for producing high-purity, uniform coatings over large areas.
- Chemical Bath Deposition: A substrate is immersed in a solution containing precursor chemicals, which react to form a thin film. This method is simple and cost-effective but may lack precision.
- Electroplating: A substrate is coated by passing an electric current through a solution containing metal ions. This technique is widely used for metallic coatings.
- Molecular Beam Epitaxy (MBE): A highly controlled process where beams of atoms or molecules are directed at a substrate to grow thin films layer by layer. This method is used for high-precision applications like semiconductors.
- Thermal Oxidation: A substrate is exposed to an oxidizing environment at high temperatures, forming a thin oxide layer. This method is commonly used in semiconductor manufacturing.
-
Atomic Layer Deposition (ALD):
- ALD deposits thin films one atomic layer at a time, offering exceptional control over film thickness and composition.
- This method involves alternating exposures of the substrate to precursor gases, ensuring precise and uniform coatings. ALD is ideal for applications requiring high precision, such as nanoscale devices.
-
Spray Pyrolysis:
- Spray Pyrolysis involves spraying a solution containing precursor materials onto a heated substrate.
- The solution thermally decomposes, forming a thin film. This method is versatile and can be used for a wide range of materials, including oxides and metals.
-
Comparison of Techniques:
- PVD is generally faster and more cost-effective but may struggle with uniformity on complex shapes.
- CVD offers better uniformity and is suitable for large-area coatings but can be more expensive and require higher temperatures.
- ALD provides unparalleled precision but is slower and more costly.
- Spray Pyrolysis is versatile and scalable but may lack the precision of other methods.
-
Applications:
- PVD is widely used in optics, electronics, and decorative coatings.
- CVD is essential for semiconductor manufacturing, solar cells, and protective coatings.
- ALD is critical for advanced electronics, such as nanoscale transistors and memory devices.
- Spray Pyrolysis is used in energy storage, sensors, and transparent conductive films.
By understanding these methods, purchasers can select the appropriate thin film deposition technique based on factors like material type, substrate complexity, required precision, and budget.
Summary Table:
Method | Key Features | Applications |
---|---|---|
PVD | Fast, cost-effective, good adhesion, but may lack uniformity on complex shapes. | Optics, electronics, decorative coatings |
CVD | High-purity, uniform coatings, suitable for large areas, but higher cost. | Semiconductors, solar cells, protective films |
ALD | Atomic-level precision, ideal for nanoscale devices, slower and costly. | Advanced electronics, memory devices |
Spray Pyrolysis | Versatile, scalable, but may lack precision. | Energy storage, sensors, conductive films |
Need help choosing the right thin film coating method? Contact our experts today for personalized advice!