The deposition of Indium Tin Oxide (ITO) involves both chemical and physical methods, each offering unique advantages depending on the application requirements. Chemical methods include techniques like chemical vapor deposition (CVD), plasma-enhanced CVD (PECVD), and atomic layer deposition (ALD), which are known for their precision and control over film properties. Physical methods, primarily physical vapor deposition (PVD), encompass sputtering, thermal evaporation, electron beam evaporation, and pulsed laser deposition (PLD), which are widely used for their ability to produce high-quality, uniform films. These methods are chosen based on factors such as substrate type, desired film properties, and specific application needs.
Key Points Explained:
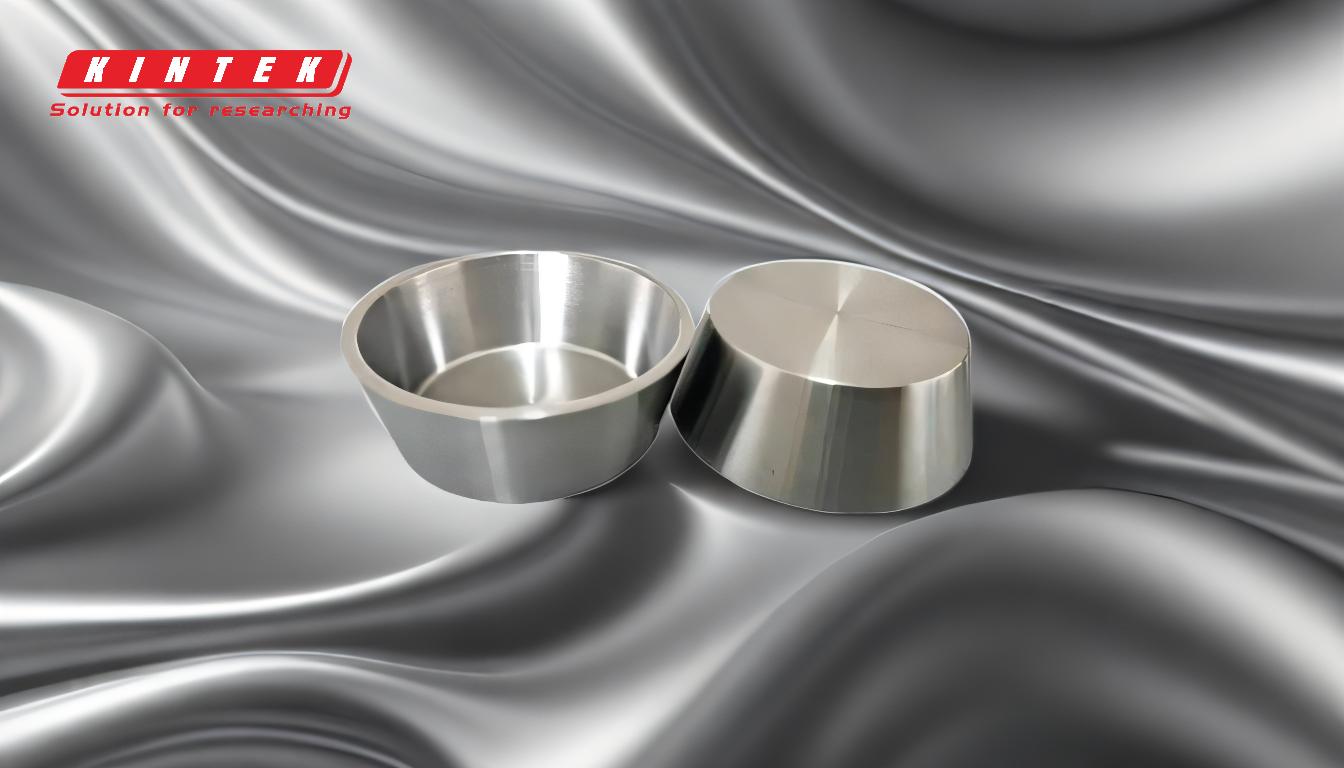
-
Chemical Deposition Methods:
- Chemical Vapor Deposition (CVD): This method involves the chemical reaction of gaseous precursors to form a solid film on the substrate. It is highly effective for producing high-purity, uniform ITO films with excellent electrical and optical properties.
- Plasma-Enhanced CVD (PECVD): PECVD uses plasma to enhance the chemical reaction rates, allowing deposition at lower temperatures. This is particularly useful for temperature-sensitive substrates.
- Atomic Layer Deposition (ALD): ALD offers atomic-level control over film thickness and composition, making it ideal for applications requiring ultra-thin, conformal ITO coatings.
-
Physical Deposition Methods:
- Sputtering: This is one of the most common methods for ITO deposition. It involves bombarding a target material with ions to eject atoms, which then deposit onto the substrate. Sputtering is favored for its ability to produce dense, uniform films with good adhesion.
- Thermal Evaporation: In this method, the ITO material is heated to its evaporation point in a vacuum, and the vapor condenses on the substrate. It is simpler and cost-effective but may not offer the same level of uniformity as sputtering.
- Electron Beam Evaporation: This technique uses an electron beam to heat and evaporate the ITO material, allowing for high deposition rates and precise control over film thickness.
- Pulsed Laser Deposition (PLD): PLD uses high-power laser pulses to ablate material from a target, which then deposits onto the substrate. It is known for producing high-quality films with complex compositions.
-
Selection Criteria for Deposition Methods:
- Substrate Compatibility: The choice of method depends on the substrate material (e.g., silicon, glass) and its thermal and chemical stability.
- Film Properties: Desired properties such as thickness, uniformity, conductivity, and optical transparency influence the selection of the deposition technique.
- Application Requirements: Specific applications, such as touchscreens, solar cells, or displays, may require particular film characteristics, guiding the choice of deposition method.
-
Advantages and Limitations:
- Chemical Methods: Offer excellent control over film composition and properties but may require higher temperatures and more complex equipment.
- Physical Methods: Generally simpler and more versatile, but may face challenges in achieving uniform thickness and controlling film composition at the atomic level.
By understanding these methods and their respective advantages, equipment and consumable purchasers can make informed decisions tailored to their specific needs and applications.
Summary Table:
Deposition Method | Key Features | Best For |
---|---|---|
Chemical Vapor Deposition (CVD) | High-purity, uniform films; excellent electrical/optical properties | High-quality ITO films for precision applications |
Plasma-Enhanced CVD (PECVD) | Lower temperature deposition; ideal for sensitive substrates | Temperature-sensitive applications |
Atomic Layer Deposition (ALD) | Atomic-level control; ultra-thin, conformal coatings | Ultra-thin ITO layers for advanced applications |
Sputtering | Dense, uniform films; good adhesion | High-performance ITO films for displays and touchscreens |
Thermal Evaporation | Simple, cost-effective; moderate uniformity | Budget-friendly ITO deposition |
Electron Beam Evaporation | High deposition rates; precise thickness control | Rapid ITO deposition with high precision |
Pulsed Laser Deposition (PLD) | High-quality films; complex compositions | High-performance ITO films for specialized applications |
Need help selecting the best ITO deposition method for your application? Contact our experts today for tailored solutions!