Thin film deposition is a critical process in various industries, including electronics, optics, and coatings, where precise control over material properties is essential. The methods of thin film deposition are broadly categorized into chemical and physical techniques, each with its own set of processes and applications. Chemical methods involve chemical reactions to form the film, while physical methods rely on physical processes such as evaporation or sputtering. The choice of method depends on the desired film properties, substrate material, and specific application requirements. Below, we explore the key methods of thin film deposition in detail.
Key Points Explained:
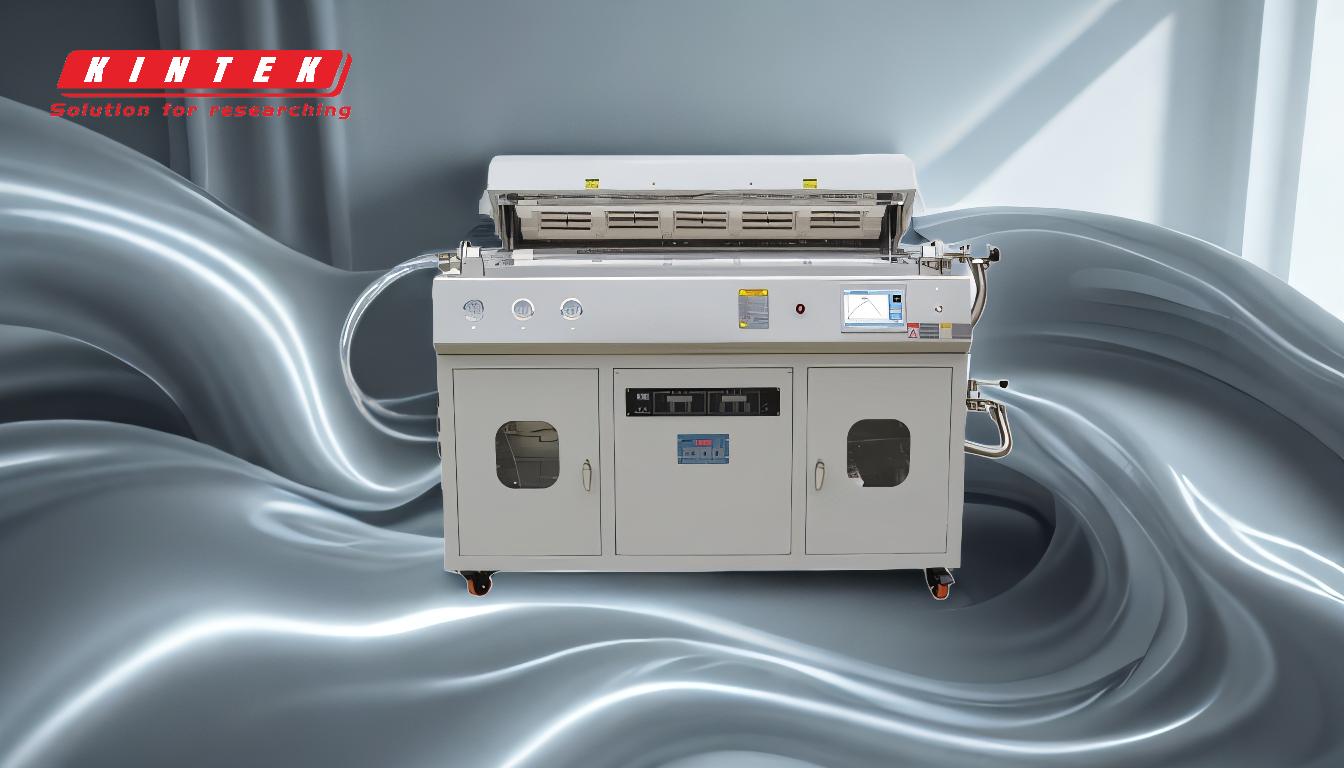
-
Chemical Vapor Deposition (CVD):
- Process: CVD involves the use of chemical reactions to deposit a thin film onto a substrate. Precursor gases are introduced into a reaction chamber, where they react or decompose on the substrate surface to form the desired film.
- Types: Common variants include Plasma-Enhanced CVD (PECVD), which uses plasma to enhance the reaction, and Atomic Layer Deposition (ALD), which deposits films one atomic layer at a time.
- Applications: CVD is widely used in semiconductor manufacturing, optical coatings, and protective coatings due to its ability to produce high-quality, uniform films.
-
Physical Vapor Deposition (PVD):
- Process: PVD methods involve the physical transfer of material from a source to the substrate. This can be achieved through evaporation, sputtering, or other physical processes.
- Types: Common PVD techniques include Thermal Evaporation, Electron Beam Evaporation, and Sputtering. Pulsed Laser Deposition (PLD) is another PVD method where a laser is used to ablate material from a target.
- Applications: PVD is used in applications requiring high-purity films, such as in the production of thin-film solar cells, decorative coatings, and hard coatings for tools.
-
Atomic Layer Deposition (ALD):
- Process: ALD is a specialized form of CVD that deposits films one atomic layer at a time. This is achieved by alternating the exposure of the substrate to different precursor gases, allowing for precise control over film thickness and composition.
- Applications: ALD is particularly useful in applications requiring extremely thin and conformal films, such as in the fabrication of advanced semiconductor devices and nanoscale coatings.
-
Spray Pyrolysis:
- Process: Spray Pyrolysis involves spraying a solution containing the desired material onto a heated substrate. The solvent evaporates, and the remaining material decomposes to form a thin film.
- Applications: This method is commonly used for depositing metal oxide films, such as those used in solar cells and sensors, due to its simplicity and cost-effectiveness.
-
Liquid Coating Techniques:
- Process: Liquid coating methods, such as spin coating and dip coating, involve applying a liquid solution or suspension of the material onto the substrate. The liquid is then dried or cured to form a thin film.
- Types: Spin coating is widely used in the semiconductor industry for depositing photoresist layers, while dip coating is used for creating optical coatings and thin films on complex shapes.
- Applications: These techniques are ideal for applications requiring large-area coatings or films with specific optical properties.
-
Electroplating:
- Process: Electroplating involves the deposition of a thin film onto a conductive substrate by passing an electric current through a solution containing the desired metal ions.
- Applications: This method is commonly used for depositing metal coatings, such as gold or nickel, on electronic components and decorative items.
-
Sol-Gel Process:
- Process: The sol-gel process involves the formation of a gel from a colloidal solution (sol) of the material, which is then dried and heat-treated to form a thin film.
- Applications: This method is used for depositing ceramic and glass films, particularly in the production of optical coatings and protective layers.
-
Molecular Beam Epitaxy (MBE):
- Process: MBE is a highly controlled PVD technique where beams of atoms or molecules are directed onto a substrate in an ultra-high vacuum environment, allowing for the growth of high-quality crystalline films.
- Applications: MBE is primarily used in the semiconductor industry for the growth of epitaxial layers in advanced electronic and optoelectronic devices.
In conclusion, the choice of thin film deposition method depends on the specific requirements of the application, including the desired film properties, substrate material, and production scale. Each method offers unique advantages and is suited to different types of materials and applications. Understanding these methods is crucial for selecting the appropriate technique for a given thin film deposition task.
Summary Table:
Method | Process | Applications |
---|---|---|
Chemical Vapor Deposition (CVD) | Uses chemical reactions to deposit films; includes PECVD and ALD. | Semiconductor manufacturing, optical coatings, protective coatings. |
Physical Vapor Deposition (PVD) | Relies on physical processes like evaporation or sputtering. | Thin-film solar cells, decorative coatings, hard coatings for tools. |
Atomic Layer Deposition (ALD) | Deposits films one atomic layer at a time for precise control. | Advanced semiconductor devices, nanoscale coatings. |
Spray Pyrolysis | Sprays solution onto a heated substrate; solvent evaporates to form a film. | Metal oxide films for solar cells and sensors. |
Liquid Coating Techniques | Includes spin coating and dip coating for large-area or optical films. | Photoresist layers, optical coatings on complex shapes. |
Electroplating | Deposits metal films via electric current in a solution. | Metal coatings for electronic components and decorative items. |
Sol-Gel Process | Forms films from a colloidal solution, dried and heat-treated. | Ceramic and glass films for optical coatings and protective layers. |
Molecular Beam Epitaxy (MBE) | Uses beams of atoms/molecules in ultra-high vacuum for crystalline films. | Epitaxial layers in advanced electronic and optoelectronic devices. |
Need help selecting the right thin film deposition method for your application? Contact our experts today!