Graphene production methods can be broadly categorized into two approaches: top-down and bottom-up. The top-down methods involve deriving graphene from graphite, such as mechanical exfoliation and liquid-phase exfoliation. The bottom-up methods, like chemical vapor deposition (CVD) and reduction of graphene oxide (GO), build graphene from smaller carbon-containing molecules. Each method has unique advantages and limitations, making them suitable for different applications, from fundamental research to industrial-scale production. This answer explores these methods in detail, highlighting their processes, benefits, and challenges.
Key Points Explained:
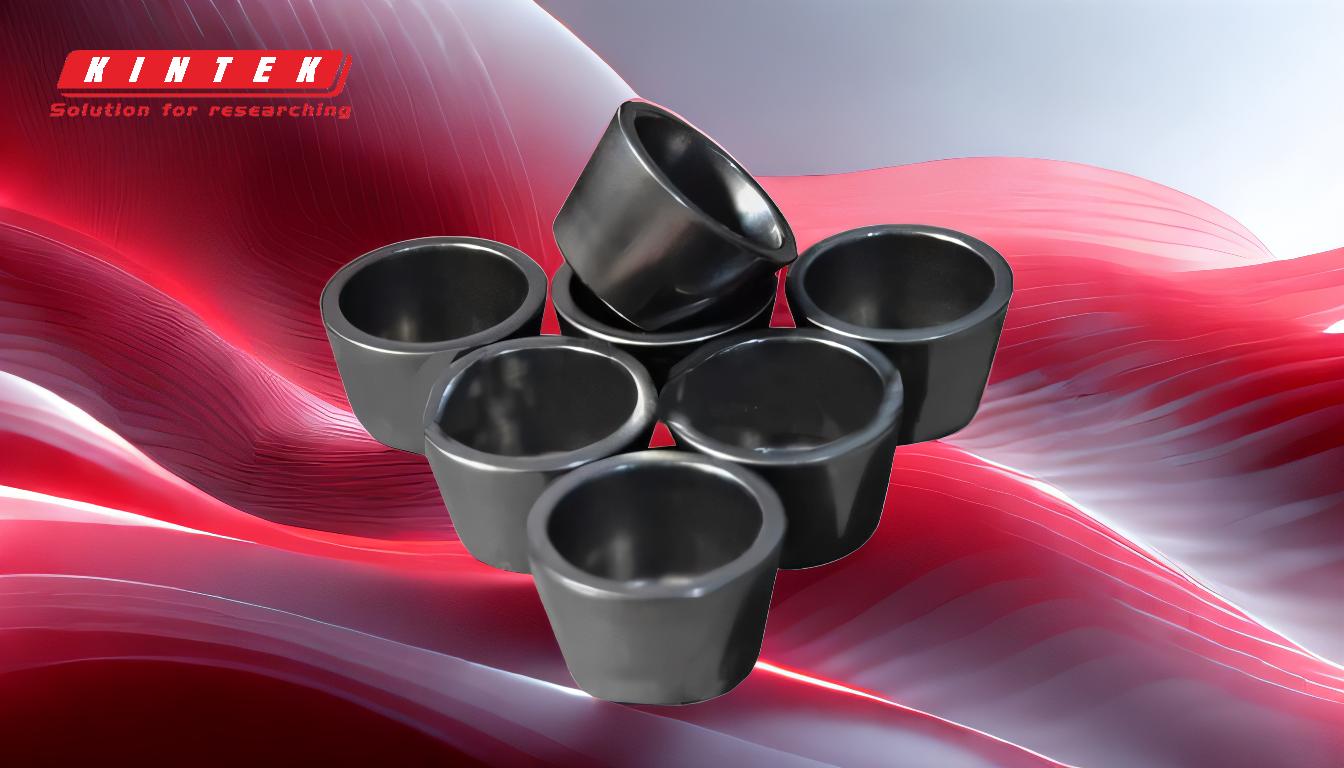
-
Top-Down Methods
These methods involve breaking down graphite into graphene layers:-
Mechanical Exfoliation:
- Process: Uses adhesive tape to peel off layers of graphene from graphite.
- Advantages: Produces high-quality graphene suitable for fundamental research.
- Disadvantages: Low yield and not scalable for industrial applications.
-
Liquid-Phase Exfoliation:
- Process: Graphite is dispersed in a liquid medium and exfoliated using sonication or shear forces.
- Advantages: Suitable for mass production and scalable.
- Disadvantages: Graphene produced often has lower electrical quality due to defects and impurities.
-
Mechanical Exfoliation:
-
Bottom-Up Methods
These methods build graphene from carbon-containing precursors:-
Chemical Vapor Deposition (CVD):
- Process: A carbon-containing gas (e.g., methane) is decomposed on a metal substrate (e.g., copper or nickel) at high temperatures, forming graphene layers.
- Advantages: Produces large-area, high-quality graphene with excellent electrical properties.
- Disadvantages: Requires expensive equipment and precise control of conditions.
-
Reduction of Graphene Oxide (GO):
- Process: Graphene oxide is chemically reduced to remove oxygen groups and restore the graphene structure.
- Advantages: Cost-effective and scalable.
- Disadvantages: Graphene produced often has structural defects and lower conductivity compared to CVD graphene.
-
Sublimation of Silicon Carbide (SiC):
- Process: SiC is heated to high temperatures, causing silicon atoms to sublimate and leaving behind a graphene layer.
- Advantages: Produces high-quality graphene without the need for a metal catalyst.
- Disadvantages: High cost and limited scalability.
-
Chemical Vapor Deposition (CVD):
-
Comparison of Methods
- Quality: Mechanical exfoliation and CVD produce the highest-quality graphene, while liquid-phase exfoliation and GO reduction often result in lower-quality material.
- Scalability: Liquid-phase exfoliation and GO reduction are more scalable, whereas mechanical exfoliation is limited to small-scale production.
- Cost: CVD and SiC sublimation are expensive, while liquid-phase exfoliation and GO reduction are more cost-effective.
-
Applications:
- High-quality graphene (CVD, mechanical exfoliation) is ideal for electronics and fundamental research.
- Lower-quality graphene (liquid-phase exfoliation, GO reduction) is suitable for composites, coatings, and energy storage.
-
Future Directions
- CVD Optimization: Efforts are focused on improving CVD processes to reduce costs and enhance scalability.
- Defect Reduction: Research is ongoing to minimize defects in graphene produced by liquid-phase exfoliation and GO reduction.
- Alternative Methods: Emerging techniques, such as electrochemical exfoliation and plasma-enhanced CVD, are being explored to address current limitations.
In summary, the choice of graphene production method depends on the desired quality, scalability, and application. While top-down methods are simpler and cost-effective, bottom-up methods like CVD offer superior quality and are more suitable for advanced applications. Ongoing research aims to bridge the gap between quality and scalability, making graphene more accessible for a wide range of industries.
Summary Table:
Method | Process | Advantages | Disadvantages |
---|---|---|---|
Mechanical Exfoliation | Uses adhesive tape to peel graphene layers from graphite | High-quality graphene for research | Low yield, not scalable |
Liquid-Phase Exfoliation | Graphite dispersed in liquid, exfoliated via sonication or shear forces | Scalable for mass production | Lower electrical quality due to defects |
Chemical Vapor Deposition (CVD) | Carbon gas decomposed on metal substrate at high temperatures | High-quality, large-area graphene with excellent electrical properties | Expensive equipment, precise conditions required |
Reduction of Graphene Oxide (GO) | Graphene oxide chemically reduced to restore graphene structure | Cost-effective and scalable | Structural defects, lower conductivity compared to CVD |
Sublimation of Silicon Carbide (SiC) | SiC heated to high temperatures, leaving graphene layer | High-quality graphene without metal catalyst | High cost, limited scalability |
Discover the best graphene production method for your needs—contact our experts today!