High-temperature ceramics are essential in various industries, including the medical field, where they are used in surgical implant devices like hip joints and knees. These ceramics are typically produced through sintering processes in high-temperature furnaces, where pure alumina powder is heated to temperatures as high as 2,500°F (1,371°C). The sintered powder is then processed further to create durable, biocompatible materials suitable for medical applications.
Key Points Explained:
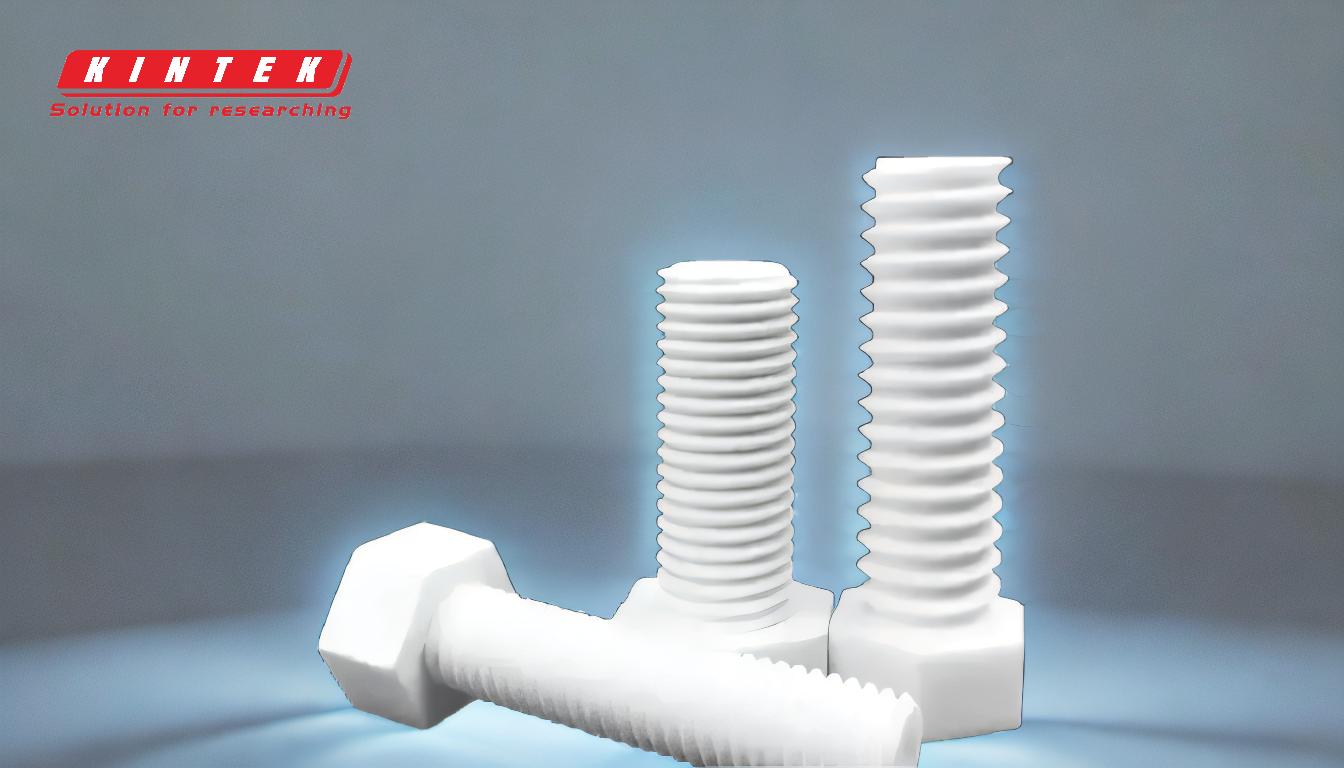
-
Sintering Process:
- Definition: Sintering is a method used to create high-temperature ceramics by heating powdered materials to a temperature below their melting point, causing the particles to bond together.
- Application in Medical Field: In the medical field, high-temperature furnaces sinter pure alumina powder at temperatures up to 2,500°F (1,371°C). This process is crucial for creating ceramic materials used in surgical implants.
- Benefits: The sintering process results in a dense, hard material with excellent mechanical properties, making it ideal for load-bearing applications like hip joints and knees.
-
Post-Sintering Processing:
- Separation of Hard Crust: After sintering, the material often forms a hard crust that needs to be separated from the rest of the sintered powder.
- Slurrying: The separated sintered powder is then slurried, which involves mixing it with a liquid to form a paste. This slurry can be applied to medical implant devices.
- Application to Implants: The slurried material is applied to the surface of medical implants, providing a biocompatible and durable coating that enhances the performance and longevity of the implant.
-
Materials Used:
- Alumina (Al₂O₃): Alumina is one of the most commonly used materials in high-temperature ceramics due to its excellent mechanical properties, chemical stability, and biocompatibility.
- Other Ceramic Materials: Besides alumina, other materials like zirconia (ZrO₂) and silicon nitride (Si₃N₄) are also used in high-temperature ceramic applications, depending on the specific requirements of the medical device.
-
High-Temperature Furnaces:
- Function: High-temperature furnaces are essential for the sintering process, providing the necessary heat to bond the ceramic particles.
- Temperature Control: Precise temperature control is crucial to ensure the quality and consistency of the sintered ceramics. Furnaces used in this process must be capable of maintaining temperatures up to 2,500°F (1,371°C) or higher.
- Types of Furnaces: There are various types of high-temperature furnaces, including electric, gas, and induction furnaces, each with its own advantages and limitations.
-
Applications in Medical Devices:
- Hip Joints: High-temperature ceramics are used in the fabrication of hip joint implants due to their wear resistance and biocompatibility.
- Knee Implants: Similarly, knee implants benefit from the use of high-temperature ceramics, which provide a smooth, durable surface that reduces friction and wear.
- Other Implants: Beyond hip and knee joints, high-temperature ceramics are also used in other types of surgical implants, such as dental implants and spinal fusion devices.
-
Advantages of High-Temperature Ceramics in Medical Applications:
- Biocompatibility: High-temperature ceramics are biocompatible, meaning they are well-tolerated by the human body and do not elicit adverse immune responses.
- Durability: These ceramics are highly durable and resistant to wear, making them ideal for long-term use in load-bearing applications.
- Chemical Stability: High-temperature ceramics are chemically stable, meaning they do not react with bodily fluids or tissues, ensuring the longevity and safety of the implant.
-
Challenges and Considerations:
- Cost: The production of high-temperature ceramics can be expensive due to the high energy requirements and specialized equipment needed.
- Processing Complexity: The sintering and post-sintering processes are complex and require precise control to ensure the quality of the final product.
- Material Selection: Choosing the right ceramic material for a specific application is crucial, as different materials have varying properties that can affect the performance of the implant.
In summary, high-temperature ceramics are produced through sintering processes in high-temperature furnaces, followed by post-sintering processing to create durable, biocompatible materials suitable for medical implants. These ceramics offer numerous advantages, including biocompatibility, durability, and chemical stability, making them ideal for use in surgical implant devices like hip joints and knees. However, the production of these materials involves complex processes and high costs, requiring careful consideration of material selection and processing techniques.
Summary Table:
Key Aspect | Details |
---|---|
Sintering Process | Heating alumina powder to 2,500°F (1,371°C) to bond particles. |
Post-Sintering Processing | Separating hard crust, slurrying, and applying to implants. |
Materials Used | Alumina (Al₂O₃), zirconia (ZrO₂), silicon nitride (Si₃N₄). |
Furnace Requirements | High-temperature furnaces with precise control up to 2,500°F (1,371°C). |
Medical Applications | Hip joints, knee implants, dental implants, spinal fusion devices. |
Advantages | Biocompatibility, durability, chemical stability. |
Challenges | High production costs, complex processing, material selection. |
Want to learn more about high-temperature ceramics for medical applications? Contact our experts today!