Chemical Vapor Deposition (CVD) is a sophisticated process used to deposit thin films of materials onto a substrate through chemical reactions in a controlled environment. The process involves activating gaseous reactants, which then chemically react to form a stable solid deposit on the substrate. The energy required for these reactions can be supplied by heat, light, or electric discharge. CVD is widely used in various industries due to its ability to coat virtually any surface with a strong chemical and metallurgical bond. However, it comes with challenges such as high temperatures, the use of toxic chemicals, and the need for precise control over process parameters. Understanding the key parameters of CVD is essential for optimizing the process and achieving desired material properties.
Key Points Explained:
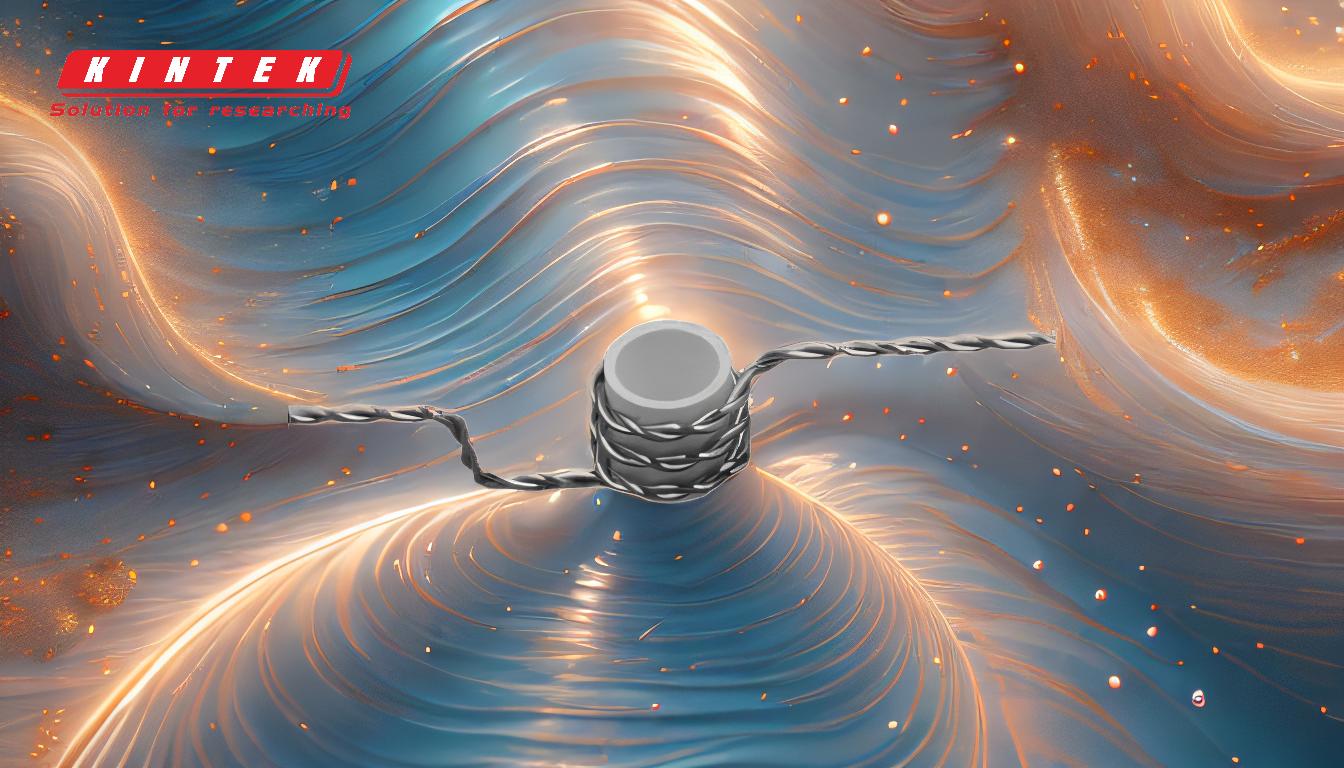
-
Activation of Gaseous Reactants:
- CVD begins with the activation of gaseous reactants, which are typically introduced into a reactor chamber. These reactants are often in the form of halides, hydrides, metal alkoxides, metal dialkylamides, metal diketonates, metal carbonyls, or organometallics. The activation process can be driven by heat, light, or electric discharge, depending on the specific CVD technique being used.
-
Chemical Reaction and Deposition:
- Once activated, the gaseous reactants undergo a chemical reaction, leading to the formation of a solid deposit on the substrate. This reaction occurs in a controlled environment, often within a vacuum or at atmospheric pressure. The vacuum helps to ensure that the reactants are evenly distributed and that the deposition occurs uniformly across the substrate.
-
Energy Sources for CVD:
- The energy required to drive the chemical reactions in CVD can be supplied by various sources:
- Heat: Thermal CVD relies on high temperatures to activate the reactants and facilitate the chemical reactions.
- Light: Photochemical CVD uses light, typically ultraviolet (UV) light, to initiate the reactions.
- Electric Discharge: Plasma-enhanced CVD (PECVD) uses an electric discharge to create a plasma, which provides the necessary energy for the reactions.
- The energy required to drive the chemical reactions in CVD can be supplied by various sources:
-
Temperature and Pressure Parameters:
- CVD processes are typically carried out at high temperatures, often around 1925 degrees Fahrenheit (1050 degrees Celsius). The temperature must be carefully controlled to ensure that the substrate can withstand the heat without degrading. Additionally, the pressure within the reactor chamber can vary, with some processes operating at atmospheric pressure and others under vacuum conditions.
-
Substrate Compatibility:
- One of the challenges of CVD is ensuring that the substrate can withstand the high temperatures and chemical environments required for the process. Some materials, such as certain polymers or low-melting-point metals, may not be suitable for CVD due to their inability to tolerate the extreme conditions.
-
Precursor Materials:
- The choice of precursor materials is critical in CVD. Common precursors include:
- Halides: Such as HSiCl3, SiCl2, TiCl4, and WF6.
- Hydrides: Such as AlH(NMe3)3, SiH4, GeH4, and NH3.
- Metal Alkoxides: Such as TEOS (tetraethyl orthosilicate) and TDMAT (tetrakis(dimethylamino)titanium).
- Metal Dialkylamides: Such as Ti(NMe2).
- Metal Diketonates: Such as Cu(acac) (copper acetylacetonate).
- Metal Carbonyls: Such as Ni(CO) (nickel carbonyl).
- Organometallics: Such as AlMe3 (trimethylaluminum) and Ti(CH2tBu) (titanium tert-butyl).
- The choice of precursor materials is critical in CVD. Common precursors include:
-
Challenges and Safety Considerations:
- CVD presents several challenges, including the need for extremely high temperatures, which can limit the types of substrates that can be used. Additionally, many of the chemicals used in CVD are toxic and require careful handling and disposal to protect workers and the environment. Companies must implement rigorous safety protocols to mitigate these risks.
-
Applications and Limitations:
- CVD is used in a wide range of applications, from semiconductor manufacturing to the production of protective coatings. However, it has some limitations, including a limited range of material usage, a loose tolerance range, and the need for post-coating finishing. Despite these limitations, CVD remains a valuable tool for creating high-quality thin films with strong chemical and metallurgical bonds.
By understanding these key parameters, manufacturers can optimize the CVD process to produce high-quality coatings and thin films for various industrial applications.
Summary Table:
Parameter | Details |
---|---|
Activation of Reactants | Gaseous reactants (halides, hydrides, etc.) activated by heat, light, or electric discharge. |
Energy Sources | Heat (thermal CVD), light (photochemical CVD), or electric discharge (PECVD). |
Temperature | Typically around 1925°F (1050°C), requiring precise control. |
Pressure | Operates at atmospheric pressure or under vacuum conditions. |
Substrate Compatibility | Must withstand high temperatures and chemical environments. |
Precursor Materials | Halides, hydrides, metal alkoxides, metal carbonyls, and organometallics. |
Challenges | High temperatures, toxic chemicals, and precise process control required. |
Applications | Semiconductor manufacturing, protective coatings, and more. |
Ready to optimize your CVD process? Contact our experts today to get started!